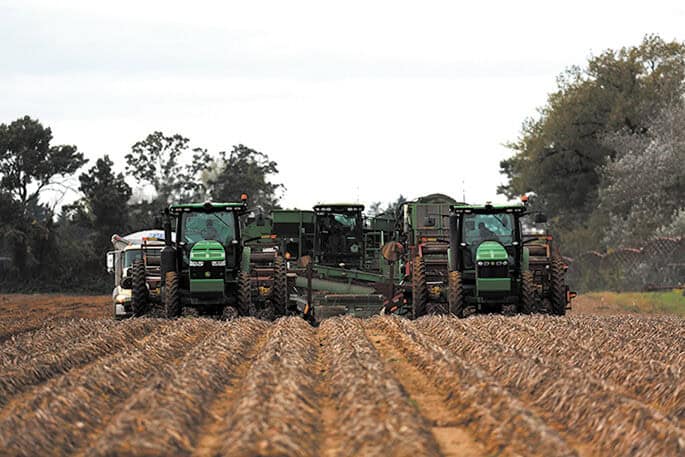
January 9, 2024
HANCOCK – “That’s the way it has always been done” – is an unacceptable phrase within Heartland Farms, Inc. – a fifth-generation, family-owned potato and vegetable farm located in Central Wisconsin.
“If you’re not moving forward, you’re moving backward,” Jeremie Pavelski, president of Heartland Farms, said.
For the past 150-plus years, Pavelski said Heartland Farms has worked to continue moving that dial forward – focusing on sustainability and best management practices for the long-term and in day-to-day operations.
“We always keep our eyes open, rip the blinders off to say, ‘How can we push the boundaries? What is the next thing we can do?’” he said.
A bit of history
Heartland Farms was started in 1873 by Pavelski’s great, great grandfather who immigrated to the United States from Poland and homesteaded 80 acres in Amherst Junction.
“My Uncle John still farms that land today,” he said.
Much growth has happened since, Pavelski said, with the 1990s serving as the impetus to “changing the whole way of farming.”
“Before 1994, potatoes wouldn’t be sorted – and what I mean by sorted is any of the rocks, the soil, cork stubble would end up going down to whatever manufacturing facility that was receiving the potatoes,” he said. “Most of those manufacturing facilities were in larger cities or on the outskirts of larger cities, so you can imagine all that going down the municipal water system and wreaking havoc. (We also) want to keep that soil on the farm.”
Updating that process, Pavelski said, changed the industry as a whole.
“Anything that doesn’t meet customer specifications, rather than transporting it and having all those miles and all that energy in it, we can apply it back out on a field and get some nutrient value from it for future years,” he said. “So, that changed the industry as a whole, which is unique. And we’ve continuously grown ever since then.”
Heartland Farms today
Today, Heartland farms 27,000 acres spanning across five counties in Central Wisconsin.
“From our main site here, all of our fields are within a 40-mile radius,” TJ Kennedy, Heartland Farms’ vice president of operations, said. “One-hundred percent of our land base is irrigated. Our soil types range from sandy to sandy loam, loamy sand to even muck – so we have a wide variety of soil types.”
The growing season starts in February with seed delivery.
“We will start warming that up,” he said. “Then we’ll cut the seed, usually at the end of March, early April and suberize – (a process that creates a protective seal over the wound protecting it from infection) it.”
The farm’s planting window, Kennedy said, runs from around April 10th to May 5th.
“We have six different planters going so we can get all the potato acres in a timely basis – and that involves the entire crew,” he said.
Heartland’s harvesting window, Kennedy said, begins around the first week of August “where we’ll direct dig off the field to the rinse plant.”
“But the big push is around Labor Day to about Oct. 10,” he said. “Because we’re primarily a storage grower, where roughly 80-85% of our potatoes go into storage, so that’s the big push.”
Pavelski said Heartland employs about 120 full-time employees year-round, with approximately another 220 on a seasonal basis at different points in the year – including planting and harvesting.
Pavelski said though he is the fifth generation of the Pavelski family at the helm of the farm, the crew and leadership team is made up of a variety of different families.
“We like to consider ourselves as a family of families,” he said. “It’s all of us coming together from different backgrounds and different views trying to figure out how to make the best of everything we have. I always say that ‘we may not be related by blood but we are by sweat.’”
