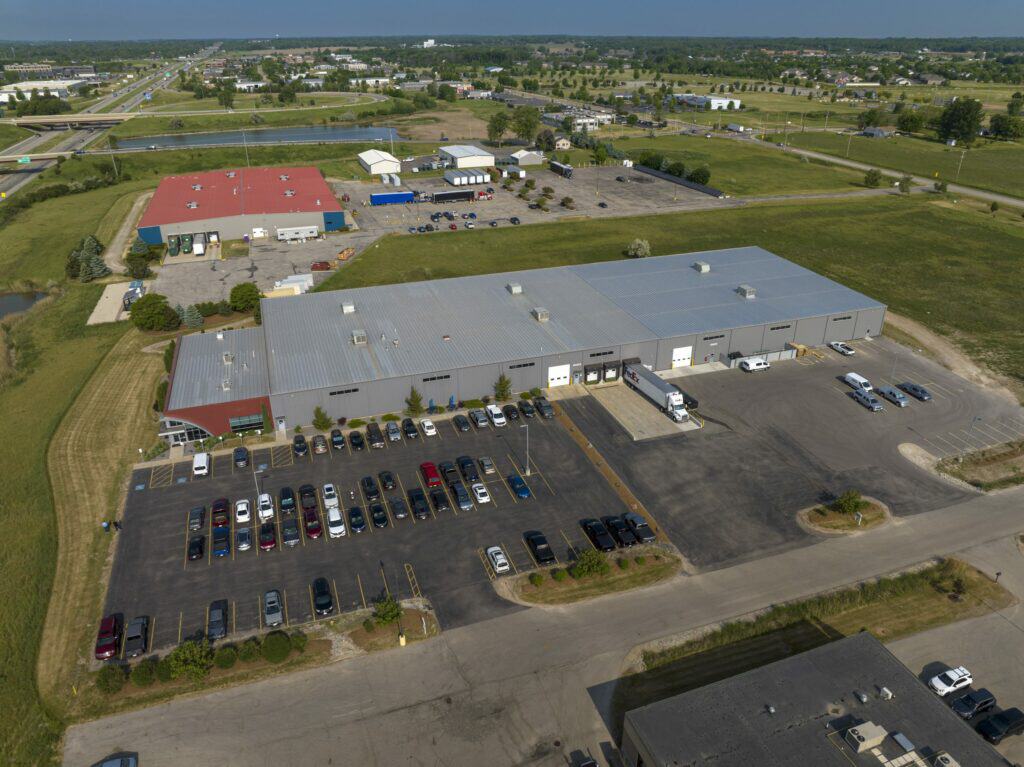
September 9, 2024
APPLETON – Being located across the highway from the landfill, Jordy Krall – materials and sustainability specialist at Eagle Performance Plastics – said, highlights the importance of reducing company waste.
“We see it growing,” he said. “Being able to minimize our contribution echoes throughout the building.”
It’s that focus on decreasing Eagle’s landfill footprint, Krall said, that led to a partnership with Convergen Energy in Green Bay.
Finding a way
For years, Krall said Eagle has searched for a solution to manage the plastic shavings generated from machining customer parts.
“We work with plastic materials, and when you’re not able to say that you’re doing anything with the (excess) – it’s something that has bothered us,” he said.
Due to the mixed materials of these shavings, traditional recyclers won’t accept them, and as a manufacturer working with various plastic materials, Krall said sorting the shavings by type is impractical.
Larger pieces of excess – “if you can picture it, you have a square piece of plastic, you cut a circle out of it and you have little triangle chunks left over” – Krall said, were picked up by a recycler, “because we knew what the majority of what it was made of.”
The issues, he said, involved the shavings disbursed during the cutting process.
“As we machine them, one material type quickly spreads into another material type, and due to the cross-contamination of materials, the recycler won’t accept the shavings,” he said. “So up until our partnership with Convergen, we had to send those shavings to the landfill because no recycler would accept them.”
