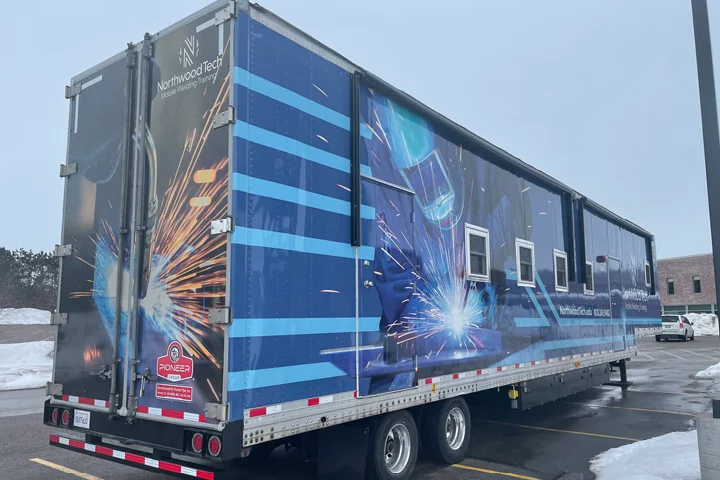
February 19, 2024
WEST CENTRAL WISCONSIN – According to The Wisconsin Manufacturing Report produced by the Wisconsin Center for Manufacturing and Productivity, workforce concerns top the list of manufacturers’ concerns – with 40% surveyed ranking finding quality and skilled people/employee retention as the top issue affecting their success.
In addition, according to the Bureau of Labor Statistics, the number of jobs in the welding field, specifically, is expected to increase by 22%.
The Northwood Technical College (Northwood Tech) is doing what it can to help address these gaps.
A win-win
Though Northwood Tech has four campuses – Ashland, New Richmond, Rice Lake and Superior – Dori Marty, director, grants/resource development, said transportation and other access struggles can sometimes create barriers to learning.
“For some people in the district, it’s more than an hour’s drive to each of the campuses,” Marty said. “We wanted to create training (we can take) directly to the communities so they don’t have to worry about transportation barriers to get to a college (site).”
With that in mind, Liz Pizzi, associate dean, workforce and community development, said the tech launched the Mobile Welding Lab – a 53-foot mobile welding lab offering much-needed welding education throughout the 11 counties and 10,500 square miles the college serves.
By bringing training to rural Wisconsin with the mobile lab, Pizzi said the goal is to help rebuild the workforce by producing quality-trained individuals, support the growing manufacturing industry and fill the current open positions.
“With the mobile welding trailer, we can provide training that is convenient for our students and business partners,” she said.
Pizzi said Northwood Tech is a great fit for “needs relative to welding, maintenance technology and machining,” which is never going to go away with the shortage there is.
“Our (on-campus) programs are always full for welding, and those labs are busy with daytime and nighttime programs, so the Mobile Welding Lab provides a solution for additional training,” she said.
Numerous West Central Wisconsin businesses seek stainless steel welding training in particular, but can’t send employees the distance to a campus.
“That’s a need the Mobile Welding Lab fulfills,” Marty said.
Fortunately, Instructor Keith Burns said he’s happy to travel wherever training is needed.
The lab even has a backup plan if a destination doesn’t have direct electricity – a $90,000 generator thanks to the generosity of Enbridge Energy and Cenovus Superior Refinery, two local companies.
Coming up on a year
Pizzi said the mobile lab began its inaugural welding course last April with eight members of the St. Croix Chippewa Indians of Wisconsin Tribe.
“The St. Croix Tribe asked the college to help them build their workforce with… skills that would allow them to become self-sufficient in trades,” Janine McNulty, higher education and community development research/recruiter at St. Croix Tribe, said. “Northwood Tech responded in partnership, compassion and support. The mobile welding training unit is proof that bringing opportunity to people in their place creates success.”
Students participated in the eight-week coursework, attending classes from 8 a.m. to 5:30 p.m. four days a week.
The curriculum included in-classroom instruction and hands-on learning in the mobile lab.