Kennedy said Heartland’s fields are on a three-year potato plant rotation.
“We’ll grow right around 9,000 acres of potatoes a year,” he said. “You can’t continuously grow potatoes every year. We have a lot of different vegetables. So if it’s potatoes in year one, year two might be sweet corn, might be snap beans. There is a fair amount of field corn also grown, as well as soybeans. And then the third year, it would be peas, beans, soybeans and then back to potatoes after that.”
The rotation, Kennedy said, is for soil health.
“Certain crops utilize more nutrients or less nutrients,” he said. “You want to have good, healthy soil, and rotation helps drive that.”
An engineering mindset
Working to evolve itself and the industry, Pavelski said, is something everyone at Heartland Farms takes great pride in.
“It’s not something that happens overnight – it’s built into the overall culture,” he said.
Though he grew up on the farm, Pavelski said, at first, he didn’t know if taking over the family business was in the cards for him.
“I worked on the farm as a kid,” he said. “My first paycheck was in first grade. It was $8. I had a unique ability back then because I was so short that I could get underneath all the conveyors – it made it a lot easier for cleaning companies.”
However, having an interest in technology development while in high school and college, Pavelski said he spent much of his time programming, writing software and networking.
“I wasn’t sure if I wanted to continue to run the family farming operation,” he said. “But I quickly realized that technology and agriculture were on a head-on collision course. The reality is, I got to have my cake and eat it, too – which doesn’t happen often.”
Pavelski said much of Heartland’s leadership and crew have engineering or technology backgrounds – including Kennedy.
Though he grew up on a family farm until middle school, Kennedy said, he, too, followed an unconventional path to a career in agriculture.
“I had worked for a crop consultant through high school and college, but at that point, I thought I was going to be a civil engineer because that was intriguing,” he said. “But after a couple of years in school on that, I took a left turn back to agriculture and transferred to ag school. It’s been in my blood, and I love doing it.”
Pavelski said that broad engineering mindset helps drive many of the decisions at Heartland, especially in terms of technological advances and sustainability practices.
Farming of the Future
Serving as Heartland Farms’ slogan – Pavelski said Farming of the Future comes down to “making sure we can continue for future generations.”
“I don’t know if my daughter is going to want to join (the family business), but if she does, I want to give her that opportunity,” he said. “And the same goes for all the rest of the families. We can’t do that if we’re utilizing all the soil resources, making it so the soil is not healthy, if we don’t have enough water – so it’s the whole mindset of continuously improving the land.”
Pavelski said this is accomplished through several technological and sustainability practices and procedures that Heartland has and continues to implement into its operations.
“We talked about us being one of the most advanced, if not the most advanced farms out there – and it’s because we have that passion and drive for continuous improvement and looking at the future,” he said. “We take a lot of risks… sometimes it works out, sometimes it doesn’t. It’s playing on that leading edge versus the bleeding edge – and we occasionally get cut. But, without doing that, you can’t push ourselves, for one, but a lot of the things we do also change the different standards for the whole industry.”
Sustainability practices, procedures
Heartland’s irrigation systems, Kennedy said, have seen many advances over the years – which has contributed to the farm’s sustainability efforts.
“All of our pivots have been switched over to low-pressure systems, so you need less energy for those,” he said. “We have a fair amount of pivots that have variable-rate irrigation, which helps because even though we’re in sandy soil, there are some variations… We can write subscriptions and say we only want a couple of tenths of an inch on this type of soil and no water at all on the heavier stuff.”
Kennedy said this is important from a vegetable standpoint, but also from a sustainability standpoint because we are reducing the overall water usage we’re using.”
Another advance of the irrigation systems, Kennedy said, is each nozzle can be controlled, which contributes to flexibility and accuracy.
Pavelski said through Heartland Farms’ sister company Heartland Ad Tech, “we develop a lot of the technology down to the circuit board level.”
“With that, we developed what we call our end gun monitor,” he said. “It monitors more of the irrigation system so we can tell if we’re getting uniform water distribution if we’re not getting uniform water distribution. And if an irrigation system has an ending gun on it, which most of us do, that typically covers about 10 to 15% of the total acres. If it’s not functioning properly, you’re going to have quality issues and yield loss.”
