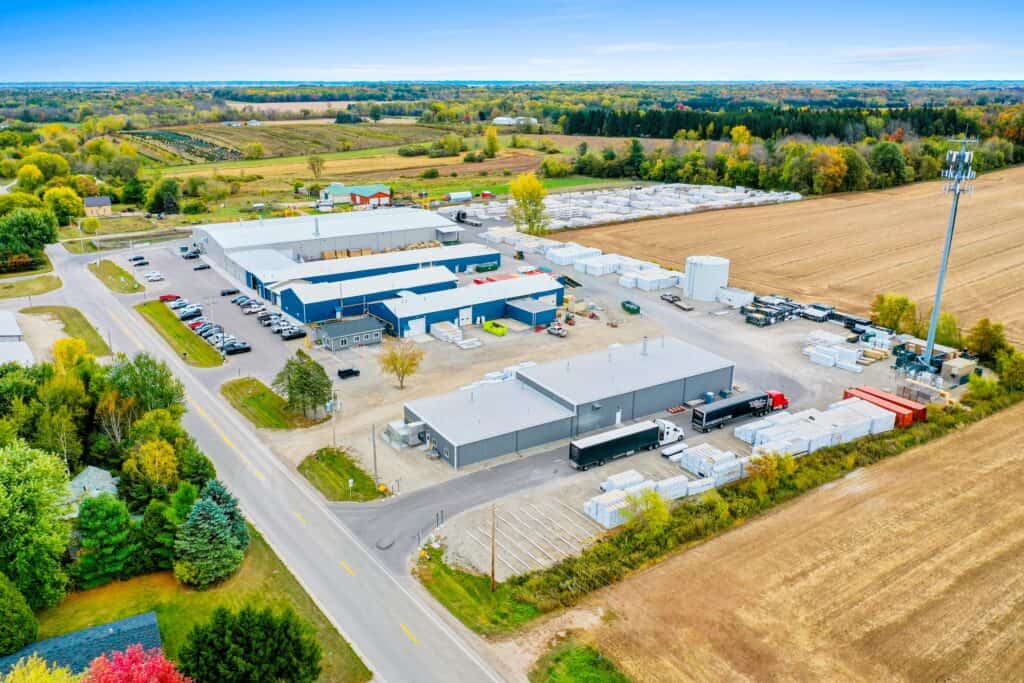
March 24, 2025
GREEN BAY – LP Green Bay, a manufacturing facility operated by LP Building Solutions, hit an impressive safety milestone earlier this year – 12 months, or the equivalent of 224,000 hours, without a worker injury.
Plant Manager Matt Holcombe said all four shifts of employees who work at the 4575 Anston Road location in Green Bay celebrated with a catered steak meal.
“Recognizing a job well done is important,” he said. “Especially as the number of people who need to work safely at the plant grows.”
Holcombe said the Green Bay facility – which makes LP Building Solutions’ flagship product, LP® SmartSide® Trim & Siding, as well as other exterior building products – has grown from about 40 employees when LP Building Solutions purchased the facility five years ago to 110 employees today.
“We celebrated as a team,” he said, “because it takes the entire team to make sure we work safely daily.”
Safety-first mentality
Dave McGowin, business EHS manager of LP Building Solutions, said the finishing plant receives exterior siding products from plants in Michigan, Minnesota, Wisconsin and Canada, then prefinishes and paints the boards before shipping the finished product to dealers around the country.
McGowin said Safety leads the way – from the beginning to the end of its processes.
“Safety isn’t what we do – it’s how we do everything,” he said. “We strive for safety to impact everything from our thoughts to our decisions to our actions. Safety is so much more than compliance – it incorporates people, processes, equipment, culture and succession for the future.”
It’s a culture McGowin said permeates all of LP Building Solutions’ locations, which have maintained a total recordable incident rate (TRIR) below 1.0 since 2007.
He said this safety metric measures the number of work-related injuries and illnesses in a company and is a key indicator of its safety performance.
TRIR is calculated by taking the total number of injuries multiplied by 200,000 and dividing by the total number of hours worked, McGowin said.
