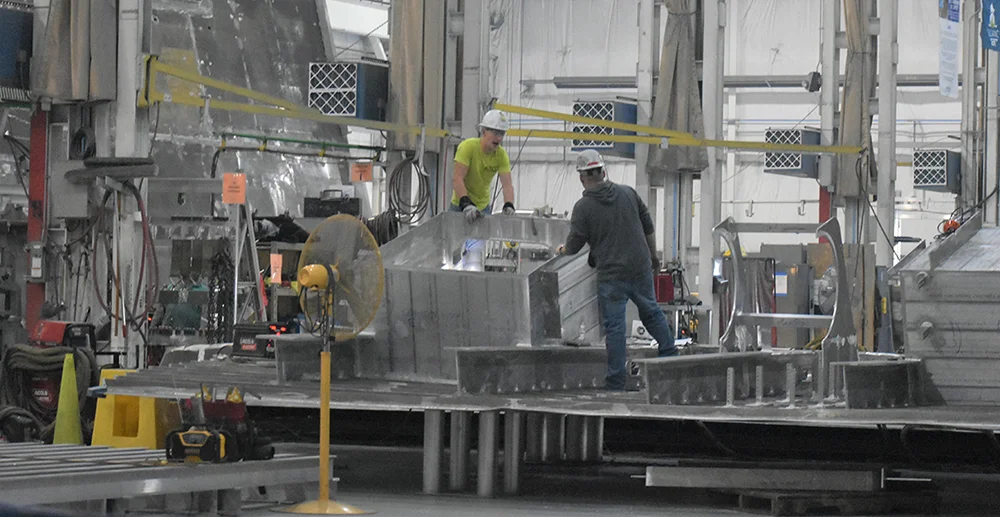
November 17, 2022
GREEN BAY – Anyone in the shipbuilding industry will tell you – building a ship is a process, with each step being just as important as the next.
Bill Boudreau, production manager at Fincantieri ACE Marine in Green Bay, said the Northeast Wisconsin aluminum welding expert plays a small, but important, role in that process.
“We’re the little kids on the block when it comes to shipbuilding,” he said. “Bay Shipbuilding (located in Sturgeon Bay) is bigger than us, and Marinette Marine is a lot bigger – they are huge compared to us. Marinette Marine is more exciting because you get to see the finished product in the water – a huge ship that will travel around the world.”
However, Boudreau said Fincantieri ACE Marine is proud of the part it plays in the process.
Currently, he said the team specializes in building the aluminum superstructure modules placed on the U.S. Navy’s Freedom-variant Littoral Combat Ship.
“It’s the part of the ship we most like building,” he said. “Pretty much what you see from the main deck up is what we do.”
Boudreau said the modules take three or four months to build.
“We haven’t shipped modules recently, so our building is full, with not a lot of space…” he said. “When they are shipped to Marinette, suddenly, we have all kinds of space.”
According to Fincantieri’s website, fincantierimarinegroup.com/ace, the company is also the builder of the Response Boat-Medium for the U.S. Coast Guard, U.S. Army Watercraft – Maneuver Support Vessel (Light) and Legacy LCM-8 Landing Craft – and the V.1600 High-Speed Intercept Vessel, which is used in border security, littoral patrol and counter-drug operations.
Aluminum work
Fincantieri ACE Marine – located at 201 S. Pearl St. on Green Bay’s near east side – works entirely with aluminum – which Boudreau said has pros and cons.
“Aluminum is much cleaner to work with, but it can also be trickier in some respects – it’s a specialized skill, so that’s why we aim to keep talented aluminum welders around,” he said. “Welders who have worked with aluminum for years don’t always like to switch to steel.”?
Boudreau said aluminum is “alive.”
“You have to know when to turn up the heat and move quickly when welding, otherwise you warp the material – you have to weld fast,” he said.
Boudreau said though its focus is being a cog in the shipbuilding process, it won’t shy away from smaller aluminum jobs.
“On a smaller scale, if welding aluminum trash cans employs 75 people, for the time being, we’ll take on the job,” he said. “We are the aluminum center of excellence – that’s our motto. We do it better than anyone in the state, and it’s earned us these bragging rights. I tell folks all the time – what you’re going to see is the highest-quality work around.”
Pearl Street operations
Fincantieri has two production buildings at the Pearl Street facility – separated by a short walk.
“One of the buildings is bigger, and that’s where we have the modules that are being put together,” Boudreau said. “The other building is smaller because it’s the start-up work for the modules – they don’t take up as much space.”
Boudreau said though supply chain issues have delayed shipping to Marinette lately, the company continues to focus on making sure everything is right.
“We’re trying to incorporate a lot of change into the ship we’re building right now so we don’t want to send the modules to Marinette and then (have) them struggle to try to redo the work,” he said. “Everywhere you go right now, there are supply chain issues.”
Worker shortage
Boudreau said finding enough workers is also a challenge.
“Besides the supply chain issues, our number one problem is finding, training and retaining people,” he said. “Everywhere you go, it’s trades, trades, trades, trades. We’re like everyone – we’re getting into the high schools more trying to talk to the shop classes and put on aluminum welding classes that try to get people interested.”
Boudreau said if you have the desire to work, Fincantieri is willing to train you.
“You don’t have to go to college to do this – we can train you, with pay,” he said. “You can jump into aluminum welding, electrical or anything you want to do. At Fincantieri, we have every trade you can think of because a ship is wires, plumbing, painting and construction. What we’re building just has motors in them and go fast in the water.”
Boudreau said starting wages start at $17 per hour and up.
A worker at Fincantieri ACE Marine, located at 201 S. Pearl St. in Green Bay, prepares to grind an aluminum weld during the shipbuilding process. Rich Palzewic Photo
“If you stick with it, your pay can quickly escalate,” he said. “As with many trades, you can’t have a short-term vision – you have to look long-term. If you do that, you can make a very desirable living wage. We mostly work four, 10-hour days.”
Though the COVID-19 pandemic has contributed to some of the employee shortages, Boudreau said he saw a shift as early as 2014 in finding quality aluminum welders.
“We didn’t need a training program before at Fincantieri because we had our pick of talented aluminum welders,” he said. “The problem was, many of those workers were at the end of their careers – they were seasoned workers who maybe liked building boats for the Coast Guard but didn’t want anything to do with other work.”
Boudreau said since 2014, Fincantieri has had to develop its own good training program.
And though finding good candidates to enter the program is sometimes a challenge, Boudreau said it’s exciting to be a part of.
“If shipbuilding was easy, everybody would do it,” he said. “It’s heavy industry and not the easiest work, so that maybe scares people off a little bit as well. But people who do it feel rewarded loading the modules up, seeing the stuff leaving and going north to Marinette to get installed. People feel a good connection to that and feel important. I can’t make shipbuilding easier – it’s never going to be Legoland – but I’m constantly talking to our employees to see how we can make it better.”
In an effort to continue improving, Boudreau said every two years, Fincantieri conducts employee surveys.
“We listen to what our employees say,” he said. “Currently, we have 65 hourly people and 10 salaried management folks. We are (also) hiring right now. There are lots of job opportunities – Fincantieri is a great company to work for.”
Fincantieri ACE Marine is one of three Great Lake shipyards within the parent company Fincantieri’s Marine Group – with the others being Fincantieri Marinette Marine and Fincantieri Bay Shipbuilding.
According to its website, Fincantieri is one of the world’s largest shipbuilders in the world, with 18 shipyards on four different continents and employing nearly 20,000 shipbuilding professionals.
Since 1790, Fincantieri has designed and built more than 7,000 ships.