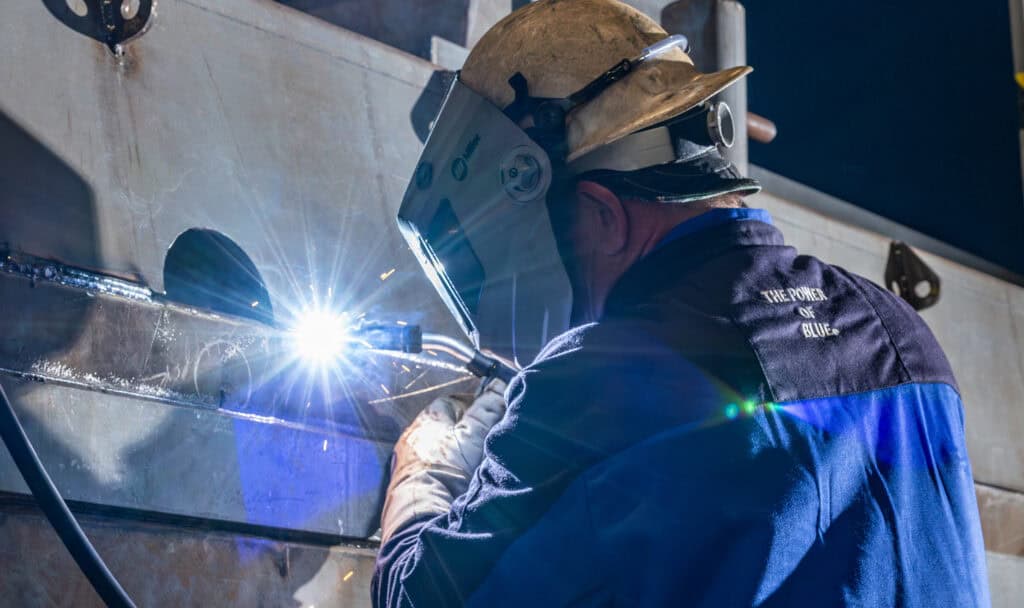
October 7, 2024
APPLETON – As a leading manufacturer of arc welding products worldwide, Nathan Leiteritz, group president at Miller Electric Mfg. LLC, said the company remains focused on customer-back innovation.
“That means our innovation starts with what the customer needs and works back toward solutions for and with them,” he said.
It is that very focus, Leiteritz said, that has Miller representatives traveling to Orlando, Florida, later this month for FABTECH 2024.
“FABTECH is basically the Super Bowl of the metal forming, fabricating, welding and finishing industries,” he said. “Our focus at FABTECH is customers in the manufacturing, fabrication and construction segments.”
Leiteritz said he’s looking forward to sharing Miller’s state-of-the-art welding solutions at FABTECH, as well as seeing those of others in the industry.
The event, he said, also provides an opportunity for companies to demonstrate that “by working together with our customers, we can strengthen the manufacturing industry, boost competitiveness and ultimately drive economic growth that benefits everyone.”
As an industry leader, Leiteritz said it’s vital for Miller to be a part of FABTECH.
“There, we have the opportunity to showcase our latest welding solutions – and we get to meet with current and prospective customers, all at the center of the action,” he said.
Leiteritz said Miller will showcase its latest welding and safety equipment at the Oct. 15-17 event – all of which aim to boost customers’ productivity, address their labor challenges and ultimately make them more competitive.
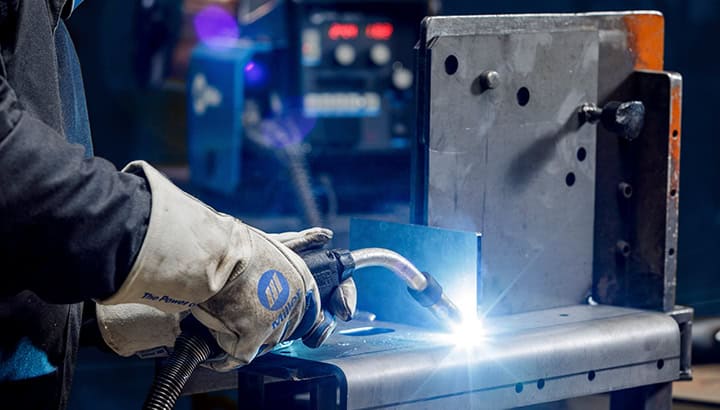
“It’s important for us to present a full array of solutions so our customers can find the best fit for their operation – from a small fabrication shop to a large national defense contractor,” he said.
Products/solutions
Some of the products and manufacturing, construction and fabrication solutions being highlighted at FABTECH, Leiteritz said include:
ClearLight™ 4x Lens Technology – available in all Digital Performance™, Digital Elite™, Digital Infinity™ and T94™ Series helmets – provides up to four times the clarity of welding helmets with 1/1/1/1 as per official USA ANSI certification of lens visibility.
With ClearLight, Leiteritz said welders can keep their helmets down between welding and non-welding tasks, improving safety and productivity.
“Safety and visibility to the weld are critical for manual welders, and our new ClearLight 4x Lens Technology incorporated into our welding helmets uses advanced high-definition optics to deliver clearer, brighter and more realistic views of the weld,” he said.
OptX™ Handheld Laser Welder, Leiteritz said, nearly eliminates the learning curve for beginner operators and raises productivity up to five to 10 times.