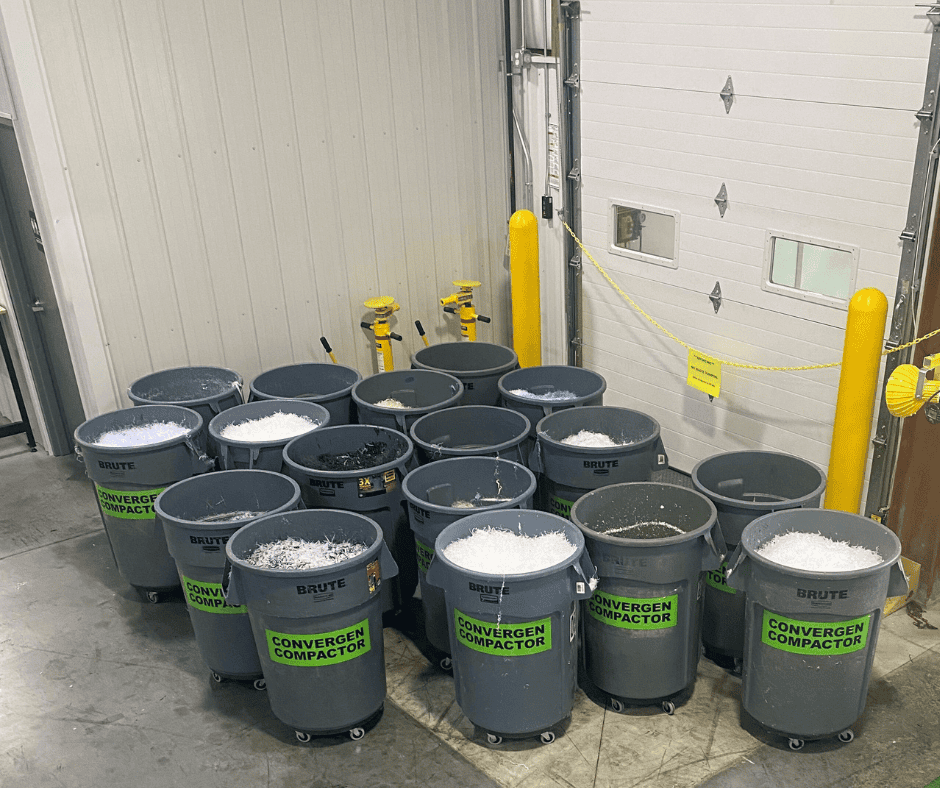
Last year, Krall said Eagle toured Convergen – a Green Bay-based company that converts mixed waste into fuel pellets, using uncontaminated paper materials and plastics that would otherwise end up in landfills – through an event hosted by the Green Bay Innovation Group (GBIG).
“Whenever GBIG hosts an event that pertains to sustainability, I try to attend them,” he said. “On the Convergen facility tour, we got to see the whole entire process – from the materials they receive all the way through the pellet generation.”
After touring the Convergen facility and understanding the process, Krall said Eagle quickly recognized that they offered the environmentally responsible solution the company had been searching for to repurpose its plastic waste and keep it out of the landfill.
“We then invited Convergen to come to Eagle and evaluate if our material would be acceptable based on what their needs are,” he said. “We then did a trial run with Convergen, and it was successful.”
Following extensive planning and discussions – both internally and externally with Convergen, Krall said Eagle implemented a new system on-site.
“We installed a trash compactor to compact the plastic shavings we generate for shipment to Convergen,” he said. “Additionally, we added more trash cans, which we color-coded to differentiate between waste types. One color indicates waste suitable for Convergen Energy, while another is for landfill-bound waste.”
Eagle’s partnership with Convergen, Krall said, marks the beginning of a new waste stream initiative that will divert the bulk of the company’s waste from landfills by repurposing it into fuel pellets and eventually electricity.
Though the initiative has just started, Krall said Eagle estimates it will be able to reduce its landfill waste by approximately 80% to start – keeping nearly 200 tons of waste out of the landfill annually.
“As we refine our processes, we hope to increase this reduction even further,” he said.
Finding a solution to this problem, Krall said, has been something Eagle has been working to correct for years.
“I started with people over five years ago now, and that’s always been something that I’ve looked into,” he said. “Not everybody may consider themselves an environmentalist, but everyone noticed the waste, and it really does bother everybody here. The bulk of our waste is plastic shavings, and it’s what we do every day. So, finding that correct avenue for it is something everyone at Eagle is pretty excited about.”
