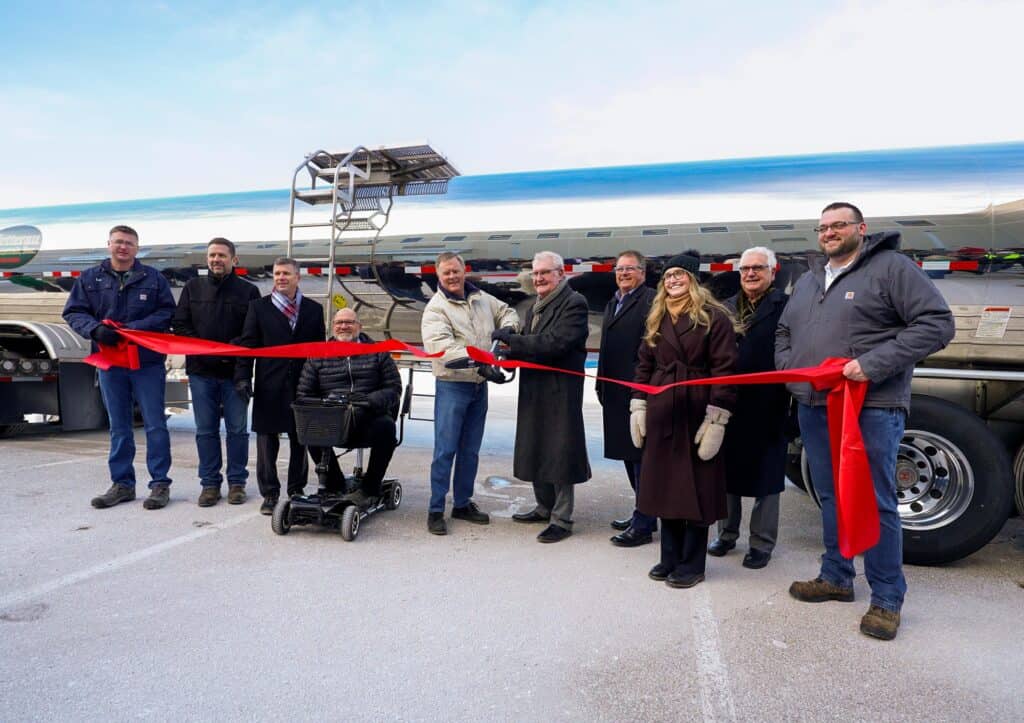
January 27, 2025
NEENAH – Got milk?
Galloway Company, a dairy ingredient manufacturer based in Neenah, sure does – especially after the completion of its recent $70 million expansion.
Galloway employees gathered in mid-January to celebrate its newly completed facility with a ribbon-cutting ceremony – dedicating its new milk evaporator to its loyal customers.
“We want to delight our customers, so they can delight theirs,” Tim Galloway, former president/CEO and current chairman of the board, said. “Therefore, we dedicate this evaporator to our customers… who put faith in us to be their supplier of choice.”
Tim said the last time Galloway Company dedicated a milk evaporator was in 1988 when its founder – his grandfather, Edwin P. Galloway – was 97 years old.
“I think (Edwin’s) three sons – Ned, John and Dick – would be proud today, too, that the third generation helped build a growing company that could support (establishing a) new milk evaporator 37 years later,” he said. “Now, we have a fourth generation in place to continue the legacy.”
Leading the way for that fourth generation is Annika Galloway – director of communications and PR – who said now is an especially exciting time to be part of her family’s company.
“I think it’s so rare for family companies to be in such a future mindset when (the current) generation is retiring,” she said. “So for me to come (after) generations that have set us up for such quick progress in the future, I really couldn’t ask for a better way to enter the business.”
Efficient expansion
Troy Youngbauer – Galloway’s COO – said the decision to expand was made about three years ago.
Following a year-and-a-half of construction, Youngbauer said it took more than a month before the product produced by the new facility was ready to be sold.
“We made our first product about 45 days ago, so we had it in shelf-life testing waiting for it (to be ready),” he said.
The morning of the celebratory ribbon cutting, Annika said the “very first load” of customer product processed through the new facility was dispatched in a tanker truck.
“That’s all local, family farmed milk, too,” she said. “We go through different co-ops, which is awesome.”
Now, for the first time in four years, Annika said Galloway has the capacity to take on new customers.
