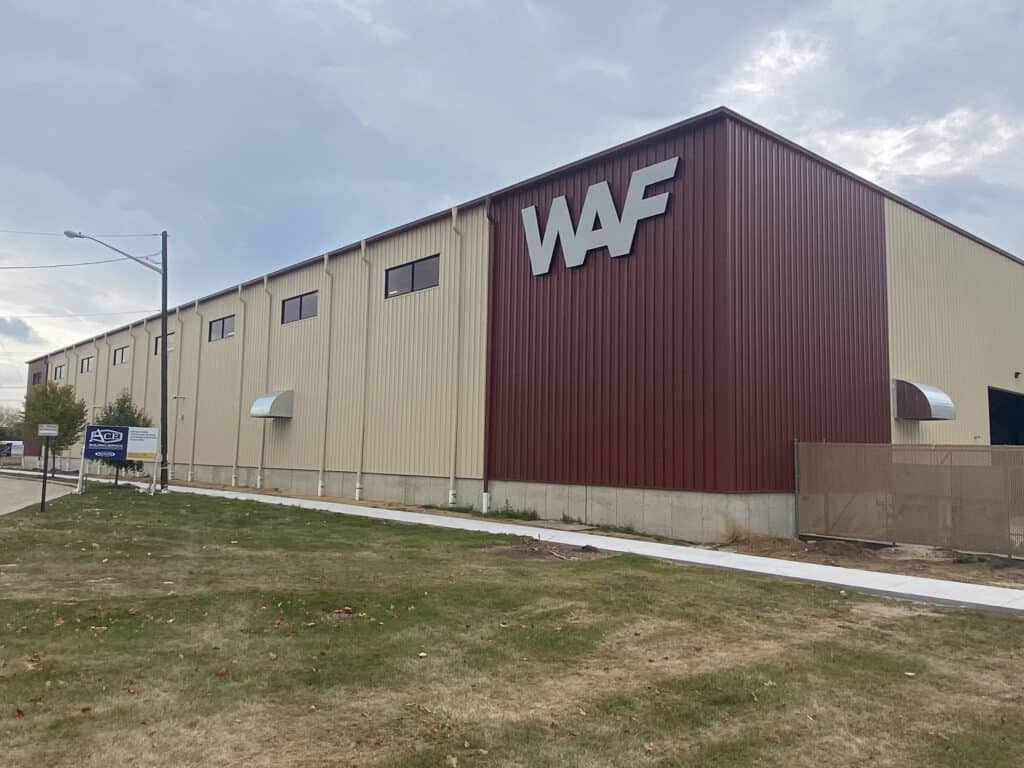
May 5, 2025
MANITOWOC – Wisconsin Aluminum Foundry (WAF), a high-quality aluminum and copper-based alloy castings design and manufacturing provider, has been named a finalist for the 2025 Manufacturing Leadership Awards.
The annual awards are presented by the National Association of Manufacturers’ (NAM) Leadership Council (MLC) – a division of the National Association of Manufacturers that helps manufacturers leverage digital transformation.
WAF’s project “How Wisconsin Aluminum Foundry Drove Energy Efficiency and Reduced Costs” was entered into the MLC’s Sustainability and the Circular Economy project category.
“(Being named a finalist) indicates that your project is among the industry’s most innovative and noteworthy as recognized by our expert judges,” Penelope Brown, senior content director for the Leadership Council, said, in letting WAF know of its award. “You are leading the way to a brighter future for manufacturing.”
Brown said the entry was submitted on WAF’s behalf by Gravity Climate, which will be recognized as a Partner in Collaborative Innovation.
Within the Partner in Collaborative Innovation category – according to NAM’s website (nam.org) – technology and consulting organizations and non-corporate organizations and institutions are recognized for their collaboration efforts and role in helping manufacturers achieve improvements in performance, processes and overall business value.
WAF is being recognized as a finalist in the Sustainability and the Circular Economy project category for its project with Gravity Climate – an end-to-end carbon accounting and energy management platform – aimed at improving energy efficiency in the aluminum melting process at WAF’s foundry in Crookston, Minnesota.
“We are honored to be selected as a finalist for this prestigious award,” WAF CEO Sachin Shivaram said. “We take an innovative, entrepreneurial approach to helping customers find solutions to their manufacturing challenges. In addition, our team takes pride in establishing positive, collaborative relationships with our partners. Those two things – innovation and collaboration – benefit everyone involved and make us all successful.”
Understanding its carbon footprint
Over the years, Shivaram said the regulatory environment has been growing to where all companies would eventually have to report what their carbon emissions are in three different categories:
- Scope 1 emissions – direct emissions that are owned or controlled by a company
- Scope 2 and 3 – indirect emissions, which are a consequence of the activities of the company, but occur from sources not owned or controlled by it
“Ideally, companies would be reporting their Scope 1, 2 and 3 emissions so we can all understand what our carbon footprint is,” he said. “As you can imagine, it’s very complicated, especially for a company of our size. We’re not a (huge company) where we have legions of accountants to do this stuff. So we were looking for a way that we could make the reporting process easier.”
Gravity, Shivaram said, has a software platform that automatically calculates all of a company’s Scope 1 and Scope 2 emissions.
“(They are) given access to invoices and operations, (and then) we tell them what kind of furnaces we’re running and so forth,” he said. “Then they automatically calculate it, in real time, without us having to do it – and for a much lower cost than we could do on our own. We’d probably have to employ three full-time accountants to do that.”
Shivaram said Gravity used WAF as a test pilot or guinea pig for some of its early technology, before it started selling the technology to several larger companies across the U.S.
Before long, he said Gravity started getting into more value-added consulting and made suggestions on how WAF could become more energy-efficient.