“This handheld welder uses laser heat and light instead of the electricity used in arc welders to create precise welds on lighter, thinner materials, like aluminum, that are used by aerospace manufacturers,” he said. “Coupling our deep welding process knowledge and critical safety sensors, accessories and training, Miller is changing the game, again, for precision welding.”
For manually operated welding systems, Leiteritz said Miller is showcasing the new Dynasty® 400 and 800 TIG welding machines with an intuitive LCD interface that simplifies TIG welding parameter selection and resultant arc and bead characteristics, as well as the Multimatic® 220 AC/DC with Wireless Foot Pedal, which simplifies cable management and improves safety.
Hercules™, Leiteritz said, significantly boosts productivity and deposition with a high-quality, single-wire automated solution.
“As our customers are continuing to deal with skilled labor shortages, they are looking to automation to help fill the gap – solutions like the Hercules™,” he said. “It is a complete system solution – including power source, gun and filler metal – designed together to dramatically boost productivity and deposition while keeping it simple as a single-wire MIG welding solution. Competitive solutions require more complicated twin or tandem wire solutions or even the submerged arc welding process, which adds more process complexity.”
With the advancement of collaborative robotics, or cobots – robots that work alongside a human operator – Leiteritz said the Miller Copilot™ system is a collaborative robotic welding system specifically designed for welding with intuitive controls and a simplified interface such that welders of all levels can amplify their skills and deliver high-quality, efficient welds.
Hobart® FabCOR® Elevate Filler Metal, Leiteritz said, delivers exceptional deposition rates and consistent feedability at high wire speeds for automated and handheld applications.
Trailblazer®330 Series is a lighter and smaller construction-ready, engine-driven welder with premium features and industry-leading arc performance.
Paired with remote Wireless Interface Control, Leiteritz said it eliminates the need to walk back to the machine – saving time and money on the jobsite.
The Air Pak™ model, he said, includes an integrated rotary-screw air compressor for expanded capabilities with an all-in-one solution.
Leiteritz said the Bernard® IronPro™ Self-Shielded FCAW Gun is ergonomically designed for optimal access and flexibility for hard-to-reach weld joints, along with a handle and trigger that retain less heat and keep out dust and dirt in harsh environments.
For generations to come
Each of these welding systems, Leiteritz said, is designed to be easy to use and learn – “making it simple for newer welders to step into their roles in hours and days rather than the weeks and months it traditionally took to master welding.”
“The experienced welders in the workforce are aging out and there aren’t enough new, skilled welders to replace them – so our customers need machines that are easy to learn and easy to use,” he said.
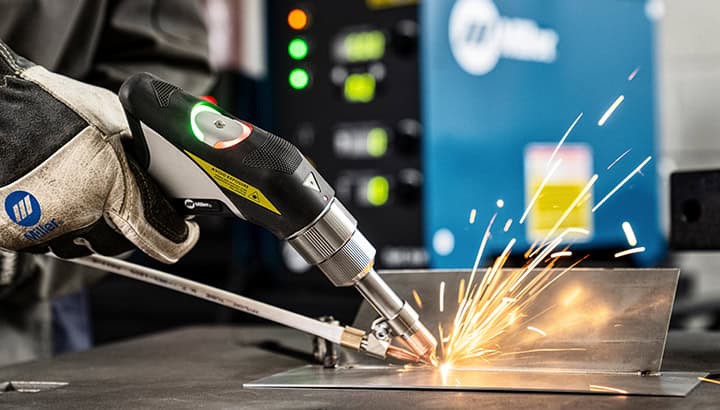
Leiteritz said the welding machines also need to create the same quality welds that someone with years of experience can achieve.
“It’s not just something that’s nice to have – these welds can hold together ships, airplanes and industrial machinery that depend on the weld,” he said.
By leaning on deep and long-standing customer relationships, Leiteritz said Miller is able to have “a finger on the pulse of the industry that continues to make us a leader in welding.”
“Together, we address their business challenges and develop and test solutions that meet their needs in both day-to-day operations and in the marketplace,” he said.
Wisconsin proud
Being able to showcase the best that Northeast Wisconsin has to offer at FABTECH, Leiteritz said, speaks to the character of the region – “our resourceful, innovative and entrepreneurial spirit.”
“FABTECH is a venue where we take the hard work that’s been done in Northeast Wisconsin and share it with customers whose operations can be revolutionized by these solutions,” he said.
The company that was started by a man (Niels Miller) in his basement during the Great Depression, Leiteritz said, was family-run and still remains a family-first culture – “and is now offering solutions to manufacturers around the world.”
Since getting its start in 1929, Leiteritz said Miller has invented and innovated welding tools that have stood the test of time.
“Miller takes the time to understand and solve real challenges, so when we release a solution, it’s exactly what the industry needs,” he said. “Our company builds reliable, durable machines that are made to last. Miller tests our products rigorously, so our customers get high-quality welds the first time around.”
Leiteritz said Miller also prides itself on the kind of customer service folks expect from a company based in Northeast Wisconsin – “hardworking and always has your back.”
“When our customers have questions, they can call our helpline and speak directly to the welding experts, here in Northeast Wisconsin, who design the product they’re using,” he said. “Our caring customer service team is with you every step of the way and empowered to do whatever it takes to solve your problem.”