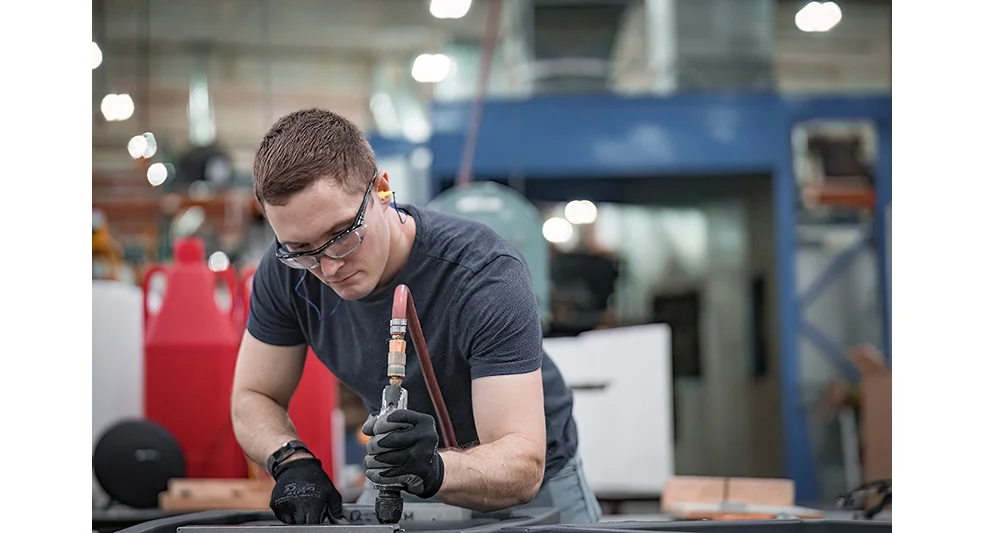
April 5, 2023
MANITOWOC – Those not directly connected to the realm of plastics manufacturing may have never heard of Manitowoc-headquartered Redline Plastics.
The company’s employees, however, have a lot to say about it – having voted the rotational molding and thermoforming plastics manufacturer “Best Place to Work” for the third straight year.
Plastics News’ “Best Places to Work” is a research-driven program from Best Companies Group that examines a company’s practices, programs and benefits, as well as surveys employees for their perspective.
“It is great to be recognized with this award,” Redline CEO Chuck Webster said. “But it’s even better to know our team feels we have a positive work environment.”
Despite being a relative newcomer to the industry – expanding into plastics fabrication in 2016 – Redline has been named to Plastics News’ list the last three years.
Nick Murray, president of Redline Plastics, said being the best starts with happy employees.
“(We offer) things such as flexible schedules, awesome shift leadership and the opportunity to earn bonuses for meeting goals,” he said. “We have a clean, bright and comfortable facility, which not every manufacturer can offer to their team.”
Nikki Paider, Redline human resources manager said it’s the people you work with every day who can make or break your work experience.
“One of our cultural behaviors is to ‘Recognize Awesome’ when we see it,” she said. “We know our employees are the ones we count on to ‘Be the Face of Redline,’ and get our customers the products they need, and on time. We know we are lucky to have an exceptional group of staff who make things happen.”
To reinforce the idea of “Recognize Awesome,” Paider said Redline chooses one “Cultural Behavior” each month to highlight.
Redline Plastics is a rotational molding and thermoforming plastics manufacturer located at 1434 South 59th St. in Manitowoc. Photo Courtesy of Redline Plastics
“Supervisors help create videos describing what the chosen mantra means and how it benefits our company, employees and customers,” she said. “These videos are shared through our internal communications and via social media. Over the course of the month, employees are encouraged to nominate another Redline ‘Ninja’ who demonstrates the Cultural Behavior of the Month.”
At the end of the month, Paider said a winner is selected to enjoy a fun meal with the person who nominated them and company leadership.
A little background
The Redline name wasn’t established until 2018, but the company itself has a long legacy in the Manitowoc area.
The company got its start in 1922 as Dow Canvas designing and manufacturing products for the tent and awning industry.
In 1975, the Webster family purchased the company and added marine and powersports covers manufacturing.
The company was renamed Dowco in 1996.
Growth continued as the years went on – expanding into plastics fabrication in 2016, with the purchase of Premier Plastics.
In 2018, the Webster family sold the Dowco Marine division of the company, while keeping the plastics and powersports businesses, renaming them Redline Plastics.
Redline specializes in rotational molding, thermoformed plastics and industrial cut and sew, which Marketing Manager Mary Kahler said makes Redline a “one-stop shop.”
