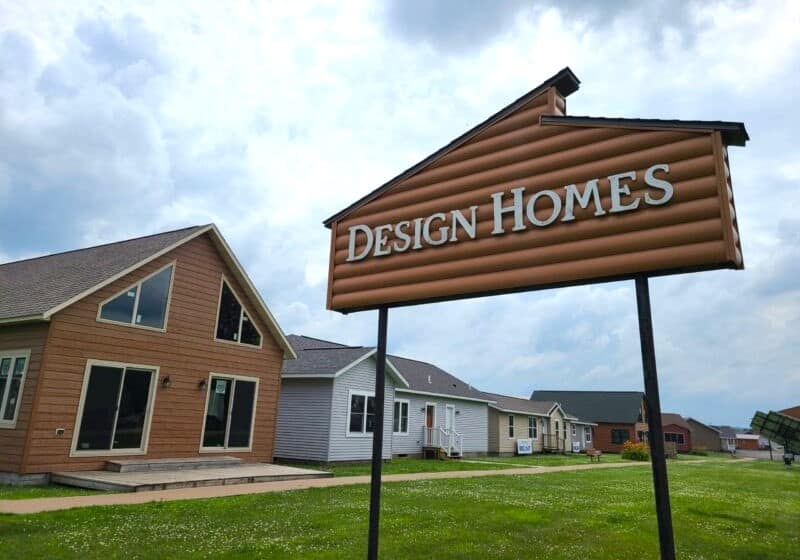
July 21, 2025
WEST CENTRAL WISCONSIN – Dale Strobach, sales manager with Design Homes, Inc., said for those looking for a more affordable house-building option – with the construction process not being weather dependent – a factory-direct model home might be the answer.
According to its website (designhomes.com), since beginning operations in 1966, Design Homes has built more than 19,000 homes in 10 states.
“Our unique policy of factory-direct sales makes your new home building process as straightforward and efficient as possible,” Strobach said. “Our sales staff located at each of our eight Midwest locations is here to help guide you each step of the way. Whether you’ve found a special deal in one of our pre-built, stock display homes, or are looking to construct your own custom plan, Design Homes can provide you with the very best home at the best value possible.”
With headquarters in Prairie du Chien, other Wisconsin locations include Chippewa Falls, Fond du Lac and Plover.
With a single location in Minnesota, Design Homes also has three locations in Iowa.
Strobach said Design Homes offers different-sized homes.
“That might be a 14-foot wide cabin or a 24- or 28-foot wide home,” he said. “In Wisconsin and Iowa, we even offer a 29-and-a-half-foot-wide option.”
Strobach said there is still a stigma with pre-built homes, but Design Homes doesn’t cut corners.
“When many people think of pre-built homes, they think of rectangular homes, plain, not fancy, paper-thin walls and cheap materials – that is not at all who we are,” he said. “We use the best materials like Kohler plumbing fixtures, Mohawk Flooring, Pella Windows, etc.”
The Design Homes’ staff, Strobach said, often receive positive comments from customers – especially when they’ve had bad experiences elsewhere.
“They’ll come here and say, ‘Wow, you guys really value quality compared to the last place I went to,’” he said. “They notice it for sure.”
Going back almost 60 years
Design Homes’ history goes back almost six decades, Strobach said, getting its start in 1966 when Owner Frank Weeks began the company.
Weeks, he said, liked the concept of being able to build a home inside an environmentally controlled setting.
