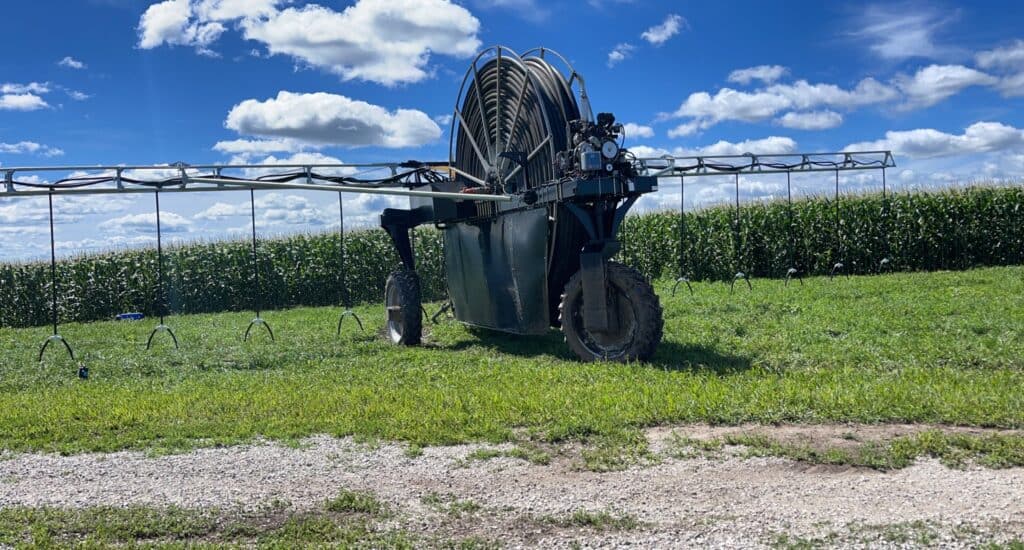
January 27, 2025
SHAWANO COUNTY – No one understands the need to embrace technology more than Jeff Strassburg and his son Jacob (“Jake”), as fifth- and sixth-generation farmers/owners, respectively, of Strassburg Creek Dairy, LLC.
Started in 1886, the dairy farm today boasts 4,100 acres of cropland in Shawano County and milks approximately 1,675 dairy cows daily.
Though they have 20 full-time employees in addition to family members – multi-generations working side by side, including Jeff’s wife, Jeni, and daughter, Alyssa – Jeff said there would be no way to effectively or efficiently run this farm without the benefit of technology.
Each generation, he said, has been encouraged to bring innovative ideas to the forefront of farm management at Strassburg Creek Dairy.
“As the younger generation comes in, you have to do like I did with Jake and like my parents (did with me) – and that’s gives them the ability to grow into the operation and do things to make it their own,” Jeff said. “You have to let the next generation bring new ideas in – it makes them excited about coming to work every day, doing what we do to feed the world, so to speak. It’s that next generation’s drive. For a successful business, you have to let the next generation take the lead and responsibility for that.”
Jake said his dad has been “very vocal and involved” in a lot of boards throughout the industry.
“(As a result), he has seen first-hand that we need to keep up with the times or others will pass us by,” he said. “He has always been open to new ideas, as well.”
An effective way to give crops water, nutrients
The most recent technological advancement the Strassburgs have added to the farm is the 360 RAIN system, manufactured and sold by Yield 360.
The 360 RAIN system – which Jake said takes farm efficiency to the next level – was installed on the farm in June 2024, after talking about it for two years.
He said it provides an economical way for them to apply leachate from their dairy operation to their crops exactly where it counts.
“We were updating our feed storage and the DNR pretty much told us we had to collect 100% of any rainwater that fell on our feed storage,” he said. “So, we had to put in a collection pit, a leachate pit to collect all the run-off. Then we had a bunch of water that we had to find a home for and the RAIN unit was the best application for that.”
Jake said 360 RAIN is an autonomous, diesel-powered/electric drive machine that connects to a water source through a 3-inch hose providing up to half an inch of water per pass.
He said it applies water, manure, nitrogen and whatever nutrients the farmer wants and because the application is right at the base of the plant, they gain increased efficiency, as well as increased profitability on every acre it covers.
