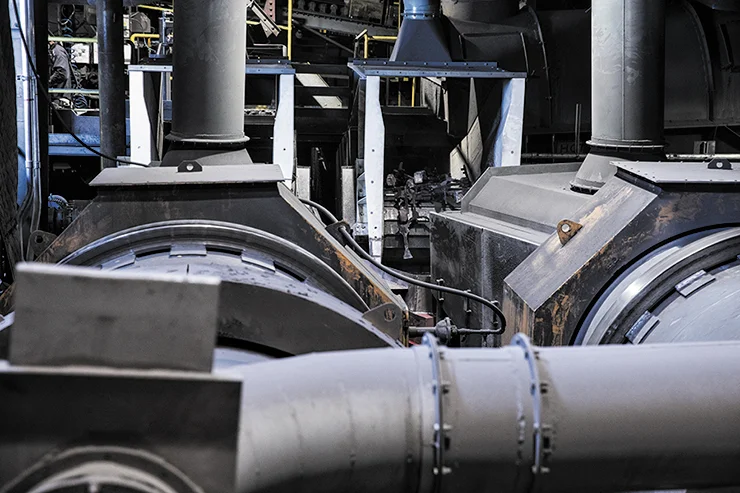
March 20, 2024
MARINETTE — Waupaca Foundry, a global leader in the production of ductile iron for a variety of industries, recently installed a new conveyor system at Plant 4 in Marinette.
The legacy vibratory shaker system was replaced with two parallel Magaldi Superbelt conveyor systems, which Mechanical Engineer Kris Olynick said are designed to offset maintenance and energy costs, eliminate iron casting jams, abate noise and decrease dust exposure.
The previous shaker system functioned, he said, by divorcing the sand molds from the iron parts with vibration after the iron was poured into the sand molds and cooled.
However, he said there are also paths within the mold for the liquid iron to reach the main cavity, which are not part of the final product and, in turn, also need to be broken off and dealt with.
The shaker system also sorted out the iron waste to be melted back down.
The legacy shaker system was prone to getting jam-ups, which Olynick said shut down all molding lines for repair and generated significant noise shaking the iron parts.
The vibratory process also generated airborne silica dust, which reduced the indoor air quality.
Upgrading with limited documentation
Olynick said one of the first and largest obstacles the foundry encountered when they began planning for the new conveyor system in 2022 was the limited space and documentation available for Plant 4.
“Plant 4 is a relatively small plant with a lot of equipment in a limited area,” he said.
In addition to the small space, the Marinette plant was built in 1974, so much of the original documentation was either not available or no longer accurate.
“The area we were looking at was congested with equipment, and not a lot of that stuff was documented,” he said. “There weren’t really any prints or models of that area, so it took a lot of time to understand what we were working with before we could start to plan for the changes that needed to take place.”
To accurately plan for the installation of the Magaldi system, Olynick said he had the planning team, made up of about 10 Waupaca Foundry employees, take 3D scans of the entire Marinette plant.
“The 3D scans were the first major step we took in 2022,” he said. “Knowing what I know now, I would have probably done some things differently, but it was the first time we’d ever dealt with something like that, so it was a learning experience.”
According to Vice President of Manufacturing and Engineering Jarrod Osborn, most large-scale foundry projects are undertaken during the two annual holiday shutdowns over Christmas and the Fourth of July.
Jarrod Osborn
“Christmas is usually a two-week window in which we work on most of our projects,” he said. “For this particular project, due to the scope, we extended that typical two-week time period (to 16 days) to account for it. So it was an aggressive project, even within the extended window that was given.”
Olynick said while it’s typical to undertake projects over the holiday shutdown, the installation of the Magaldi Superbelt conveyor systems was one of the most aggressive timelines he’s worked on.
“Our timeline goal was always to install the Magaldi system over the Christmas break — it was a matter of figuring out how to make that happen,” Olynick said.
The advantage of in-house engineers
Sara Timm, director of marketing and media, said the foundry’s successful timeline wouldn’t have happened without having a team of in-house engineers working as the project managers.
“The single reason why this project was able to be successfully executed on time was because they are intimately involved with the plant, its processes and its technology,” she said. “If you bring in somebody from the outside who doesn’t understand foundry equipment, it would not have gone quite as smoothly.”
Rob Jezwinski, engineering manager at the foundry, echoed Timm’s sentiment and said home-grown engineers were a huge advantage for the project.
“We live in this environment, so we were intimate with the details needed to create an efficient process and install an entirely new operating system for Christmas,” Jezwinski said.
Despite having an experiential advantage, Olynick said a project of this scope could not be completed by in-house engineers alone, so the foundry hired contractors Beson and Houle and IVI, as well as Spectrum professional engineers from the Upper Peninsula of Michigan.