“They came up with a list of 10 projects we should do that would help us reduce our energy emissions, and in turn, our energy consumption, therefore our carbon emissions as well,” he said. “So we’ll save money – that was an intermediary thing they did.”
Then, Shivaram said Gravity took another step in telling WAF that, as part of the Inflation Reduction Act, there were federal programs that encouraged companies to do energy-efficient projects.
“If you do them, you could get this co-funding from the government,” he said. “But you have to go through an auditing process and have to contact what’s called an AIC and they vet your projects – and the only AIC in Wisconsin is at the University of Wisconsin-Milwaukee.”
Though it’s a “little complicated,” Shivaram said they will “hold your hand through the whole process.”

“Basically, all you have to do is sign your name, and you can participate in these federal programs,” he said. “So we went forward with a pretty significant replacement of a furnace at one of our facilities that was going to reduce our energy consumption. This was a project identified and brought to us by Gravity. They helped us do all the paperwork that would help us qualify for these federal grants.”
Project on pause
The accolade from the NAM, Shivaram said, is somewhat bittersweet, however.
This project, he said, received federal support through a Department of Energy program focused on small- and mid-sized manufacturers and is currently on hold because of executive orders from the new administration, which essentially pulled the funding as part of a broader federal spending review.
With the funding pulled, Shivaram said it’s unlikely they will do the project they had planned, which was to replace a furnace at one of their locations.
He said he is also uncertain how this new development will affect their award when the winners are announced in June.
“It doesn’t seem like it would make sense to give someone an award for a project that isn’t happening, but I just don’t know what will happen,” he said.
Shivaram said the project is not completely dead and WAF is looking at other options, but so far haven’t found any.
Shivaram said the furnace replacement project is lined up, but in the interim, with all that’s going on with the federal government right now, “they’ve canceled that whole program that the Department of Energy was funding.”
“And, on our own, we can’t do it,” he said. “We really needed that external grant to help make it viable for us. It’s a lot of money, and the payback just isn’t there… We want to become more energy-efficient and help the environment, but unfortunately, those projects are too costly for the savings that we get. It’s like a seven-year or 10-year payback. We don’t have unlimited capital, and we need to devote our capital to projects that have a quicker payback.”
Shivaram said he likened it to wind farm investments where, left to their own devices, developers wouldn’t likely do them, because the payback isn’t there, but incentives and the Inflation Reduction Act make those developments worthwhile and cost-effective.
Where to go from here
Shivaram said WAF is considering lenders that specialize in lending to environmental sustainability projects to help fund the original project.
“The reason you need specialized lending is because they’re taking a secured interest in your project and judging the viability of the project and savings,” he said. “We are talking to one lender, but in the end, we’re still going to have to borrow money and pay interest on a loan that we’re going to be repaying.”
In addition, Shivaram said there are other companies seeking loans from these specialized lenders for environmental-related projects they want to do.
So, he said, WAF is competing for lender dollars with other projects.
“To be honest, I feel it’s unlikely that we’ll borrow money to do this,” he said. “We’d still have to meet the same financial hurdles – it just doesn’t make sense.”
Shivaram said WAF will need to think creatively to get this done.
“We’d need to find somebody who has a vested interest in this happening,” he said. “It could be someone who makes an emerging technology that we haven’t considered for this furnace project and they’d want it to be a pilot program or something like that. Or maybe they’d want a test site, and they’d give us a discount on the equipment, or let us have it for free. Or it could be a customer who has a mandate to reduce their own carbon emissions and they’d be looking for an aluminum supplier who has a lower carbon footprint and thereby would be helping them meet their mandates.”
But the challenge, Shivaram said, is that ultimately companies need someone willing to pay money for an environmental outcome and the people who want that are generally going to be communities – local government or state government.
“And even if it’s a company that has a vested interest in us reducing our carbon emissions to meet their mandates, they must be getting some kind of tax incentive on their end,” he said. “And if they’re in America, I’m guessing that whatever made them care about reducing their carbon footprint, that incentive scheme is probably not there anymore either, for the same reason we don’t have ours. So the challenge is: how do you find someone willing to pay money for an environmental improvement?”
Shiavaram said the larger theme is that there is a different focus on where dollars are put from the previous administration to the current one.
“The appetite to spend money for an environmental improvement outcome is not there,” he said. “We’re caught in a situation that is one small glimpse of how that whole debate is playing out.”
Foundry industry still alive, well
Though the foundry industry has gotten a bad rap over the years, Shivaram said it is “getting a lot better,” and the state has a vested interest in it being better.
The foundry industry, he said, is somewhat of a millennia-old process.
“Pouring metal into a mold made of sand has truly been around for thousands of years, and some aspects of it have not changed,” he said.
Shivaram said Wisconsin is the most foundry-intensive state in the country.
“So, the foundry industry is a big deal in Wisconsin and hopefully, seeing a company like ours get an award for innovation helps people understand that even with this millenia-old industry, there’s a lot of neat stuff happening – high-end engineering,” he said, “and we’re keeping up with the times and offering our customers better and better products. That’s helping the state and is keeping this very vital industry still vibrant.”
Winners in all award categories, Shivaram said, will be announced at the Manufacturing Leadership Awards Gala, which will take place June 18 in Marco Island, Florida.
He said the gala is the closing event for “Rethink: Accelerating Digital Transformation in Manufacturing.”
Shivaram said all finalists will be recognized, receive a finalist trophy and be invited on stage at the event.
Additionally, because it was named a finalist, Shivaram said WAF has been automatically entered as a candidate for Project Category winner – which is given to the top-scoring project in each category; as well as for the Future of Manufacturing Award – which is given to projects that the judges and MLC leadership team have selected as distinctively innovative or futuristic.