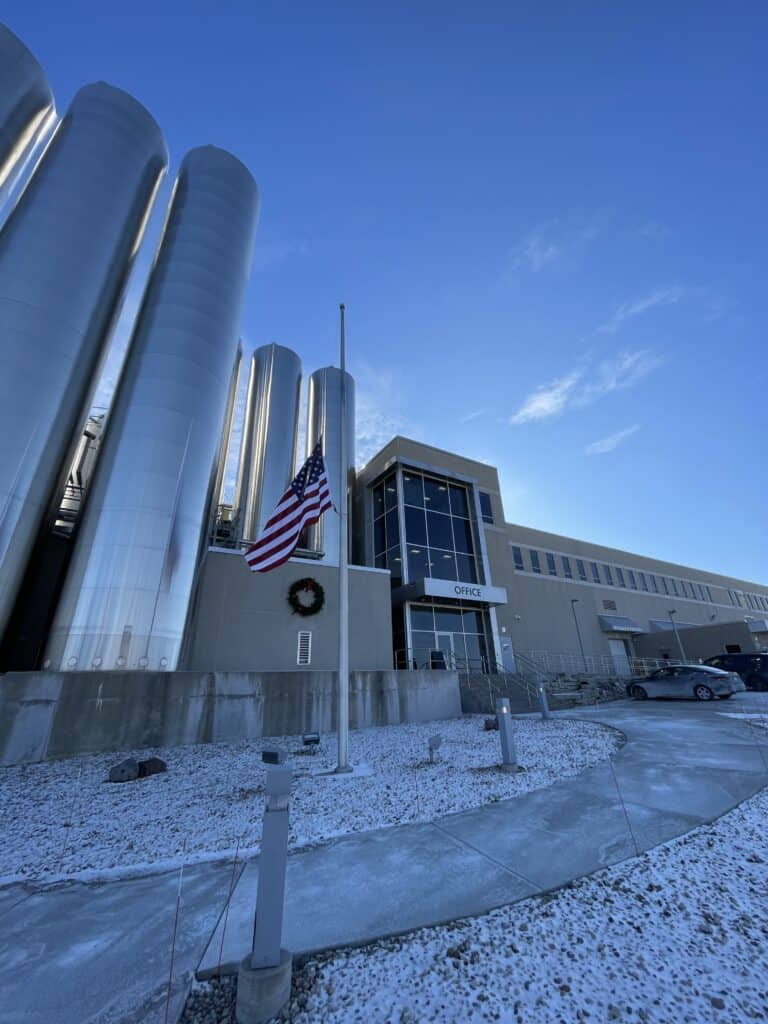
“Some of our very loyal customers have wanted to buy more (products) from us, but we just (didn’t) have the capacity,” she said. “So they have known about this project, and we’ve been able to increase their orders before we opened it up to the public.”
With relatively little space to stretch into, Annika said the 41,211-square-foot expansion was an interesting logistical challenge for the company.
“The old evaporator is just on the other side of the staircase,” she said. “It’s interesting how we’ve been able to expand in such a small footprint being so landlocked in Neenah – it all becomes very condensed, so we’ve only ever had the one facility.”
Increased clientele, however, means more manpower is required to serve their customer’s dairy ingredient needs.
“In the next year, we expect to add 20 new positions, but those aren’t necessarily (for) operators,” she said. “It’s all the other business implications that an expansion brings on.”
A unique challenge Galloway experienced in its niche industry, Youngbauer said, was an equipment shortage, not a workforce shortage like many other manufacturing industries are experiencing.
“We basically can run it with the same operators that we had before,” he said. “We probably added four or five positions just to support and give ourselves a little more flexibility. As we grow into it we may have to add more, but for now, it’s a pretty minimal headcount honestly.”
Part of the reason why Galloway Company can operate on a minimal headcount, Youngbauer said, is because of how hard its operators and engineers have worked to make the evaporation process as efficient as possible.
For example, he said the new evaporator has Clean In Place (CIP) capabilities.
“Basically, we can do everything in the machine – we can clean without manual interaction,” he said. “The system will clean itself.”
Operator-first approach
Chris Olson, process owner at Galloway, said when the company decided it was time for expansion, the goal was to increase the facility’s overall capacity by 150%.
“We started this process with the idea that we wanted to make the new evaporator about one and a half times the size of our current evaporator,” he said. “So (now) we have a 250-million-pound capacity.”
Olson said the new facility also allows for an evaporation process that makes the operators’ jobs easier.
“A big start-up with this project was (asking operators) what are the things we do really well on our current evaporator and what are the things they don’t like doing anymore,” he said. “(They are) probably where the majority of these ideas came from.”
