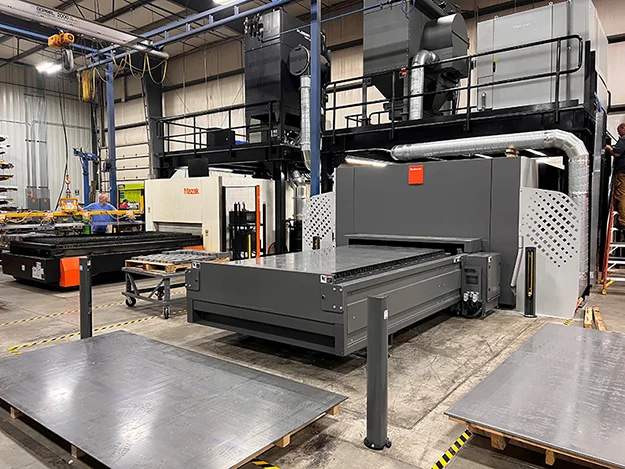
October 17, 2023
MANITOWOC – The arrival of the Seyi Stamping Press at Manitowoc Tool & Manufacturing (MTM) in February is the latest in what CEO Scott Mertens describes as purposeful efforts to stay ahead of the curve when it comes to innovation and state-of-the-art equipment.
This press, Mertens said, will top the company’s existing largest stamping press by more than 230 tons, allowing it to stamp more, faster.
“It’s been our experience that in the large stamping market, the more complex and bigger a part, the more tonnage needed to produce the part,” he said. “We can make large, complex pieces because we have the tonnage to do so, and we’ve reduced our competition by investing in large equipment.”
Over the past year, Mertens said the company has invested in a number of other pieces of equipment – including the Virtek Quality Laser Inspection System, Milltronics VM 3018IL, Bystronic 12kw Fiber Optic Laser and NEW Milltronics VM 4222IL CNC Machining Center.
Though MTM has a consistent budget line item for investing in new technology and equipment, it’s not something Mertens said he puts a limit on.
“It’s clear to management that I want to keep investing as much as I can, whatever that is,” he said. “The faster we can buy equipment, the better. We want to be as state of the art as we can be and to grow, and we have.”
MTM provides production metal stamping, tool and die design, the building of tools and dies, fabrication and assembly.
Mertens said the company’s origins date back to 1965 when it was known as Manitowoc Tool & Die and was located on 29th Street.
In 1980, the business invested in property on Clipper Drive in Manitowoc’s Industrial Park and with it diversified its offerings – continuing to create stamping dies but also adding machining and building tools and dies.
By 2006, Mertens said the business had grown significantly, prompting Mertens to split it into two companies with the machining breaking off and becoming Manitowoc Tool & Machining.
The brand new Milltronics VM 3018IL offers the company’s tool and die shop added capacity and efficiency to assist in delivering quality stamping tools and metal parts. Photo Courtesy of MTM
The tool and die design, metal stamping dies and production stamping became Manitowoc Tool & Manufacturing.
Embracing innovation
For more than a decade, Mertens said innovation at the company has included integrating the use of robotics as part of its operations.
“We’ve embraced robotics to help the operator, so they don’t have to lift as heavy of components, or to gain greater throughput,” he said. “It has never taken the place of somebody’s job – it’s an enhancement to production.”
Production has been on the upswing, which Mertens said sparked the purchase of a new, 42,000-square-foot building on Vits Drive in Manitowoc earlier this year.
The 20-acre property MTM acquired in the I-43 Technology and Enterprise Campus, Mertens said, is part of the company’s plan for the future – starting with the building that is currently serving as warehousing.
After the installation of the Seyi Stamping Press at the company’s 200,000-square-foot Expo Drive location, Mertens said future presses will be installed at the Vits Drive location.
“Those 20 acres prepare us for the future,” he said. “With parking, we can go up to 500,000 square feet in space there.”
What is metal stamping?
Simply put, Mertens said metal stamping is a manufacturing process used to convert flat metal sheets into specific shapes.
He said the complex process includes a number of metal-forming techniques ranging from blanking, punching, bending and piercing.
Mertens said MTM’s customer base runs the gamut of industries from appliance, automotive and lawn and garden equipment industries to office furniture, lighting, recreational vehicles and trailers.
“It’s important for us to be diverse,” he said. “We have never refused work from a customer, but it has pushed us to grow the rest of the business so we’re not top-heavy in one industry over another.”
In addition, as global markets evolve, Mertens said there is an ever-increasing need for quickly-produced, large quantities of complex parts that make their way into many everyday things.
“Odds are, if the chair you’re sitting on is of reasonable quality, the chair has metal stampings in it,” he said. “Odds are the fan apparatus in your bathroom has metal stampings in it, as does the toilet paper holder and the cabinet if it has hinges. We make a lot of light fixture components as well.”
