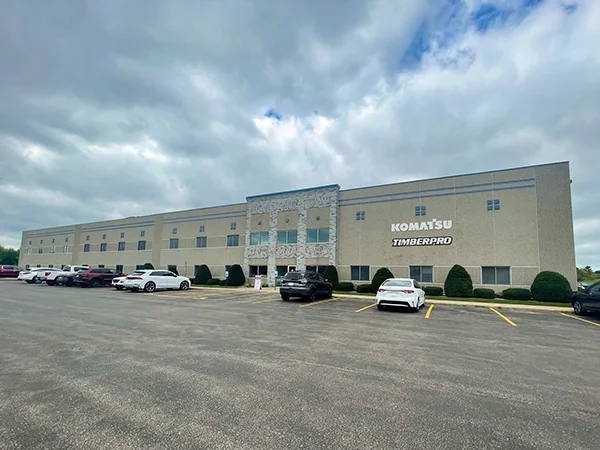
September 19, 2023
SHAWANO – The path that led to the creation of TimberPro Inc. (1407 Industrial Drive) was one of innovation, acquisition, growth, more innovation and even more acquisition – the culmination of founder Pat Crawford’s perseverance and hard work.
“Pat was a logger who decided he was going to make logging equipment easier and make it easier for others to log,” TimberPro Plant Manager Mike Peterson said.
Crawford’s decision to be an innovator rather than just a logger following the pack, Peterson said, led to the creation of Timbco – the forebearer of TimberPro Inc.
“You can’t talk about TimberPro without talking about Timbco, which developed what the feller buncher looks like today with what’s called an ‘engine-up’ design – which means the engine is on the upper turntable and stays level with the cab at all times,” he said.
Peterson said at the time Crawford launched Timbco, he was primarily interested in building machines for his own use – not necessarily looking to be in the manufacturing business.
But when interest from other loggers continued to pour in, Peterson said Crawford – at the age of 55 and after having been a logger for most of his life – began a whole new career in manufacturing.
Though in the beginning Crawford struggled, Peterson said slowly but surely the company grew – starting with a two-way leveling machine and later introducing a four-way leveling machine.
Peterson said the company’s engine-up design was crucial to the continual growth of the Timbco brand – noting that many of the ideas within the forestry industry can be traced back to Pat’s guidance.
The engine-up design, Peterson said, sold well in the Northwest area of the United States and British Columbia due to the steep terrain of logging.
As the company continued to grow and Crawford’s design continued to be sought after, Peterson said Crawford realized they couldn’t do what they wanted without better distribution.
“At some point, it came down to distribution,” he said. “Distribution was done by Caterpillar when they focused more on the forestry industry and John Deere.”
This, Peterson said, eventually led to Partek’s (now Valmet) offer to buy Timbco – which happened in 2000.
With the sale, however, Crawford maintained the option to buy back the wheeled division because Partek already had a wheeled division.
Peterson said Partek was mainly interested in the tracked division and ownership of the name.
In July of 2002, at the young age of 77, Peterson said Crawford bought the wheeled division back and started TimberPro Inc.
By the end of 2002, Peterson said, the first heavy-duty wheeled feller-buncher was designed and sold.
The current office building was built in 2004 (which underwent renovations this year), and in 2007, the non-compete for the tracked division was up, and Crawford started making tracked machines in addition to wheeled machines.
Peterson said until his death in 2018, at age 92, Crawford and his wife Ruth continued to be an integral part of TimberPro.
The company was acquired by Komatsu America Corp. – a global heavy equipment manufacturer headquartered in Chicago – in 2019 but retains the TimberPro name.
Today, TimberPro manufactures purpose-built forest machines and attachments – including tracked feller bunchers and harvesters, forwarders, wheeled harvesters and felling heads.
Transitioning to forestry
Peterson – a Merrill native, said he was already working for Komatsu in the Wausau area when he was asked to transfer to Shawano after the company acquired TimberPro.
Though he was working in Komatsu’s mining division at the time before moving to forestry, Peterson said there were many similarities between the two.
“I was in the mining division, and I’m a manufacturing guy – that’s where my background is,” he said. “However, there’s so much that’s similar between other commodity organizations.”
The TimberPro team recently celebrated its 1,000th built tracked buncher. Submitted Photo
Peterson said he finds the forestry division interesting because there is silviculture, which he said is “like an offshoot of agriculture.”
“In reality, forestry is not that different from farming,” he said. “It’s just a much longer lifecycle of what you’re harvesting.”