When introducing the 360 RAIN at the 2023 National Farm Machinery Show, Aaron Phillips, regional manager at 360 Yield Center, said there are several benefits to the machine:
- Farmers can water their crop as it’s growing.
- Crops can be spoon-fed without the farmer having to rely on Mother Nature or an irrigation pivot.
- Crops receive a half-inch of water with every pass, throughout the growing season.
- The machine can be tied into wells, surface water and ponds, and can assist farmers in getting rid of dairy and hog manure.
“Getting rid of manure can be a big struggle for farmers and (they) usually only have a couple of weeks in the spring and a couple of weeks in the fall (to do so),” Phillips said. “(With 360 RAIN), the manure can be spoon-fed throughout the growing season instead of having to get rid of it at the end of the season.”
In total, Jake said they moved about 16 million gallons of leachate and 600,000 gallons of manure, using the system, and basically for nothing more than the cost of the electricity to run the pumps and some diesel to put in the machine – which Jeff said was cheaper than putting it in a truck and hauling it.
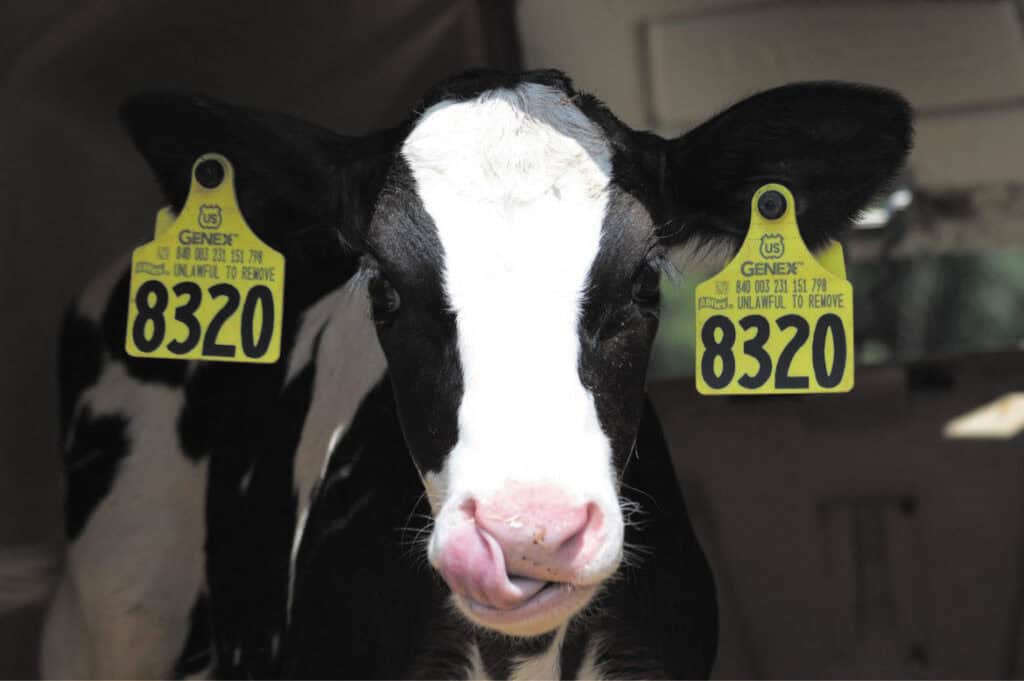
“So, that’s about 1,100 trucks that we took off the road, reducing our carbon footprint,” Jeff said.
What’s unique about the system, Jeff said, is it gives farmers the ability to have “that million-dollar rain.”
“We always hear farmers talk about ‘If I could only get rain at this certain time of the growing season, I’m going to have a great crop,’” he said. “Well, now we can do that. We can send this machine out and can water (crops) at those crucial times during the growing season.”
Initial skepticism quickly turned into belief
Jeff said he was a bit skeptical at first, but said once he saw the 360 RAIN in action, he quickly became a believer.
“It’s great because we’re able to apply nutrients not only into a green, growing crop, but we can apply them in smaller amounts as the plant is using them,” he said. “The unit can irrigate about a third of an inch of water across 160 acres in a week.”