“The welding program gave a chance for someone like me, who works full-time and lives too far away from any college, to learn a new skill,” Jeff Taylor, Jr., a Mobile Welding Lab graduate, said. “I can now help my tribe in my (current) job or (use those skills to) help me in a new welding job,”
Pizzi said the college’s second partnership was with the Lac Courte Oreilles Band of Lake Superior Chippewa Indians, which also wanted hands-on, manufacturing-specific training.
Students within that learning arrangement, she said, also participated in a four-days-a-week, eight-week training from July through September, and two students earned their diplomas.
Thus far, Pizzi said the tech is pleased with the feedback it has received from students.
“We’ve had quite a few females in our cohorts who were curious about welding and figured out they were great at it, and I don’t know they would have come to a campus to check it out,” she said. “Because the Mobile Welding Lab was in their community and in a place they were comfortable with, they tried it out.”
Pizzi said one participant said he likely wouldn’t have considered welding but needed a job – after participating in the training and she said he realized it was a good fit.
“He was employed the day after he graduated and was super excited about it,” she said. “He was excited to buy birthday presents for his kids and to have that self-sufficiency.”
Pizzi said many students learn new skills they never thought they’d be good at and it builds confidence.
“(Many participants) are the first family member to get a technical diploma, and that’s powerful,” she said.
Funding and vision
The Mobile Welding Lab is part of the three-year Restoring Employment through Support, Training, Outreach, Recruitment and Education (RESTORE) project funded by the Wisconsin Economic Development Corporation and Wisconsin Department of Workforce Development as part of a $10 million Workforce Innovation Grant under the Federal American Rescue Plan Act. The RESTORE project presented a partnership between the college and Chippewa Valley Technical College to assist regions of Wisconsin to address and solve the critical workforce shortage in the growing manufacturing industry, while also providing highly trained individuals to fill current open positions.
The Mobile Welding Lab, Pizzi said, is one piece in helping to achieve RESTORE project goals, including:
- Enroll and/or serve at least 1,200 disconnected and underserved participants, including rural secondary students, unemployed and underemployed adults and incarcerated individuals by Dec. 31, 2024.
- Allow at least 900 participants to complete industry-recognized training credentials in metal manufacturing by Dec. 31, 2024.
- Allow at least 600 participants to gain or maintain employment, advancement opportunities and/or pay increases with regional employers following completion of training programs.
Pizzi said the lab is an integral part of the college’s expanding options for Industry 4.0 Advanced Manufacturing training.
With eight individual welding booths, students can practice hands-on skills and businesses’ employees can upskill their abilities to earn their customized welding credentials.
Depending on the customized training, Pizzi said credentials that can be attained not only include the stainless steel certificate, but also credits for shielded metal arc welding, gas metal arc welding, flux cored arc welding, gas tungsten arc welding and welding/maintenance and fabrication technical diplomas.
Building awareness
Pizzi said the Mobile Welding Lab’s existence isn’t a matter of “if you build it, they will come.”
Instead, she said its mere existence – at not even a year into availability – requires a lot of community outreach.
Pizzi said that has taken many forms, hitting the road to attend manufacturing events targeted to students in particular – including the St. Croix Valley Homebuilders Association’s Build My Future event in Glenwood City.
“There were about 1,500 students there learning about careers in construction and ‘critical friends’ of construction – and welding is one of those careers,” she said. “Students had a chance to come through the trailer, meet the instructor and ask questions of our students.”
Another outreach effort in the same vein was attending Manufacturing Day in Hudson – welcoming high school students inside the mobile lab.
Pizzi said the tech also hosted a Community Connections event open to the community at large to raise awareness of the mobile lab.
The college is also developing cohorts of incumbent workers already working in manufacturing who seek additional training, which Pizzi said should begin in March.
“Manufacturers are growing and looking to help individuals who are maybe in an assembly position who want to become a welder and (providing that training for them),” she said. “These cohorts will help train people who already work for them and help take them to the next level.”
The mobile lab, Pizzi said, also has the opportunity to fill a dire need for technical education in high schools throughout the college’s boundaries.
“We’re partnering with K-12 because we’re finding a lot of our high schools don’t have tech ed teachers or can’t keep them because they’re leaving for industry,” she said.
For more information on the Mobile Welding Lab and the opportunities available within it, visit northwoodtech.edu.