Distributor partnerships
Peterson said TimberPro doesn’t deal with the end user, rather it makes the machines for distributors, such as CrossTrac, Roland Machinery, Modern Machinery and Anderson Equipment.
“The distributors are the face of the company,” he said. “We rely on them to sell the machines – and then support the machine. So, they’re our face with the forester or the logger that’s in the woods when something needs to happen with the machine.”
Peterson said wherever there is a tree and mechanized forestry, TimberPro will do its best to sell a machine there.
“We have a pretty large dealer in Europe that sells throughout Spain, Belgium and France,” he said. “They do a lot of biomass creation. They essentially grind up a lot of the smaller type of wood that isn’t going to be used for lumber or for veneer or something like that.”
Peterson said TimberPro has a lot of machines down under in Australia and New Zealand as well.
One market the company is trying to break into, Peterson said, is South America.
“We’ve sold some machines there in the past, however, there’s not a strong dealer network down there yet,” he said. “We’ve recently placed our first machine in Brazil in quite a long time. We’ve sold quite a few machines into Chile as well.”
Almost 2,000 machines
With a worldwide network of sales, Peterson said TimberPro recently built the 1,000th track machine.
Including those, plus more than 800 wheeled machines, Peterson said the company is nearing almost 2,000 machines built in 20 years – which he said is quite an accomplishment.
“It’s pretty exciting,” he said. “It’s a huge milestone, and we’re looking forward to building more.”
Peterson said it takes about six weeks, from start to finish, to manufacture a TimberPro machine.
“Once it’s in assembly, it’s two to three weeks, but we have several machines being built at the same time,” he said.
Supply chain hiccups, Peterson said, have been a major hurdle for TimberPro, even before he came aboard.
“The hydraulics industry is probably the toughest one to get material out of, just because they’re so swamped with work right now,” he said. “Materials in general are hard to come by. But, then even steel here and there has been difficult to come by. Electronics have been an issue for a while as well.”
Facility, company expansion
The TimberPro facility has undergone a handful of expansions over the years.
In 2008, a few thousand square feet were added, followed by another 30,000 square feet in 2012.
However, this past summer, the company finished its largest expansion yet – adding another 49,000 square feet, bringing the facility to a total of 147,000 square feet.
The expansion, Peterson said, will allow TimberPro to double its production capacity, thus enabling it to meet growing market demand for its equipment and attachments.
Doug Morris, vice president of the forest machine business division at Komatsu, said the TimberPro expansion represents a significant step forward.
To celebrate the project’s completion, Morris said TimberPro hosted a public open house late last month for employees, their families and members of the Shawano community.
TimberPro Plant Manager Mike Peterson said company founder Pat Crawford developed the engine-up design, which has the engine on the upper turntable and stays level with the cab at all times. Submitted Photo
“We were glad to showcase our enhanced capabilities to the community,” he said.
Morris said the new expansion was dedicated to the Crawford family for their contributions to the industry and community.
With the expansion and increase in demand, Peterson said that has also prompted a need for more workers – which like many other companies has been a struggle to find.
“If I could hire 10 employees tomorrow, I would,” he said. “It’s right behind supply chain issues.”
As a skilled-labor employer, Peterson said the challenge TimberPro runs into is it’s not necessarily easy to hire someone and learn the skills needed easily and quickly.
Managed forestry
Peterson said as a company in the industry, it’s important for TimberPro to educate others about the importance of forestry.
“We have to manage the forests like we manage any other crop we harvest,” he said. “We want to manage the forest from the environmental side as well as from the consumer side.”
Peterson said there is a huge demand for forest products, such as pulpwood that’s used in making paper, tissue and toilet paper.
Lumber, Peterson said, is also in high demand.
“We have a huge demand for housing in the United States and throughout the world for that matter – so lumber is huge as a driver,” he said. “With that goes the veneer or the high-quality woods for making high-quality furniture or anything that’s needed.”
Economically, Peterson said, forest management makes for one less supply chain issue for the final end user of whatever forest product is being used.
According to the Wisconsin Department of Natural Resources, the forest products industry provides more than 61,000 full- and part-time jobs in Wisconsin and has a total industry output of $24.4 billion.
Morris said to help support regional jobs and the regional supply chain, TimberPro sources materials from many companies in northern Wisconsin.
“Forestry is important to the Wisconsin economy, and the recent expansion will enable us to provide more good family-supporting jobs, while also allowing us to enhance our research and development capabilities and significantly increase our production,” he said.