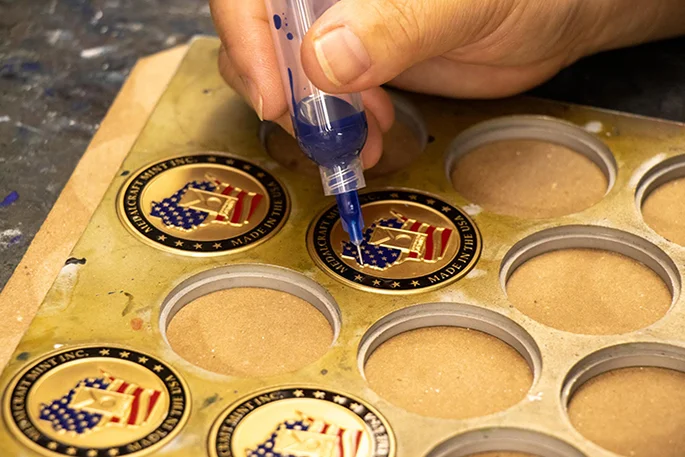
April 5, 2023
GREEN BAY – Medalcraft Mint’s origins date back 75 years to a blacksmith shop in Kewaunee.
Since then, the manufacturing company continues to specialize in a number of medallic needs, however, who they work with and how they do it has evolved significantly over the decades.
“We like to say we’re a U.S. manufacturer specializing in custom medals, challenge coins, military insignia and medallic needs,” Company President Jerry Moran said. “We’re making a piece of art.”
Moran purchased the company located at 2660 W. Mason St., Green Bay about 17 years ago, and said he set out to position it for future viability.
Prior to that, he said the company had always made a good product, but about 80% of its sales were through distributors.
The economic recession in 2008-09, Moran said, also prompted the company to evaluate its target customers.
At the time, he said the majority of its products were sold for corporate recognition.
“The reality is, when companies’ budgets get a little tight, what do you stop doing?” he said. “Much of the work we had with companies in 2008 dried up and went to China. So, we did some soul searching on what to change in how we did business.”
Diversified customer base
In the ensuing years, Moran said Medalcraft pursued work in a variety of sectors to diversify its customer base.
Today, Moran said 35-40% of business is in government work – with the Pentagon, Capitol Hill, Congress, etc. – outgrowths of his efforts to start the company’s government sales division in 2009.
That includes producing the Official Inaugural Coin for George W. Bush, as well as inaugural coins for former Presidents Barack Obama and Donald J. Trump.
Another 15-20%, Moran said, is in military insignia work, creating medals soldiers wear on their uniforms.
Entering that market, Moran said, involved significant work to become an approved vendor through the Institute of Heraldry, which Medalcraft did in 2015, enabling the company to produce military insignia.
“That opened doors we weren’t in, and now we are a pretty good player in that market,” he said. “They like we’re sitting in the Midwest because most of the players are in the Northeast (region).”
Moran said that work was further bolstered by Medalcraft’s purchase of Medallic Art and Mint, formerly two companies – Medallic Art Company and Northwest Territorial Mint – in 2018.
A Medalcraft Mint employee hand polishes a large bronze medallion. Submitted Photo
The move, he said, made Medalcraft Mint the largest private mint in North America, with that work folded into the Green Bay operation.
“That company specialized in college and university business, and we wanted that business because, in our minds, it was recession-proof,” he said. “That is until the COVID-19 pandemic hit and shut down universities and colleges.”
After a temporary hit, Moran said, fortunately, that business has rebounded and now comprises 15-20% of Medalcraft’s business.
He said the remainder is sprinkled throughout the corporate world and a bit in distribution, albeit in a small way.
“So, in the past 10 years, we have revamped our customer base, making us a lot healthier and setting us up for the future,” he said. “So when you ask, why are you still around? We had to change or we wouldn’t be around.”
Business evolution
In 2016, Moran said the company embraced further automation in its enameling work by adding three robots to the company roster to increase its speed to market even further.
“The product we make has a lot of hand touches, and that makes us unique,” he said. “But wherever you can use automation, we’re striving to do so, and that includes enameling of coins. The majority still (receive) hand finishing after, but it’s greatly reduced.”
Automation, Moran said, is also being incorporated into ribbon folding for military insignia.
In addition to being intentional about diversifying the business, Moran said he invested in improving both the process and production of coins and in turn expanding the company’s product capabilities.
He said he allotted monies annually to eliminate bottlenecks and improve the process.
“When I acquired the company, the majority of our dies were hand cut, taking about eight days to cut one die,” he said. “Today, all our dies are CNC cut and can be cut in three to eight hours. That’s a substantial reduction in the time required, and important as we’re doing 2,000 dies a year.”
What has remained consistent throughout the business’s evolution, Moran said, is both company culture and a focus on creating a quality product.
“The biggest thing separating us is the quality of the product, and that comes from the quality of our employees,” he said. “They take their work seriously and enjoy making the product, and (we) work hard to maintain our culture.”
Moran said the employee base is, like most businesses, a mix of long-standing employees and newer ones – all working in an environment that strives to be inclusive, positive, collaborative and rooted in recognition for a job well done.
Next big project
Moran said the company is excited to soon be working on another new endeavor, which is set to officially launch this summer.
He said Medalcraft was approached by Renaissance Reliability, LLC, a company that focuses on managing assets and keeping equipment consistently operable to increase uptime, in turn increasing efficiency, opening capacity and adding profitability.
Its CEO, Williams “Bill” Leahy, partnered with the University of Tennessee-Knoxville and accredited a reliability engineer certification.
Part of Renaissance Reliability’s mission also includes helping veterans transition successfully to civilian life and reducing the veteran suicide rate.
The organization also highlights manufacturing and defines what “Made in the U.S.A.” means.
Jerry Moran said wherever the company can, it uses automation, which includes enameling of coins. Submitted Photo
Medalcraft will host transitioning veterans onsite in June, July and August while they go through the reliability engineer certification.
“When they are completely discharged, (the goal) is for them to be more equipped for life in the civilian society,” Moran said. “A program like this has never been done before, and we are all excited about it. (Renaissance Reliability) came to us as a U.S.A. manufacturer, and one who makes a product every military person resonates with.”
Moran said the company sees this opportunity as a progressive step to supporting another segment of the population.
For years, Moran said Medalcraft had worked with Aspiro to provide project work for individuals with disabilities to perform at Aspiro’s facility.
He said the company became one of the first participants in Aspiro’s Group Supported Employment (GSE) program in 2020, which involves having workers with disabilities coming onsite to Medalcraft (as well as other employers) to work, accompanied by an Aspiro staff member who serves as their job coach.
The individuals gain work experience toward community-integrated employment, increasing their independence and self-esteem, and employers’ benefit from productive employees.
“Fast forward to today, and we can’t be happier,” Moran said. “A mix of 10-11 people comes in from 9 a.m. to 2:30 p.m. Monday through Friday. We have hired one of the (individuals in the program) and are looking to hire two more. They do a good job, and they are wonderful. The clients have formed strong bonds with employees in other departments.”