Pavelski said Heartland Farms has GPS technology on its tractors and the implements behind them which helps maximize land use by planting straight rows, only applying fertilizer and seed where necessary and harvesting those exact rows to reduce defects and waste.
“We only plant what can be watered,” Kennedy said. “So, implementing row shut-offs with that technology is important… Being able to get to the boundary of the field and having the planter shut off when it hits that boundary so we’re not overplanting, so we’re not using more seeds than we need to, so we’re not using more protections than we need to – (GPS technology) allows us to eliminate some of that waste.”
With all of Heartland’s equipment, Pavelski said it’s about “what was out there today versus what was out there yesterday, and is there any improvement.”
“We look at that not just from an overall efficiency standpoint, but from a team member happiness or wellness standpoint that says ‘okay, we’ve had automatic transmissions versus stick shift for a long time – that makes it a lot more comfortable for them to drive,’” he said. “It also comes into play when we do some automation in our harvesters, which requires less interaction by the operator because they’re doing a lot of things already.”
Making sure the equipment is not worn out, Pavelski said, is also important.
One of the newest pieces of equipment in Heartland’s fleet, Kennedy said, is drones.
“We like to be on the leading edge of technology, so last year, we purchased a drone to apply crop protectants,” he said. “We wanted to walk before we ran, so we didn’t stumble (using one drone in 2023) – and it went off well.”
Heartland Farms, Kennedy said, plans to purchase and implement more drones during the 2024 season.
“(The drones) allow us to spray in sensitive areas where you may have more residential,” he said. “And you don’t have sprayer tracks in the field from the ground sprayer, which trim yields or are the louder airplane. We are going to go up to two, if not three, drones this year – there are benefits there.”
The drones, Alicia Pavelski, project coordinator at Heartland Farms, said also improve overall accuracy.
“We can spray just the edges of the fields if there is pest pressure coming in so we’re not spraying an entire field,” she said. “It’s been extremely effective, and it’s going to reduce the overall carbon footprint.”
Potatoes, Jeremie Pavelski said, are water-sensitive.
“We talk a lot about water because it’s something that’s always on everybody’s mind – we want to make sure you’re taking care of it, and making sure the crop gets what it needs,” he said. “So, it’s one of those places that TJ and his team and all of us spend a lot of time in.”
Kennedy said potatoes are much like humans.
“They need oxygen – if they get into an anaerobic condition where your soils are saturated if you apply too much water, they’ll get stressed,” he said. “As I said earlier, most of these potatoes will get harvested and put into storage, and we have to store those potatoes from September until June. If you don’t have a high quality, low disease pressure potato, the chances of success are slim.”
Heartland, Kennedy said, has state-of-the-art storage facilities, but “it’s not a hospital.”
“If you put poor-quality potatoes in, we can’t fix them,” he said. “But, if we put good quality potatoes into storage, we can maintain that quality.”
The storage’s envelope design, Kennedy said, is like a building inside a building.
“So, during the winter months when it gets cold, there won’t be any condensation on the ceilings or the outside walls – potatoes do not like free moisture,” he said.
Each storage facility, Kennedy said, has its climate control.
“We can control the humidity levels,” he said. “You need to have proper humidity, which is around 95%, otherwise you can dehydrate the potato – which is about 80% water.”
Kennedy said temperature management is also critical.
“Again, potatoes are just like humans, they need oxygen, they give off CO2 – so having those state-of-the-art storages, you’re trying to minimize any stress on that potato,” he said.
Pavelski said Heartland Farms’ storage facilities give the team the ability to create and maintain the perfect environment “for our little babies, if you will.”
“You don’t want to shake them,” he said. “You don’t want to have them too warm. You don’t want them to be too cold. You essentially want them to hibernate to some extent without waking the bear.”
Alicia said all of Heartland’s storage facilities also have variable frequency drivers for energy efficiency.
“And a couple of years ago, we upgraded all of our lighting to LED so we could have the energy savings there as well,” she said.
Kennedy said Heartland also has remote technology for each of its storage bins.
“If you go back 15-20 years, you physically had to drive to the bin, check all the stuff out,” he said. “Now you can view all of that data on your iPhone, iPad, etc. You still have to get in there and look at stuff, but having that data at your fingertips is beneficial.”