If an item features an odd-shaped piece of metal, and there is a volume required, Mertens said it’s likely a stamping.
“It takes a stamping die to build a particular part, placed in a stamping machine, that goes up and down, to make part A,” he said. “Then there is a different tool to make part B and part C and so forth.”
Mertens said parts reach facilities both nationally and internationally, depending on where they are located.
A surge in growth
Though the company has experienced double-digit growth of about 10% in revenue year to year, Mertens said 2022 significantly surpassed that with 40% growth.
He said he credits heavy production numbers across the company’s customer base for the increase.
“When you get a new project, it takes a bit to get it running in the plant efficiently,” he said. “You start with 100 parts, then 1,000 parts and so forth. Last year, we had heavy production across the board.”
In addition, Mertens said customers often return to MTM for a number of reasons – including a dedicated and autonomous workforce that cares, the state-of-the-art equipment and its all-inclusive approach to business.
“We have an engaged workforce that is excited to be here,” he said. “We try to keep it new and exciting with new equipment and programs and giving them the autonomy to make decisions.”
Mertens said to him, inclusivity means being a one-stop shop – the ability to design, build a stamping die and run the production of stampings all in-house.
“So many times, competitors say they have toolmakers in-house, and they might, but they’re for sharpening a tool and not for building from scratch,” he said. “We don’t outsource anything, and I think our customers enjoy that the buck starts and ends with us.”
Responsiveness, accessibility and family ownership, Mertens said, figure into the equation as well.
He said every manufacturer, at some point, faces a hiccup – but it’s what you do in response to that that matters.
“Maybe we didn’t make (the error),” he said. “Maybe it was a drawing change, for example, but I am proud of our people for being super responsive. We hit issues head-on.”
That responsiveness, Mertens said, extends to leadership, including him.
“When a customer wants to come in and meet with the head person, they’re not talking to a board of directors – they’re talking to me,” he said.
Mertens said the company’s consistency in its mainstay values and behaviors is a milestone in and of itself.
CEO Scott Mertens said the Virtek Quality Laser Inspection System provides quick feedback, which allows Manitowoc Tool to meet tight timetables for its customers. Photo Courtesy of MTM
With 260 employees, maintaining an engaged, empowered workforce, he said, is not the result of happenstance.
“We have consistently invested in and engaged our employees and continually grown the business – it’s been that drumbeat that has helped us weather storms and be confident in our abilities and not take our eye off the ball,” he said. “We don’t decide to buy some company that makes a (different) product line or diversify our portfolio by buying land we hope gets developed. It’s about constantly investing in ourselves, our employees and our equipment that has helped smooth out peaks and valleys.”
A toast to employees, customers alike
As an extension of the company’s employee-focused mission, Mertens said MTM began assembling care packages for new employees – starting with an MTM-logoed lunch box.
Employees, he said, often joked that a six-pack would fit well in it as well – which eventually sparked an idea.
Max Ashenbrener, sales manager, said he met with PetSkull Brewing Owner Paul Hoffman about the idea of creating an MTM beer.
“He jumped on board right away, and it started with one beer type,” he said. “This past summer, we had our third iteration of an MTM beer and a non-alcoholic root beer we give to employees on holidays and also to customers. They’ve taken a liking to it and ask what the next iteration will be.”
Accelerating community involvement
MTM’s beer and root beer, Mertens said, was a great exercise in community involvement, and one example of the company’s efforts to give back to the community it has always called home.
Earlier this year, MTM provided funding to help support Valders High School’s Introduction to Engineering class – a block class the school offers every spring semester.
The culmination of the class, Mertens said, is the building of super mileage cars to be used in competition at Road America as part of a Challenge USA event.
The students’ goal, Ryan Zunker, technical education teacher at Valders High School, said is to build a car that measures up on the track.
“That was at the students’ discretion as it is a student-led, student-driven project,” he said. “I’m hands-off, which gives them a chance to be very hands-on.”
Zunker said students gain experience in designing, engineering and building the car while also tracking their budget.
In addition to its financial donation, Mertens said MTM offered access to the business’s manufacturing skills and equipment, if needed.
“A lot of students are intelligent, and this gives them a way to explore more in the shop area and gives them manufacturing experience,” Zunker said.
Ashenbrener said MTM has also supported the same program with Mishicot High School, as well as hosted school tours so students can learn more about manufacturing careers.
“Any way we can be a support system for students on tool and die, CNC machining and anything manufacturing-oriented, we’re happy to work with those high schools,” he said. “We’re happy to let these students know that trades programs can provide a nice career path and they can do well for themselves.”