Even more fixes
The process in which the plastic shavings are collected and transported, Krall said, even provides for a more efficient process.
“The cool thing with the compactor is it’s like a contained system,” he said. “Previously, we had a standard, eight-year dumpster, so when the waste management company would come pick up the waste, the truck would flip it overhead and empty the contents of the dumpster into the truck.”
That process, Krall said, would oftentimes cause the lightweight plastic shavings to scatter throughout the parking lot.
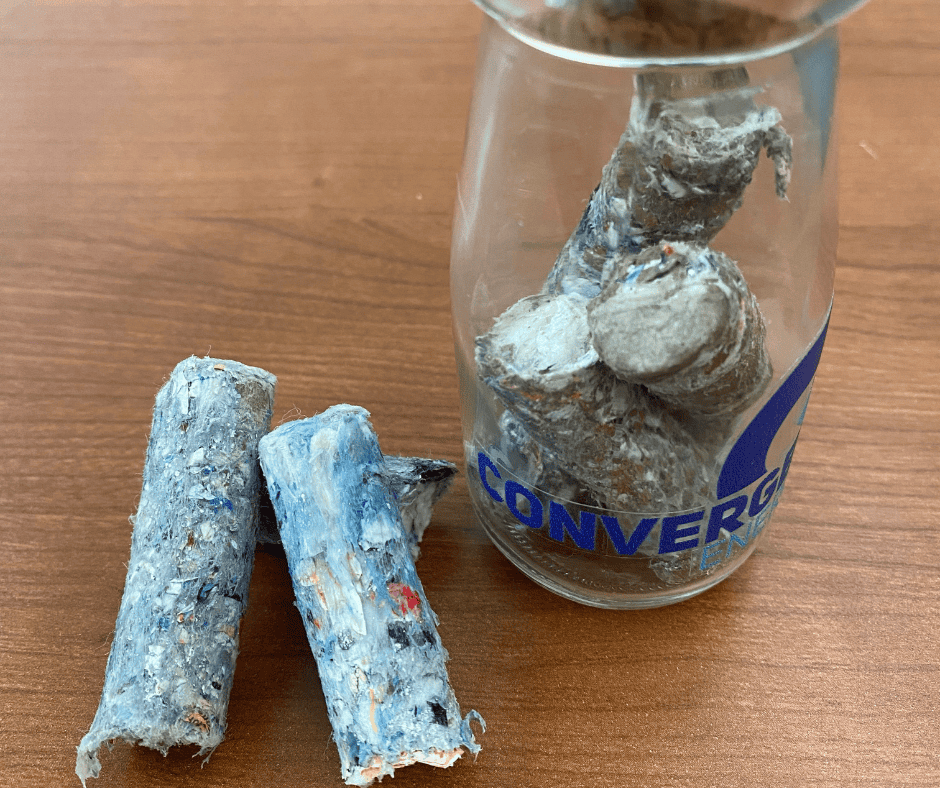
“We’d have to sweep that up pretty frequently and put it right back into the dumpster for them to pick up the next time,” he said.
Now, because the compactor is a contained system, Krall said “everything we put in the compact is sealed so nothing is blowing around the parking lot anymore.”
“I can only imagine how much it blew around in the waste management trucks on the way to the landfill, previously,” he said. “Now it’s all contained within that compactor for the entire trip to Convergen.”
Krall said he believes “if you can do something better, then you should do it better” – which is the approach Eagle has taken with this sustainability initiative.
“We’re not having any cost savings with this, I think it’s actually costing us more money to do this,” he said. “But it’s the right thing to do. It seems like a small effort – sorting plastic shavings – but those changes can make a big difference in the long run.”
More about Eagle Performance Plastics
Eagle supplies custom plastic parts for a variety of industries around the world – including food and beverage processing, material handling, packaging equipment and robotics just to name a few.
“All the materials we make are for reusable plastic components – these parts are going on large machines that are intended for repeat use,” he said.
For more on Eagle Performance Plastics and its sustainability efforts, visit eagle-plastics.com.