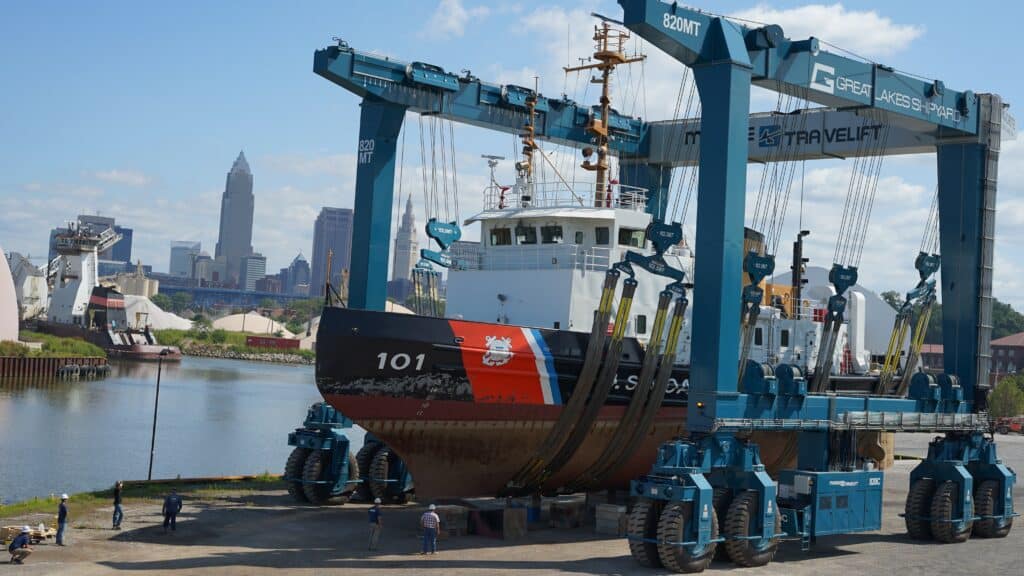
November 4, 2024
STURGEON BAY – As giant ships continue to dock at one of the many ports along Wisconsin’s northeastern coast, one may wonder how those vessels are initially launched into Lake Michigan.
The answer – or rather, the solution – can be found on Wisconsin’s peninsula.
People “don’t really think about how they get all these boats out of the water,” Marine Travelift CEO Erich Pfiefer said. “Well, that’s what we do. It’s what we know.”
Marine Travelift has been a staple in the mobile boat hoist manufacturing industry since 1954, and Pfiefer said its recent $5.2 million contract to build a 620-ton hoist for the U.S. Coast Guard’s shipyard in Baltimore, Maryland, is just another example of its dominance.
As a global supplier of mobile boat hoists with no major direct competitors in the U.S., Pfiefer describes the company as an “800-pound gorilla in the industry.”
“This isn’t an industry that has huge volume,” he said. “It is an important industry, (but) it’s not like we’re building thousands of these a year.”
Most of the company’s competitors, Pfiefer said, are overseas as they ship the hoists “all around the world (to) all six continents – anywhere where there’s regular vessel activity.”
He said these hoists – which vary in size – will lift personal watercraft, government vessels, tugboats, barges and supply vessels in and out of the water – supporting port and offshore oil activities, as well as offshore vessel transportation, fishing industries and defense industries.
Though the hoist Marine Travelift will be constructing for the Coast Guard is “the biggest mobile boat hoist that the U.S. Federal Government (will) own or has (owned),” Pfiefer said it is nowhere near the largest hoist the company builds.
“The biggest one that (we’ve) built to date is a 1,000-ton mobile boat hoist,” he said. “That’ll pick up like a 300-foot barge – that’s the biggest vessel we’ve seen picked (up) with that one.”
The planned Coast Guard hoist, Pfiefer said, will be capable of lifting 150-foot-plus vessels in and out of the water.
Why mobile?
Ports, docks and piers aren’t mobile, so why are the boat hoists?
“Prior to this type of equipment being mobile, you could (only) lift one boat at a time, whether it was on an old-fashioned railway or a dry dock,” Pfiefer said. “But (being) mobile allows them to lift the vessel out and set it in the yard and have multiple vessels in the yard at one time.”