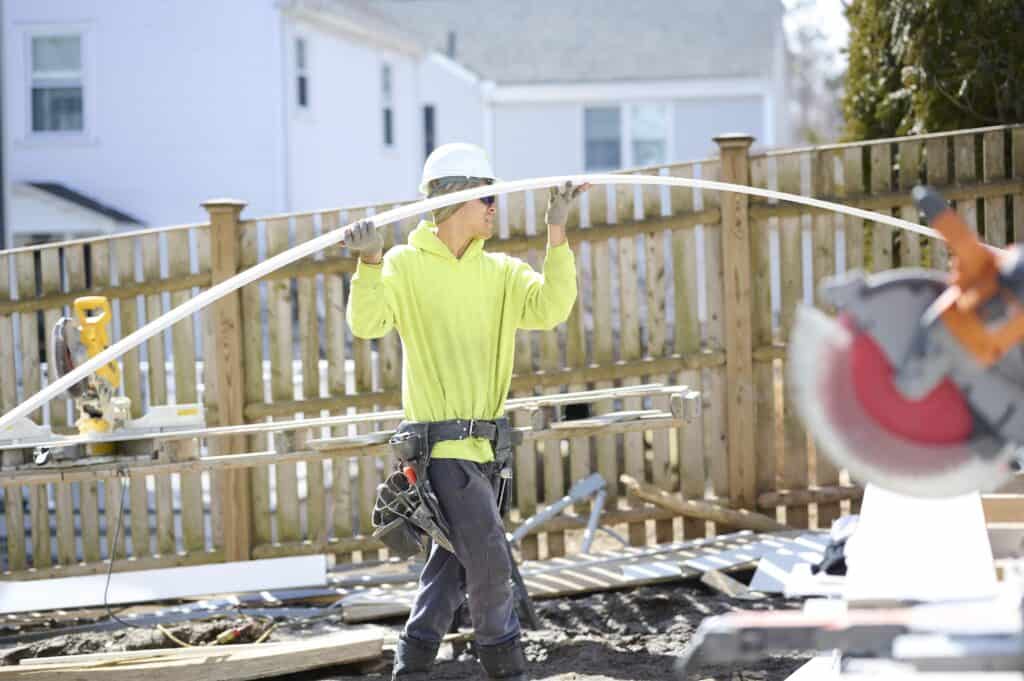
In 2024, he said LP Building Solutions improved this metric to 0.67 – an improvement Holcombe said he attributes to consistent behaviors across the Green Bay team, as well as the hiring of a safety manager in the past year and maintaining regular touchpoints with the corporate safety team and their peers.
“We do a lot of sharing among the plants at LP, learning from each other,” Holcombe said. “(An incident) may not happen at our plant, but it is something we can learn from during monthly calls, for example.”
Just as importantly, Holcombe said embracing safety is achieved by the steel-toed boots on the ground who consistently wear their personal protection equipment (PPE) and are willing to point out opportunities to do better.
“We have built a culture where they feel comfortable talking about improvements, whether for themselves or a different job,” he said.
A mindset of continuous improvement
Holcombe said one example of an employee-suggested change regarded the facility’s foam application station containing a hot wire.
He said an employee came forward with a suggestion to build racks to hold the foam differently so operators could open, reach and clean it better while also placing them in a work position that doesn’t require as much stretching and leaning.
“It was a really good suggestion and a pretty easy fix that we made quickly that really made the job safer,” Holcombe said. “Operators are always bringing up ideas for reengineering, and we would much rather engineer safety than mandate, ‘This is how you operate it.’”
McGowin said milestone safety achievements matter and are tracked, but what really matters are the everyday wins adding up to those milestones.
“We focus on celebrating the day-to-day wins,” he said. “Safety is a journey comprised of many steps, and each step is important.”
McGowin said LP follows the TRUTH model – an acronym for trust, respect, urgency, transparency and honesty – which is critical to safety.
Without those values being lived out each day, he said, employees wouldn’t share concerns or help with their improvements – and without their input, he said, improvement is impossible.
It’s a tone leadership upholds daily, McGowin said, in keeping with LP Building Solutions’ leadership principles across all its plants.
He said one of the principles is “Insist on Excellence.”
