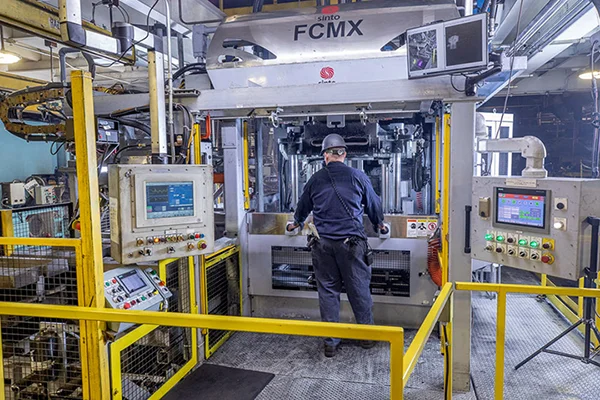
April 21, 2023
WAUPACA – There are two ways to cast iron – in vertical molds or horizontal molds.
In its 100-plus-year history, Waupaca Foundry has worked with both.
However, in the most recent years, the foundry’s focus has been on vertical molds – which Vice President of Engineering Jarrod Osborn said are designed for speed and work best on less complicated castings.
“We literally are the world’s leader in casting iron via vertical molding – that means parts going to automotive, diesel, off-highway and other heavy-duty customers,” he said.
The foundry installed its first vertical molding machine in 1967, and by the early 1990s, the last of the horizontal molding machines were removed.
However, for the first time in more than 30 years, the iron casting supplier has reintroduced horizontal molds to Plant 1.
“We are constantly looking to add innovative features that add safety, quality, productivity and reliability – (the horizontal mold is one of those),” Osborn said.
The why
Todd Pagel, vice president of operations, credits the foundry’s expanded production capabilities as the driving force behind the installation of the new horizontal line, which he said is best for large, complex and lower-volume iron castings.
“There are certain castings that are more challenging to cast vertically than they would need to be in rising and gating (which are processes used in foundries),” he said. “As soon as you part a casting horizontally, you can riser and gate in ways not possible with vertical. Some are cost-prohibitive to produce vertically, and some are just better horizontally – it is all about a difference in the way the casting is actually produced.”
Recognized as a leader in green sand vertical molding, Mike Nikolai, president, COO and CEO of Waupaca Foundry, said expanding production back into horizontal molding options will help diversify the company’s portfolio.
“We are making this investment as a direct response to customer demand,” he said. “We have made strategic capital investments in key areas of production, including the use of material handling automation, now we are adapting to customer needs by offering both horizontal and vertical molding.”
Expanded capabilities
Installation of the new line – a Sinto Horizontal Molding Machine, the first in operation in the U.S. – began in February, and officially joined the production process following a first-pour event April 18.
James Newsome, vice president of sales and marketing, said the production expansion directly addresses the concerns of customers.
“Waupaca Foundry has a strong reputation for high-volume production,” he said. “By adding horizontal molding, our customers have a solution for value-added services to produce low-volume, complicated parts.”
Newsome said the new machine allows Waupaca Foundry – North America’s largest iron foundry – to respond to customers’ tight deadlines, becoming a “one-stop shop.”
Although the foundry is replacing a 22 x 34 vertical molding machine at Plant 1 with the new horizontal molding machine, Pagel said the two machines, and their space needs, are not identical.
Over the course of the last few months, he said a number of different layouts were considered.
Overall, Pagel said the new footprint and total real estate required are slightly greater than the old, but it is due to the handling line, not the actual machine.
He said much work and preparation was done to fit the entire line wisely and well into virtually the same space with minimal disruption to anything else.
David Scott, director of tooling and process manufacturing, said Waupaca Foundry engineering, maintenance and operations have been working closely with the Sinto team through the design, build, installation and commissioning of the machine.
//tbnapp.cdn.bubble.io/f1682105413112x496193058207572860/richtext_content.webpThe new horizontal molding production line enables Waupaca Foundry to respond to customer needs, even in an emergency supply constraint. Photo Courtesy of Waupaca Foundry
“Waupaca Foundry has a strong, in-house technical workforce that ensures a quick adoption of the new technology and process that will drive its success,” he said.
Scott said the machine has been running a limited number of hours daily to test and debug the molding, pouring, mold handling and shakeout process.
“While running the machine and testing the processes, we were also validating individual part-specific patterns,” he said. “Over the next several weeks, we will continue to increase the run hours and molding speed.”
Scott said the newly installed molding machine is the fastest flaskless horizontal match plate machine available on the market at 200 molds per hour and features pattern changes within a single-mold cycle.
“The speed of the machine combined with zero downtime for pattern changes allows for efficient operations with low volume iron casting production,” he said.
Historically, Osborn said pattern tooling for a cast part was unique to both the part and the machine.
“However, Waupaca Foundry has invested in adapter plates that allow existing flaskless match plate patterns of equal or smaller size tooling to be used rather than investing time and expense to develop new tooling,” he said. “By using adapter plates and customer’s current tooling, production and PPAP (production part approval process) can be completed in a few days – compared to weeks – and months-long program launches.”
Osborn said this enables Waupaca Foundry to respond to customer needs, even in an emergency supply constraint.
Headquartered in Waupaca, the foundry has 1.4 million tons of capacity across 29 vertical and one horizontal molding machines.
Every day, 4,000 Waupaca Foundry team members melt 9,500 tons of durable, gray iron castings, ductile iron casting and high-strength ductile iron castings in foundries located in Wisconsin, Michigan and Indiana.
With the addition of horizontal molding, Newsome said Waupaca Foundry is positioned to produce a wider variety of cast iron parts.
“The foundry will be able to function more as a ‘one-stop shop’ for customers who source cast iron parts suited for both vertical and horizontal molding,” he said. “The horizontal molding capacity will streamline manufacturing supply chains and benefit from the quality and service they have long experienced from Waupaca Foundry.”