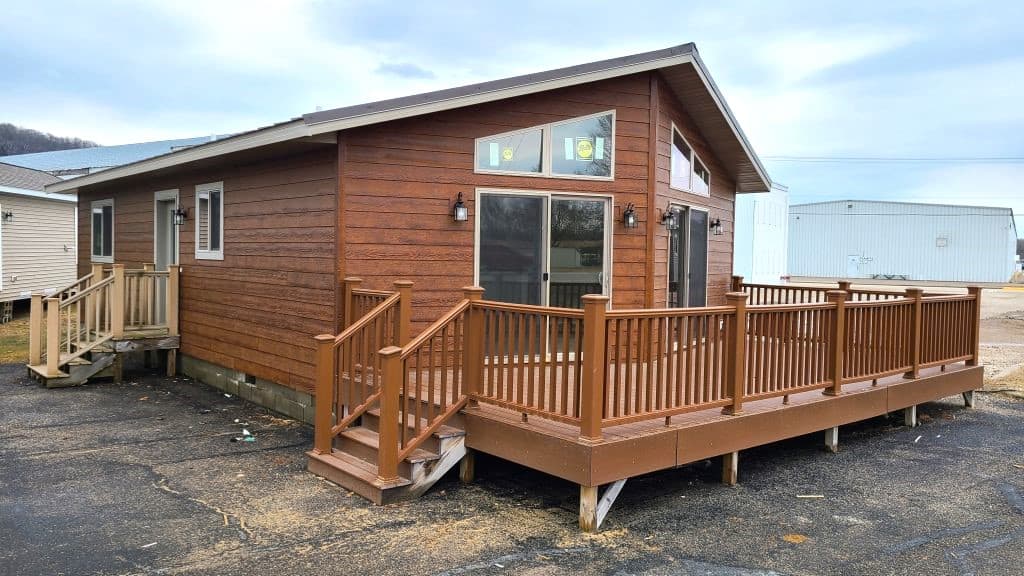
“After a section is built inside, the house is shipped in sections to the location, lifted in place and set on a foundation,” Strobach said. “That’s kind of how our process works. Design Homes requires either a crawl space or a basement for any of our structures – we can’t do anything on a slab.”
Customer’s responsibilities
Though Design Homes does much of the work to build and place a home, Strobach said some of the process needs to be completed by the customer.
These customer responsibilities, he said, largely include securing land, permits, financing, foundation and plumbing, hooking up to utilities and some other finishing touches.
“Of course, there are similar companies out there, but one of the big advantages we offer is that we build our homes for every one of our clients,” he said. “Due to this, we’re more flexible on layout and options. Other places might say, ‘We’ve got 15 houses to choose from – which one do you like?’”
Though he wouldn’t describe Design Homes’ options as “limitless,” Strobach said “we have a lot of options available to people.”
“We can customize if that’s what folks want, and we don’t charge for that,” he said. “We just need their ideas to fit within our limitations.”
Big benefits
Strobach said Design Homes’ structures provide customers with a variety of benefits, including more affordability.
Once customers lock in a price, he said that’s the price through the entire project.
“Thinking back more than five years ago, we were going through the COVID-19 pandemic,” he said. “Prices went through the roof – no pun intended. Our customers who ordered pre-COVID instantly gained about $40,000 in equity on their homes before it was even delivered, but we didn’t charge a nickel more.”
Because Design Homes are a lot easier to budget for, Strobach said lenders “love us.”
“Because we lock in the price, lenders know they don’t have to build in any fluff,” he said. “Whatever the contract says is what it stays, unless the customer wants to make changes.”
Strobach said Design Homes offers tours at its Prairie du Chien location, where all the building takes place.
“On average, we’re going to be 10-15% less [than a typical stick-built house], in terms of cost,” he said. “All of our homes meet or exceed stick build specifications. In other words, we have something called UDC (uniform dwelling code), and that’s what every site builder and Design Homes has to meet or exceed. We do that on all of our structures.”
Strobach said Design Homes are built just as soundly as a stick-built house.
“They have to be built to stand up to the forces of nature,” he said. “We over-engineer them for that reason. We also offer a one-year service warranty after it’s set on the foundation. If cracks form, doors need adjusting, etc., after the home settles on the foundation, customers have one year to claim things.”
With the homes being built indoors in a factory setting, Strobach said it allows for a much more efficient process.
“I used to build spec homes with a guy as a side gig,” he said. “In November, in Wisconsin, he’d say, ‘Dale, go out and shovel off that subfloor – it’s got three inches of snow on it.’ Then I’d have to grab some two-by-sixes under a tarp, and they were sopping wet. We’d be laying out walls and nailing them together, and water would shoot out when the nail shot in.”