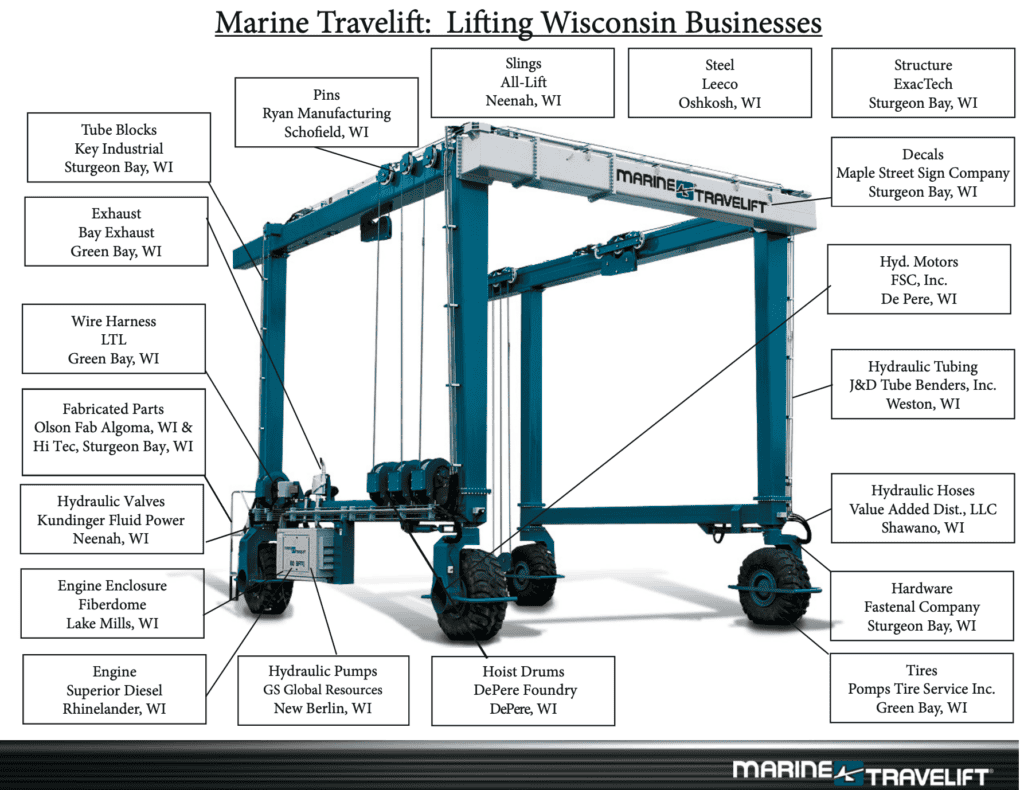
He said the hoists being mobile is “absolutely crucial” for their use case – especially with the Coast Guard.
To conduct regular maintenance, Pfiefer said the boats need to be out of the water so engineers can access all the parts they need to.
“(From) the Coast Guard’s perspective,” he said, “they’re able to work on multiple vessels at once… That’s really critical for them.”
Without any major domestic competitors, Pfiefer said Marine Travelift has become the go-to company to fulfill contracts like theirs with the Coast Guard.
Though, regardless of its competition, he said the company strives to be the best.
“Our whole premise is we build machines like this all the time,” he said. “We know it well. We can build it cost-effectively, we can build it efficiently and we can build it quickly.”
Pfiefer said “it’s been about a decade” since the Coast Guard contacted Marine Travelift to discuss what it wanted to do to the yard and the type of vessels it wanted to handle – “(an) iterative process of understanding our capabilities, what we can do and what the machines can do.”
“I think it started because some of the Coast Guard’s vessels were getting lifted with other machines (of ours) that were of this capacity,” he said, “and they realized (they needed) to take that control in-house so they can control their own schedules and workflows.”
American-made, Wisconsin-supported
Pfiefer said a unique element of Marine Travelift’s contract with the Coast Guard is that it falls within the parameters of the Buy America Act – legislation passed in 2021 that, according to the U.S. Department of Commerce, requires federal agencies to prioritize purchasing American-made products.