Jeff said when you think about an inch of rain across an acre of land – that’s a little more than 27,000 gallons of water per acre.
“So, when you start talking about 5,000 gallons, you’re actually talking under a third of an inch, or maybe even under a quarter of an inch pretty easily,” he said. “When you think of a quarter-inch, that’s dried up in a matter of hours in the heat of summer.”
Jake said with the 360 RAIN system, it doesn’t really matter how much they put on at one time, because it’s all set up in the field already, and “we can go across that field as many times as we want.”
“It just matters how fast that machine drives,” he said. “We found it was actually better to put on 4,000 or 5,000 gallons an acre at a time and do it twice or three times than to do it all in one shot.”
The Strassburgs said they are using 360 RAIN on their cornfields, though they also grow soybeans, alfalfa and wheat, as well as some cover crops – all things on which the system could be used.
“This unit was born in Illinois, which is corn and soybean country, but they haven’t really done many studies with soybeans,” he said. “There was a farm west of Appleton that ran it in some alfalfa and had some really good results with that. But logistically, for us, the fields that we have it on are corn in rotation. We haven’t been able to use it on any other crops yet.”
Some 360 RAIN users, Jeff said, have realized a full return on their investment within that first year, though it can take two to three years to have it pay for itself, which is what he believes it will take for them to realize the payback.
In addition to the 360 RAIN system, Jake said they may put in an additional well at some point.
“As it sits right now, the only water source we have is that run-off water – we can also tap into our manure pit,” he said. “But, a lot of these RAIN unit systems have a well hooked up to them. We do not currently have a well designated for this unit.”
Jake said the unit needs about 200-240 gallons a minute, which is a lot less than what traditional pivot systems need.
“A lot of time we struggle to get 50 gallons a minute out of our wells, so we might have to explore our options on how to drill a well that would be capable of handling this machine,” he said. “We’re just not sure exactly where it would go or how we would do it. When you put that hole in the ground and invest in that infrastructure, you’re stuck with it, so we’re just trying to figure out where and what would fit best.”
Other innovations
Jake said the 360 RAIN unit is the most recent addition to Strassburg Creek Dairy’s long history of embracing technology and new innovations as they come up.
In 2022, he said they finished a multi-phase installation of a robotic milking barn, bringing the number of robotic milkers on-site to 12.
On average, Jake said, the robot can harvest nearly 5,000 pounds of milk per day from approximately 180 milkings.
Jeff said the farm has two different kinds of milking operations at the same facility – the robots and a more traditional milking parlor.
“We have two Grade A licenses – one for each of the two facilities,” he said.
Jeff said milk from the robots goes to one place and milk from the milking parlor goes to another.
“The robotic milking machine was put in to decrease labor costs,” he said. “It takes about a third of the labor in the robotic milking machine than in the milking parlor.”
In the last year or two, the Strassburgs also built a robotic calf barn, which Jake said allows calves to eat essentially whenever they want.
“Once you get them trained, they pretty much feed themselves,” he said. “It’s a free-flow barn, so the cows can come and go as they please. They can eat, milk, sleep or drink water anytime that they want.”
Other forms of innovation and technology recently implemented on the farm include:
- Auto-steer on tractors
- A row guidance system that guides the machine along the planted crop rows with high accuracy, reducing operator fatigue and maximizing yield potential.
- Yield mapping, which uses GPS data to collect information about crop yields and other field conditions. It helps farmers make decisions about when to plant, harvest and fertilize crops.
Jeff said this past year they installed what they call “machine sync” on the farm’s combine – which creates a wireless network connection between the harvester and the tractor pulling the cart, enabling the position and speed of the tractor to be synchronized precisely with the harvester.
He said it simplifies the process of unloading grain on the go for even the most experienced operators.
“It’s another step toward automation,” Jake said.
This year, Jeff said they are looking at putting in a sand separator to be able to reclaim it from the manure.
“All of our cows are bedded with sand, so that’s important,” he said. “Again, it will also take dump trucks off the road and help us get as close to carbon-neutral as we can be.”