Pavelski said Heartland has also deployed automatic rain gauges to all of its fields.
Normally after a rain event, he said, staff would have to drive around to each field to turn on and off irrigation systems depending on whether they’ve received enough rain or not.
“That process was typically about two hours,” he said. “Right now, if we’ve received enough rainfall, we can immediately turn off all of those irrigation systems. One hour of running every irrigation system on the farm would be like 18 million gallons. So, you essentially double that for how many gallons of water we save by having those remote sensors.”
Heartland Farms, Kennedy said, also plants cover crops to minimize soil erosion.
“The cover crops we primarily use are rye or winter wheat, oats at times, and we have dabbled in tillage radishes,” he said. “Overall, from a soil health standpoint, cover crops are a good thing because it keeps that soil actively growing. Come springtime, when we go to plant, that cover crop is already actively growing, so the soil is stimulated, it’s not compacted – that’s a benefit.”
To reduce tillage passes, Pavelski said Kennedy and his team implemented an aerial application process.
“We have an airplane (drop it) on in front of the harvester when we’re harvesting potatoes because the harvesting process itself incorporates it into the soil,” he said. “By doing that, we’re typically getting that cover crop established about eight to 10 days faster than we normally would have. You get a jumpstart on that…There’s less duration of time when the soil is not covered, so that potential for erosion also goes down.”
Data management, Pavelski said, is a huge part of what Heartland Farms does.
“Whether it’s sensor data or application records or crop data, in any given five-minute period, we’re pulling in roughly 200,000 data points,” he said.
As much as that data is important, Pavelski said “it’s worthless unless it becomes intelligence.”
“So, we spend a lot of time working on getting the right reports out to the right people doing the right comparisons,” he said. “We started recently incorporating some AI technology to help with that analysis.”
Today, Pavelski said the Heartland IT team is made up of 16 employees.
“They are working on the infrastructure, the data management and programming,” he said. “We have our own development crew for any of the applications we have. Many of the iPad apps for collecting data, we build that all in-house.”
From a food safety standpoint, Kennedy said thanks to Heartland’s data management practices, he can track all potatoes from seeds to market.
“I can’t say this specific customer… but I can grab a bag of potato chips off the shelf and type in the code that’s listed on it, and within 10 seconds, I can tell you every single thing that happened with that potato chip,” he said.
Alicia said going one step further, not only can Heartland see where the potato came from, but it can also see everything that was ever applied to it, where it was grown – “the whole story, it’s better than Ancestory.com.”
Renewable energy, Alicia said, is also part of Heartland’s overall sustainability mindset.
“Our office building has 95 kW of solar – in Central Wisconsin, that made the most sense for an alternative energy source, especially with our farming operation,” she said. “We’re looking at installing more now that solar is becoming a more viable option and more efficient.”
By 2030, from a carbon standpoint, Pavelski said, Heartland will be close to net zero, if not surpassing it.
“From that standpoint, the question is, ‘when do you pull the trigger on making larger investments in that?’” he said. “Right now, over about seven years, the overall efficiency of solar has essentially doubled.”
Always moving forward
Technology, Pavelski said, is a huge part of “everything everyone does these days.”
“Unless you’re looking at the latest and greatest technology, and have the team that can implement it and utilize it, you can’t move anything forward anymore on the continuum,” he said.
In reality, Pavelski said when talking about sustainability efforts, “a lot of those things directly go to profitability as well.”
“If we can reduce fuel usage by 10% – that’s a big expense in our organization,” he said. “If we can reduce crop protectors by 5%, 10%, whatever it ends up being – that goes to the bottom line. So, there’s always a balancing act done.”
How quickly can those technologies and practices be put into place for the desired results, Pavelski said, is typically where much of the conversation lies.
“Whether it’s man-made climate change, or whether it’s just cyclical – there’s a million debates on it – Mother Nature is changing, she’s a little bit different than she was last year and in the previous year,” he said. “We take a look at it from our records and it seems like there are some fairly substantial cycles, but by utilizing technology and the sustainability type things, it’s how do we make sure it doesn’t change to the detriment of the region, the U.S., the world. The end goal is making sure it’s better for the future is what it comes down to.”
For more information on Heartland Farms, Inc., visit heartland.farm.