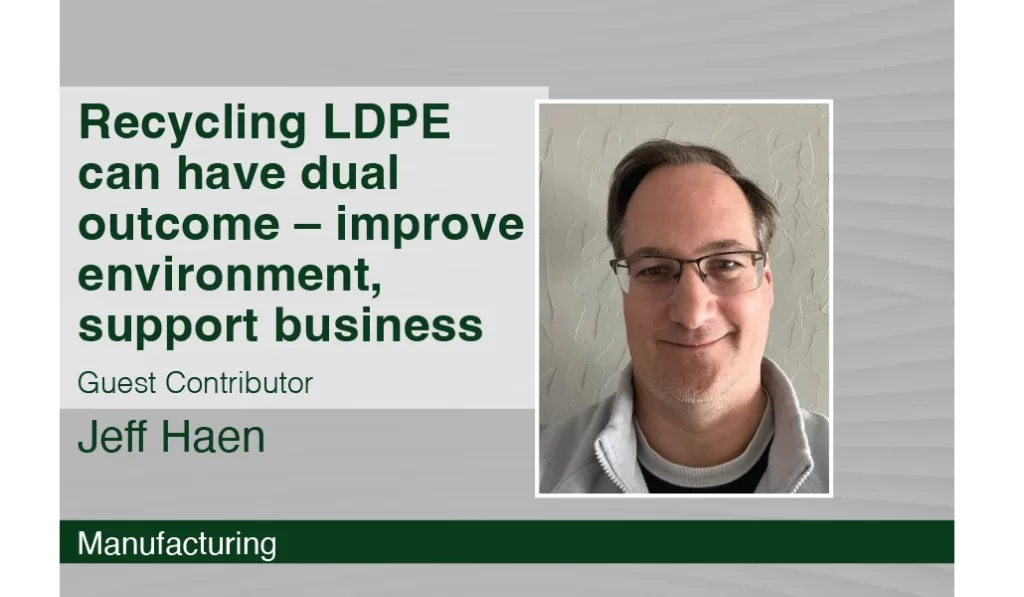
April 5, 2023
As more businesses become environmentally conscious, finding ways to minimize waste and increase recycling often find their way to the top of priority lists in an effort to implement sustainability practices.
One item that makes it into the minimizing waste conversation is LDPE plastics – which are commonly used to make plastic bags, shrink wrap, food packing and wire coverings.
This is especially true for businesses, such as manufacturers, distribution centers, retailers, medical facilities and other types of businesses that frequently receive bulk shipments, as these shipments are typically wrapped in these types of materials to secure items during transport.
Unfortunately, less than 10% of LDPE is recycled in the U.S., despite the fact that it is recyclable and can be reused to create a variety of new products, including manufactured lumber, plastic bins, paneling and furniture.
Potential hesitations
A common reason why businesses decide not to recycle LDPE is because the collection and recycling of it take time, requires space on the floor and creates opportunities for injuries to occur.
That’s because, typically, the LDPE plastic is collected with gaylord boxes – which are large, bulky and placed on pallets so they can be moved using a forklift.
They are then placed at key locations around a facility for the collection of LDPE plastics.
Once full, they are transported to a baler via a forklift and then unloaded manually.
This process can create a variety of opportunities for injury.
According to the Occupational Safety and Health Administration (OSHA), up to 62,000 injuries occur every year involving forklifts – many of which occur from turning too quickly, causing a rollover or from running into a co-worker while maneuvering the lift.
In addition to the potential for forklift injuries, a study from the Pain Relief Institute shows repetitive stress injuries account for up to 75% of all workplace injuries in the United States. Manually unloading a gaylord box – which involves bending over to reach into the box, collect the LDPE and transport it to a baler – creates a continuously repetitive motion.
In reality, gaylord boxes are not an efficient or safe way to recycle LDPE.
It’s time-consuming, creates a risk of injury and takes up valuable space.
Alternate methods
The solution isn’t to forgo recycling LDPE plastics.
Instead, it’s about changing how you do it.
Start by evaluating where your LDPE plastic is collected.
If you are using gaylord boxes, consider finding alternatives that take up less space and don’t require the use of a forklift.
It’s also good to talk with your team to see what ideas they have to help reduce the time and energy needed to dispose of LDPE plastic – as the people who perform the task, they will likely have some great ideas.
Be sure to explore what other companies are doing and research online for alternative options available that streamline the process while making it safer for your employees.
Ultimately, recycling this plastic is essential not only for helping to improve the environment but also as a sound business decision.
Jeff Haen is co-owner and vice president of PolyWrap Recycling, Inc.