“We have customers in all three areas who are exclusive to each other, but we also have been able to capitalize on a growing need for customers to streamline their supply chains by providing support through two or more of our work centers,” she said.
Today, Kahler said Redline Plastics is a leading manufacturer of rotational molded, vacuum-formed and line-bent plastics products for a variety of industries, as well as leather and textile cut and sew products produced both domestically and internationally for the powersports industry.
Redline also specializes in fiberglass-reinforced plastics for the construction and marine markets.
Toolkit approach
Kahler said there are a handful of rotational molders in the Wisconsin and Midwest region who do a ton of volume, but typically focus only on rotational molding.
“Our differentiation at Redline Plastics is that we have a toolkit approach,” she said. “A mechanic may need one tool for a project today and a different one tomorrow – or they might need several to do the job right. At Redline, those additional capabilities have been key in providing value to our customers.”
Kahler said Redline is forward thinking not only in its approach to products and service offerings but also from an environmental standpoint – completing numerous Focus on Energy projects and system evaluation, which Kahler said has allowed them to ensure they are running the larger 225,000-cubic-foot building and equipment as efficiently and as energy-consciously as possible.
Doing its part
From temperature regulation and LED light implementation to specific machine upgrades and electrical heat collection, Kahler said Redline has modernized the new facility as much as possible to help with rising energy costs – thus lowering the company’s carbon footprint while running a state-of-the-art facility and manufacturing process.
Kahler said Redline also designed and outfitted the larger facility with fuel management in mind – which has allowed the company to repurpose the heat generated through the production process to heat the building during the winters.
“All of this has allowed us to save on additional energy costs and use,” she said. “Overall efficiency of our ovens and a reduction in the use of our natural gas fuel is of particular emphasis within our processes.”
In addition, Kahler said Redline has several other initiatives to reduce environmental waste, including repurposing internal scrap plastic and recently investing in shredder and grinder equipment that will help reutilize material more efficiently.
Chuck Webster
She said the facility’s resin silo has minimized the company’s over-the-road resin shipments to the plant.
Kahler said Redline also actively partners with several eco-friendly customers to drive increased use of repurposed resin, as well as experimentation with new alternatives, such as hemp-filled resin.
Second chances
Kahler said Redline also takes to heart giving a second chance to those who need it.
In the past year, she said the company has become a recovery-friendly employer, providing support and employment for members of the community who are struggling with addiction.
Kahler said Redline has partnered with Lighthouse Recovery Center, a local recovery organization, to continue to learn how it can best support this population.
“We have hired more than 10 employees who are active in the recovery program,” she said. “We are humbled to know our ability to provide a safe working environment has supported these employees in their journey to recovery.”
Quality Holdings acquisition
Last month, Redline announced the acquisition of Quality Holdings, LLC, a rotational and compression molding company in Hartwell, Georgia, which Kahler said fits into Redline’s strategy to build capacity in rotational molding as well as diversify into additional plastics specializations.
Kahler said the acquisition of Quality Holdings affords Redline the opportunity to target new geographic regions while expanding its services and locations for its domestic customers.
She also said that adding compression molding capabilities will bring new opportunities in new markets.
“We look forward to sharing knowledge, resources and expertise with our Georgia operations team and staff to improve processes in both locations,” she said.
In the near term, Kahler said the plan is to devote capital toward people and process improvements that will drive incremental improvement in the overall business.
Whether that is additional equipment or leasehold improvements, Kahler said Redline is taking a look at all options to drive incremental growth and profitability while focusing on how it can make new team members’ lives easier.
Kahler said Redline is in the long-term game mindset.
“Over the next several months, the Redline Manitowoc team will work with the Redline Georgia team to prioritize those items needing attention to make our business and the people within it stronger,” she said. “Our integration plan will take a ‘people approach’ to form relationships of trust and teamwork toward reaching our company’s strategic objectives over the next several years.”
Nick Murray
Kahler said there were many reasons Redline chose to acquire Quality Holdings.
“We were excited at the prospect of additional rotational molding capacity and a trained workforce, as well as the addition of the compression molding capability,” she said. “In the long term, we look forward to the strategic advantages that having a location in the southeast will provide.”
Murray said the Quality Holdings team also has similar values as Redline Manitowoc that will benefit both locations.
“We are focused on integrating our new Redline Plastics facility in Georgia and welcoming our new team members to our family,” he said. “This acquisition will allow Redline Plastics to continue to grow in capacity and capability by leveraging the equipment, trained workforce and customer relationships that are already in place.”
Kahler said Redline is looking forward to building on the “solid foundation the team at Quality Holdings has built in terms of employee focus and culture.”