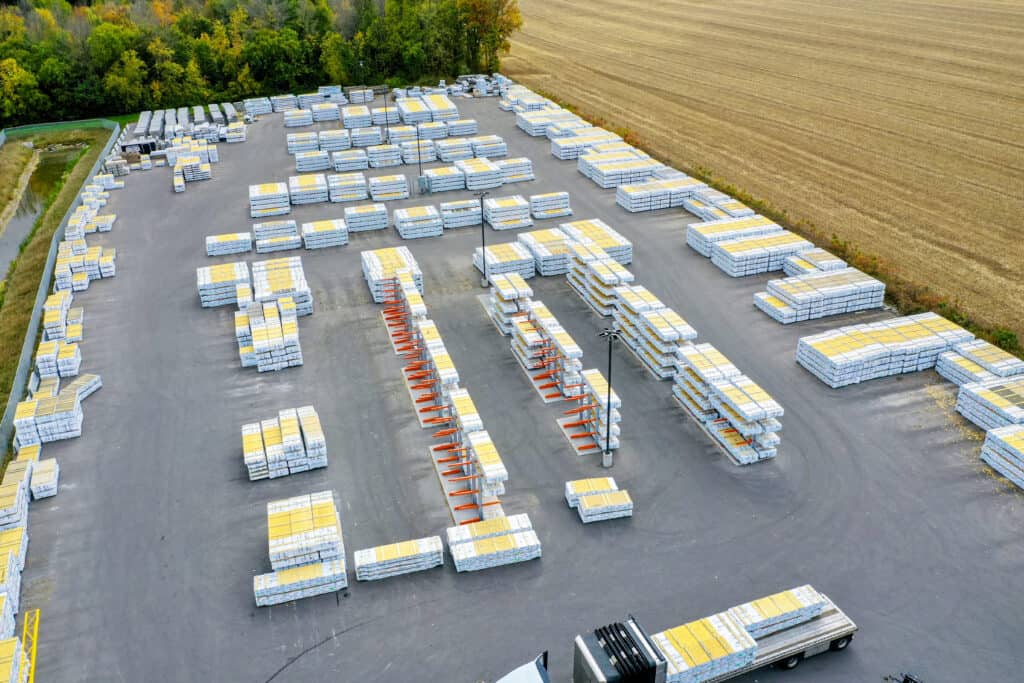
“We are never satisfied – one safe day must lead to another,” McGowin said.
He said the other leadership principles include:
- “Innovate and Simplify” – which looks to generate new ideas from the men and women working in its facilities every day to be the sources of key innovation
- “Join Forces” – which focuses on teamwork
- “Be Curious” – which leads to new ideas and approaches to safety as well as process improvements
- “Embrace Differences” – which encourages employees to do just that; showcase their unique perspectives and experiences that can help change things for the better
- “Lean In and Speak Up” and “Have a Bias for Action” – both of which encourage employees to make things happen
“This is where the fun discussions begin,” McGowin said of the latter principles. “Construction conversations with the unified goal of a safer workplace is the desired outcome. Every person should ask, ‘What am I going to do today to demonstrate my commitment to safety?’ The decisions we make today should result in a safer tomorrow.”
Safety leads each shift
The tone for safety, Holcombe said, is set anew with each shift.
Before team members get to work, he said they don PPE appropriate for their work, such as steel-toed boots that cover the ankle, high-visibility/reflective vests or shirts, long pants, hardhats, safety glasses and, for certain tasks, hearing protection, cut-resistant gloves and respiratory protection.
Holcombe said these behaviors occur regardless of which of the two day shifts or two night shifts employees work within the 24/7 plant.
Each shift begins with pre-shift safety meetings called toolbox meetings, he said, to get everyone focused and informed of what’s going to happen that shift.
“That’s fundamental to being safe, coming to work and going home the same way they came in,” Holcombe said. “That’s a core principle that drives us here.”
Once a month, he said the toolbox meetings feature an additional focus area – be it lockout/tagout or heat exhaustion in summer.
Holcombe said the meetings are intentionally short (10-15 minutes), with discussions covering topics affecting daily life in the plant, as well as stories about employees’ choices that resulted in accidents – whether due to rushing or being distracted – for all to learn from.
“We openly discuss that type of thing to make sure we’re focused when we get out on the line,” he said. “Be safe and be productive – that’s what the team is about here.”

Believing actions speak louder than words, Holcombe said the company shows its commitment to safety by investing in improved equipment.
All entities across LP Building Solutions follow the organization’s management system, he said, utilizing a safety program app for reliability inspections and audits and to ensure equipment is working properly.
Holcombe said the company rolled out a safe start program in 2025 that trained all team members at the local Pittsfield Town Hall in addition to the training that occurs monthly.
Rinse and repeat-repeat-repeat
Holcombe said LP Building Solutions has been recognized for its safety numerous times over the years – as he estimates LP has earned more than 90 awards in the past 12 years, recognizing safety practices throughout the organization.
These recognitions, he said, include the 2023 Safest Company Award from the APA – The Engineered Wood Association, which was LP’s 12th win in the 16-year history of the award program.
Holcombe said the award is considered the premier safety award program for North America’s engineered wood products industry, as it recognizes operational excellence aiming to reduce injury and illness rates among member companies.
Per apawood.org, awards are based on the lowest rate and severity of injuries, greatest reduction in injuries, innovations to reduce injuries and best overall company record.
And though Holcombe said it’s everyday efforts and a low TRIR that lead to significant recognition as such APAs, he said the drive to achieve great safety isn’t about the accolades – as nice as they are – as is doing the right thing by his team members.
“We are here to satisfy and take care of our customers, but our employees’ families are counting on them to come home the same way they came to work,” Holcombe said. “That is our number one goal.”