Olson said one of the “bigger changes” derived from the expansion involved the facility’s powdered milk process.
“(With) our old system, operators had to carry two, 27 pound bales up three flights of stairs to the top,” he said. “Now we have a system that air conveys it for us.”
Operator input, Olson said, was at the forefront of his mind as he and the engineers tackled the massive project.
“When we started this project, I had at least one operator with me for pretty much 75% of the meetings I was in,” he said. “He was keeping me in line with some of the things that they were looking for, too, because that’s a big part of it… What makes sense to me on paper sometimes doesn’t make sense to the guy that’s doing the job.”
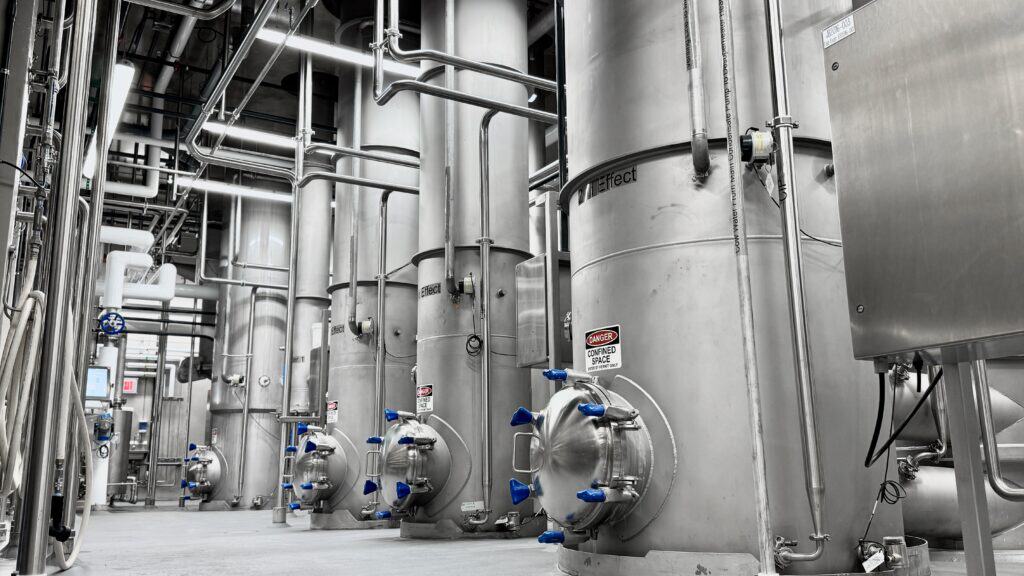
Though there are slightly new systems and processes for operators to learn, Olson said much of what the company implemented in the new facility was already tried and tested in its first evaporator across the stairwell.
“Every idea was replicated over here from our last evaporator with minor upgrades,” he said. “Sometimes, there’s just a more efficient way of doing it.”
Olson said Galloway’s first-ever electronic charting system also contributes to the facility’s efficiency – which allows operators to check their charts from their desk.
“Pretty much everything that we’ve done on the system is set up so you can push a button and it does it for you,” he said.
After everything in the new facility was operational, Olson said it took roughly two passes through the new process for products produced in the new evaporator to be considered “in-spec.”
“I think our last seven runs were all in-spec, so within our specification range that we’ve made,” he said. “We have a good group of guys… they know what they’re doing… If we have an issue one time, generally speaking, the next time we’re doing it, that issue is gone.”
Olson said it’s important for products to be in-spec to ensure they are both safe to consume and match the quality and consistency of what’s being produced in Galloway’s other evaporator.
“We’re trying to replicate the product to be identical to the product ran on either (system),” he said. “That was part of the engineering process… We want to make sure that we’re creating the same product.”
Future growth
Though the new milk evaporator was dedicated to its customers, Tim said the facility expansion represents Galloway’s commitment to more than just the company’s clientele.
“As the third generation is at, or near retirement, this expansion is a commitment to our industry, company and community who will be here for a long time,” he said. “Hopefully, we are back here at the age of 97 to see amazing growth just like Grandpa did.”
Tim also said the company’s growth won’t stop here, with plans to “spend another $100 million in the next few years” on growth.
“This is the right thing to do for the people who manage this business for us, those who make the products that sustain us, the community that supports us and our vendor partners that make all this happen,” he said.
To learn more about Galloway Company’s history and product offerings, visit its website, gallowaycompany.com.