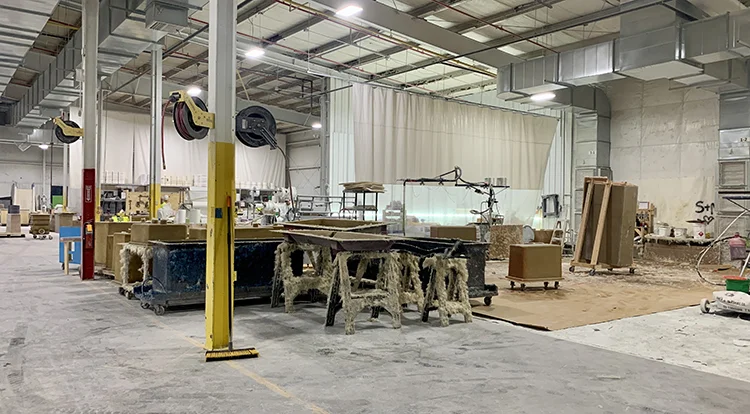
October 30, 2023
GREEN BAY – “Fiberglass is great because it lasts forever, but it’s also bad because it lasts forever.”
That’s the way Ben Bertram, co-owner of Fiberglass Solutions Inc., located at 995 Waube Lane in Green Bay, said is the best way to describe fiberglass – a fiber-reinforced plastic using glass fiber.
“It’s tough to recycle fiberglass,” he said. “I’m sure someone someday soon will find an effective way to recycle it – the product itself has a ton of benefits.”
Those benefits, Ben said, include being cost-effective, corrosion-resistant, strong and electrically non-conductive.
“Stainless steel is a good example to compare (it to), especially in the dairy industry,” he said. “Fiberglass and stainless steel are both corrosion-resistant products when it comes to chemicals, etc. However, stainless steel will rust in a cheese plant because the brine to make the cheese is all saltwater. If you put that brine in a stainless-steel tank, over time, you’ll have an issue with rusting. Fiberglass is clean and lasts a long time if taken care of. If you think of many boats sitting in salt water, they’re made of fiberglass.”
More about the business
Ben said Fiberglass Solutions has been around for almost 50 years.
The company was started by Norman Johnson in 1974 and specialized in boat repair and fabricating custom parts and tooling for the fiberglass boat industry.
From there, Ben said the company evolved and developed into a manufacturer of custom fiberglass-reinforced plastic products.
Ken and Mary Glowacki purchased the business in 2001 and renamed it Fiberglass Solutions Inc.
Ben, along with his wife Amy, purchased the business in 2018.
“When we bought the business, it was probably 70% dairy industry,” Ben said. “If you eat string cheese, asiago, parmesan, mozzarella, feta, etc., there’s a good chance it’s made in one of our brine tanks. We are in cheese plants all over the United States. We do commercial and industrial fiberglass.”
The company moved into its current location – a 33,000-square-foot facility on Waube Lane – in 2021 and has about 20 employees.
Ben said Fiberglass Solutions currently focuses on three facets of the business – contract manufacturing, custom manufacturing and service and repair.
“First, we do contract manufacturing for companies – 10 of these, 15 of those,” he said. “We also do custom manufacturing like the brine tanks for cheese plants … none of those tanks are the same, so they’re custom made to what the plants need. Lastly, we do service and repair. We’ve got trucks and trailers on the road every day of the week fixing fiberglass.”
Co-owner Amy said her husband always had a goal of buying a business.
“We looked at five or six businesses to purchase and decided Fiberglass Solutions was the best fit,” she said. “I do the finances, the purchasing, etc. We didn’t know anything about fiberglass when we started, but we’re learning more every day. There’s a lot of opportunities out there. We’re fortunate to have great employees.”
Ben said one of the unique aspects of the fiberglass business is “nothing with fiberglass is fast.”
“It’s an involved process,” he said. “If you call me and ask, ‘Can you build me a fender for my ’79 Ford F-150 – it should only cost a couple of hundred dollars.’ On our end, there would be hours upon hours into that process. With fiberglass, if you don’t have a mold, you have to build it from scratch. Once you build it, then you have to sand, paint, sand some more and then trim it.”
Other products
As part of the Greater Green Bay Chamber’s Manufacturing Month tours, the Bertrams showed members of the community how the process of making fiberglass works – starting from the finished product and going backward.
“If you have a recessed basement, we make the fiberglass window wells that look like slate,” Ben said. “We work with a local company out of De Pere on those. We also make a lot of mobile food carts for a company in Michigan. You’ll see these in hospitals, schools, etc. All of them are semi-custom, so that’s why a lot of fiberglass shops don’t want to take them on – we like that stuff. It works perfectly with our business model.”
When you watch the Green Bay Packers play at home – starting with the Oct. 29 game against the Minnesota Vikings – you’ll see some of Fiberglass Solution’s work on the sidelines.
“The Packers came to us with the 12 fiberglass benches that sit on the sidelines – six on each side,” Ben said. “They wanted to see if we could find a solution to get more heat or cold air up through the seats when the players are sitting on the benches. We cut some holes out of the benches and worked with another local company to make it happen. We also have to reinforce what’s underneath to hold several 300-pound guys sitting.”
Ben said Fiberglass Solutions currently doesn’t make the fiberglass benches, but that’s something it could do.
“We’d just have to make a mold for it,” he said. “That’s something we are going to look into. There are a lot of those benches in the professional and college ranks.”
Ben said another area Fiberglass Solutions works in is the pool industry.
“If you’ve ever gone in a big commercial pool, waterpark, etc., you’ve seen the grates on the bottom of the pool,” he said. “We make the pool filter boxes – that’s what’s underneath those grates. Those pool filter boxes are shipped all over the world. They are also semi-custom – everyone is a little bit different.”
To learn more about Fiberglass Solutions, visit fiberglasssolutions.us.