“I think the Buy American Act is important to ensure that the tax dollars are being spent on American equipment… as well as ensuring American suppliers for this equipment are paid,” he said.
However, the reason the contract falls within the legislation’s parameters, Pfiefer said, is because Marine Travelift was already prioritizing – as it always has – sourcing American-manufactured components and materials.
“We definitely strive to not only make sure all the materials are American made, but also really focus on utilizing Wisconsin businesses,” he said.
Pfiefer said it sources parts and materials it needs to build the boat hoists from companies across the country, “but the majority of our components and outsource parts, if you will, are from Wisconsin manufacturers.”
“We design everything… (and) we assemble a lot of the components together,” he said. “But we obviously don’t manufacture (things) like a hydraulic motor or a gearbox… We buy all those components from Wisconsin-based companies.”
Pfiefer said Marine Travelift does all of its steelwork in-house, but the steel itself is also sourced from American manufacturers – mostly from Gary, Indiana.
“So not only is it helping (support) jobs in Wisconsin and Northeast Wisconsin, but definitely the Great Lakes region and the Midwest region,” Pfiefer said.
To delivery – and beyond
Due to the massive scale of the mobile boat hoists, Pfiefer said Marine Travelift will “do everything in sub-assembled components,” and ship those components to then be fully assembled where they’ll be operational.
“We’ve got about 200 people that work here (and) about 200,000 square feet of facilities, (which allows the company to manage the sub-assembly in-house),” he said.
One aspect of Marine Travelift that Pfiefer said differentiates the company from the (lack of) competition is its customer service following delivery.
He said it will send a team of two or three employees to assemble the hoist, “and within about three weeks, that thing will be fully assembled – ready to pick (up) vessels.”
“That’s what really sets us apart,” he said. “And that’s what federal agencies see, is the support after delivery.”
Pfiefer said Marine Travelift has been working with the federal government for “more than 40 years at this point.”
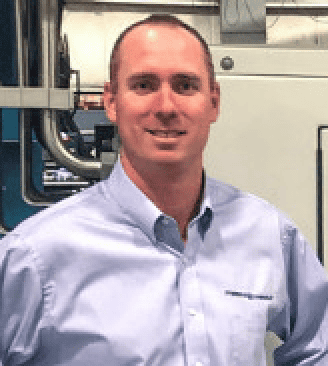
From a security standpoint, he said it’s really important for the government to have a partner that can support them, and has had a history with working with.
“This equipment will last the government 20-30 years,” he said. “So having an American company that can be there to support them, provide parts (and) provide service… is really important because of the critical nature of the mission of these vessels.”
Though government contracts make up no more than 10% of Marine Travelift’s business in a given year, Pfiefer said working with federal agencies is “important to us… We’re proud to do it.”
Training on the job
Like many other employers in the Badger State, Pfiefer said Marine Travelift is also struggling to find experienced employees right now – even more so with its need for “skilled labor” to build the hoists.
“You can definitely find people who are willing to work and learn – (which) takes time to onboard them and get them up to speed,” he said, “but to find people who are already qualified and experienced – it’s a challenge.”
However, with businesses like Marine Travelift in the state, Pfiefer said he “(thinks) Wisconsin is actually quite a bit ahead of the curve compared to a lot of states on how they place an emphasis on skilled labor (and) manufacturing.”
He said Marine Travelift is also trying to do its part in promoting skill-based manufacturing jobs through internship and apprenticeship programs where employees are paid to learn new skills.
“That’s how we’ve been able to get to (this) market position,” he said, “through that dedication, hard work and continuing to improve – and ultimately supporting our customers to the best of our ability.”
Pfiefer said the 620-ton hoist will take about a year to build and is estimated to support 50-60 jobs.
That estimate, he said, is a conservative one, as it encompasses all the jobs that will be created within both their own company and the ones Marine Travelift relies on for components and parts.
Though he couldn’t speak to the permanency of those jobs at other companies, he said the new positions at Marine Travelift are expected to be permanent because they have “a great workflow of orders,” that will continue to add jobs to fulfill the number of hours needed to assemble just one of the 100 hoists they build every year.
Visit marinetravelift.com for more information.