“Working with outside contractors and engineers added a layer of complexity, but it was pivotal to getting the project done on time,” he said.
Overall, the labor force required for the installation of the Magaldi Superbelts involved more than 100 people.
“We had more than 60 contractors and laborers, 15 to 20 maintenance guys and about 20 electricians,” Osborn said.
Plant shut down for installation
On top of working with a short timeline, Osborn said the entire plant had to be shut down for the duration of the installation of the conveyor system.
“During this period of the project, the entire plant could not run, which is a pretty high-level impact compared to most of our projects that are more department — or pieces of equipment — focused,” he said.
While the conveyor system is one piece of equipment, Osborn said it ties all of the molding lines within the foundry together.
“There was quite a bit of prep work leading up to the main install over Christmas,” he said.
“We had to build columns, but we also had to remove other structural elements to give more access for our contractors to work on the equipment.”
Many adjustments had to be made to the interior of the foundry to create room for the Magaldi Superbelts.
“It wasn’t as simple as taking out the old equipment and sliding in the new equipment,” Timm said. “There were so many accommodations and so many adjustments, things like relocating ductwork and the two DIDION Rotary Media Drums that reclaim core and molding sand from the iron casting manufacturing process.”
Brandon Kruse, general manager of Magaldi Technologies, was onsite for most of the installation process, which Olynick said was pivotal to the process.
“Kris spent every other weekend at the plant for a good part of the year planning out column relocations, relocations for conduit, pipework, ductwork, sand conveyors and everything you could imagine,” Kruse said.
Other challenges
Once the Magaldi equipment arrived, Osborn said it still had to be pre-assembled outside the foundry before it could be installed.
“We started receiving containers of equipment around two weeks before the shutdown with the last of them arriving the week of the start of the shutdown,” he said.
Working around the local environment also created challenges for the team.
“There wasn’t space under the roof to store the sheer volume of stuff we had,” Olynick said. “Obviously, in Wisconsin in December, that’s a crapshoot. You don’t know if you’re going to be fighting snow or rain.”
While Olynick said the team was fortunate to not experience a lot of snow, he said they had to face another natural element instead.
“We did have some rain, so that made it challenging because those poor guys are outside in the rain, trying to pre-assemble the equipment and prepare it for installation,” he said. “But having Magaldi representatives present during that process was a huge benefit.”
In addition to the weather, the team also ran into physical obstacles like local infrastructure.
“There were also power lines in the area we had identified, so we had to be cognizant of that because we used a crane to take the stuff out of the containers,” Olynick said. “And doing all that work while the foundry was still running was the biggest thing. We probably made some people unhappy because their day-to-day had to change a little bit to facilitate what we needed.”
Benefits
Some of the benefits of the Magaldi Superbelt in contrast to the legacy shaker system, Olynick said, include an increase in safety, efficiency, noise reduction, cost reduction, energy cost reduction and ease of maintenance.
He said the new system is anticipated to reduce maintenance downtime in the shakeout area by as much as 50%.
“The motors that power the new conveyors are smaller than the motors powering the legacy shaker system, so weíre using less energy now, even though we are powering two conveyors instead of one,” he said.
The Magaldi Superbelt also improves Foundry 4’s work environment for employees.
The exterior of Plant 4, located in Marinette. The plant upgraded its conveyor system over its Christmas break with the help of in-house engineers and contractors. Photo Courtesy of Waupaca Foundry
“The biggest difference within the foundry is probably the noise,” Olynick said. “The pans on the new Magaldi Superbelts are high manganese alloy, so you can still hear when something is dropped onto the conveyor, but it just makes a thud. In contrast, the previous vibratory equipment was all lined with AR 500 sheets and when stuff would fall on that, you got all kinds of noise, plus the noise as a conveyor itself — having it vibrate like that is a violent process.”
The community around the foundry will also benefit from the new machine as well.
“Foundry 4 is built on a garbage dump, so there’s not a lot of structural support underneath,” he said. “It’s easy to shake that, and it was negatively affecting the community around it as well.”
Kruse said the lack of vibration on the Magaldi Superbelts means the iron returns do not collect and jam up and silica dust is not generated.
It also allows maintenance teams safer, easier access to the conveyors.
“There’s a lot more moving parts on a vibratory conveyor than there is on a simple belt-on-roller like the Magaldi Superbelt, so that should severely cut down on the required downtime for maintenance,” Olynick said.
While Foundry 4 puts its new conveyor system to good use, Olynick said the previous system served its purpose well.
“I don’t want to paint the vibratory equipment to be completely negative because it worked for us for many years,” he said. “But it was also near the end of its useful life.”
To learn more about Waupaca Foundry, visit waupacafoundry.com.