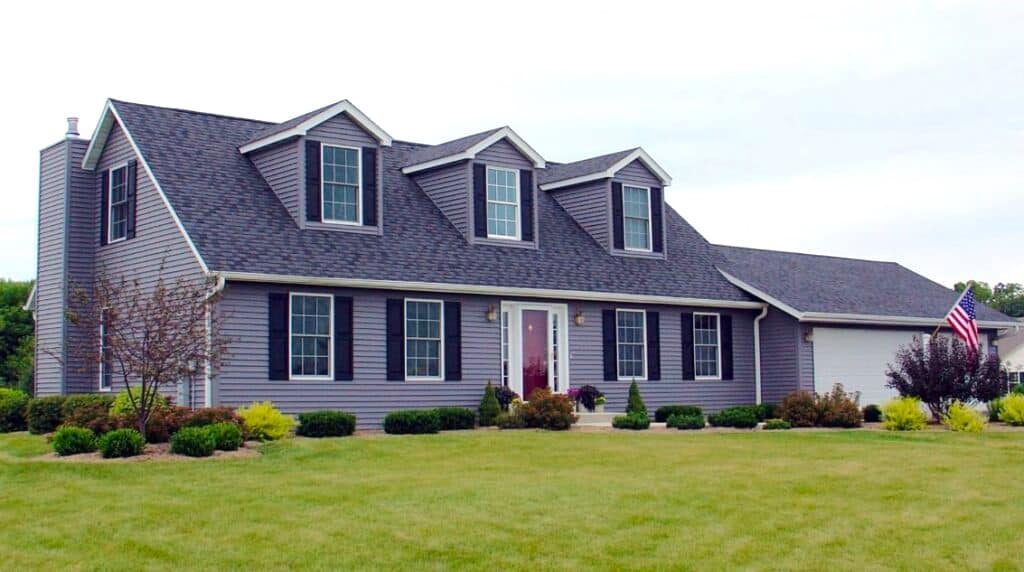
Strobach said in a nutshell, with the way houses are traditionally built, conditions are often not ideal – especially in Wisconsin.
“We were, at times, building in terrible conditions,” he said. “Once that wood – [if] it’s not treated – gets inside and dries out, it twists – then the drywallers had to deal with it. In our process, it’s always 65 degrees and dry through the entire process. Then it’s wrapped and sits outside ready for deliveries.”
How long does it take?
Though it varies, Strobach said currently, a Design Homes build takes about seven months to complete.
He said the lead time has reduced dramatically from a few years ago.
“We don’t tell people it will take four months and then add another six months on,” he laughed. “We don’t want ticked-off customers, so we are very upfront with our timeframes.”
Four years ago, Strobach said the lead time was up to 17 months.
“2021 was the perfect storm,” he said. “Interest rates were around 2.25%, and house values skyrocketed. In our situation, people were dumping their houses for a profit and then coming in and ordering Design Homes. We had more than a year’s worth of homes on our schedule and were doing maybe four or five a week.”
When taking in the entire process, Strobach said he feels seven months’ lead time is “very reasonable.”
“By the time you get done with your excavation, foundation and everything else, that seven months goes by quickly,” he said.
Once the home is delivered and put on its foundation, Strobach said there is some finishing work needed.
“[Finishing work] includes siding and some soffit and fascia work where the sections of the house come together,” he said. “That’s done by the finish crew. They usually show up two days to two weeks after the set crew finishes their part.”
When a Design Homes build is in place and the finishing crew does its thing, Strobach said it’s important to point out there are still other customer responsibilities.
“We don’t include appliances, a furnace or an air conditioner,” he said. “There is a base price, and much like buying a new car, if you’re going to add options to it from there, there is a total price. For example, if you want to switch from laminate countertops to quartz, you’re going to pay a little bit more. You can keep your house basic or beef it up a bit.”
Big differences
Strobach said there are big differences between modular and manufactured homes.
“Modular homes are built to state code (UDC in Wisconsin, IRC in other states) and become real property once they are set on the clients’ foundations,” he said. “They also appreciate in value over time, like a stick-built home.”
Strobach said manufactured homes are built to a less stringent HUD (U.S. Department of Housing and Urban Development) code.
“Manufactured homes have steel frames, aren’t necessarily intended to be put on a permanent foundation, are considered personal property and usually depreciate in value over time,” he said. “One style is an investment – the other is an expense.”