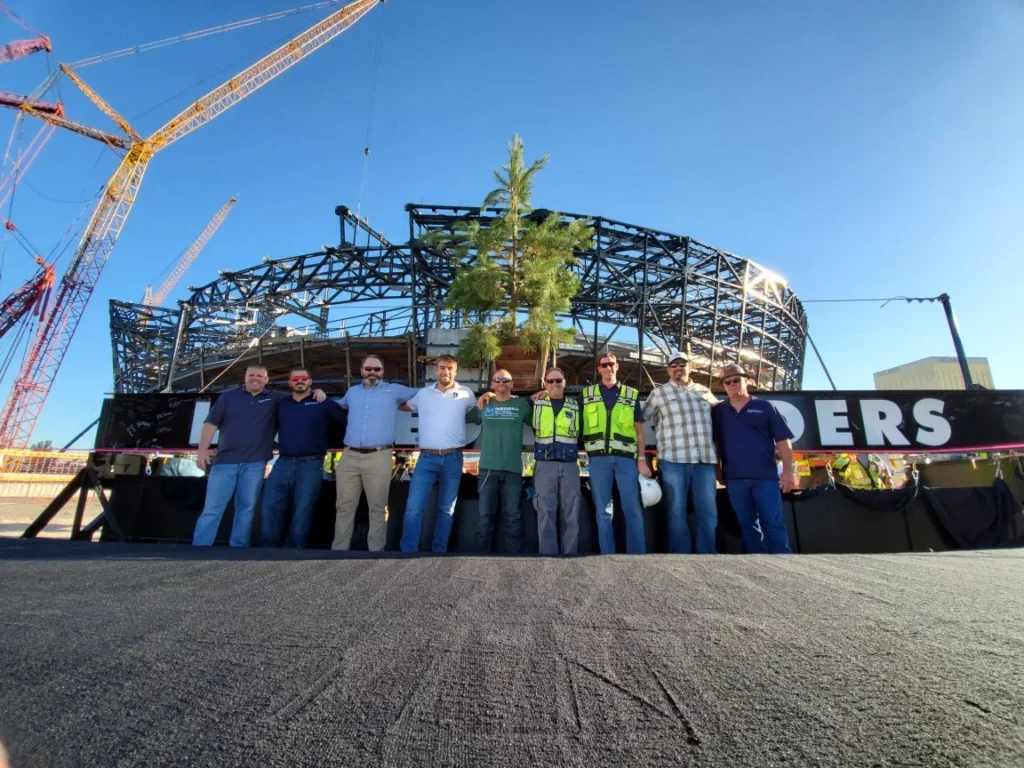
April 1, 2024
SCHOFIELD – The Green Bay Packers may not have made it to Super Bowl LVIII at Allegiant Stadium in Las Vegas, but there was still a strong Wisconsin presence there – besides the Lombardi Trophy, of course.
The Badger State was represented in the form of 57 million pounds or 28,500 tons of steel – courtesy of Merrill Steel.
The Central Wisconsin-based company won the bid to be the structural steel contractor for the project in early 2018 – meaning the company would purchase, fabricate and install the structural steel system for the stadium.
Darren Brown, regional sales manager, said when the company won the contract, the team got to work right away.
“We began immediately working on the pre-construction phase of the project such as engineering, shop drawing production and material procurement, soon followed by production,” he said. “The site activities, such as civil site work, had already begun upon our award.”
Timing, Brown said, was of the essence to meet tight NFL deadlines.
According to the company’s Facebook page, “working closely with the design team on every aspect of this unique structure, there was no challenge presented we did not tackle head-on. Items, such as the first-ever cable net ETFE (or Ethylene TetrafluoroEtilene – a transparent plastic material designed to have long durability for outdoor applications) roof structure built in the USA, to the retractable field tray that allows for a natural grass playing surface – there was no shortage of complex design elements in this structure that required our expertise to complete in time to support the 2020-21 football season.”
Brown said Merrill Steel’s part of the project – the erection of steel – was completed in August 2019.
“The total duration of construction was 34 months from the start of earthwork to occupancy,” he said. “The tight deadline was to ensure the stadium was ready for the 2020 NFL football season as the Raiders had already left Oakland and did not have an alternate location to play that season.”
Allegiant Stadium, Brown said, was not the first sports venue Merrill Steel has worked on. “Other high profile jobs include Lambeau Field Renovation Projects – i.e. the atrium expansion in 2001 and the south end zone enclosure project in 2011; Fiserv Forum, Milwaukee; and Allianz Field, St. Paul, Minnesota.
The company, he said, has also fabricated steel assemblies for:
- U.S. Bank Stadium in Minneapolis, host of Super Bowl LII
- Miller Park in Milwaukee
- Camp Randall Stadium in Madison
- Soldier Field in Chicago
- Kansas City Wizards Stadium in Kansas City, Kansas
- Mercedes Benz Stadium in Atlanta
- Citizens Bank Park in Philadelphia
- Tyson Events Center in Sioux City, Iowa
- Detroit Events Center in Detroit
Not just sports venues
Though Merrill Steel has extensive experience in the construction of sporting and events venues throughout the country, Brown said the company has played a significant role in many other varied projects as well, including the Resch Center in Green Bay, the Orlando International Airport, Detroit Metropolitan Airport and the University of Notre Dame.
The company, he said, is or has also been involved in projects within the commercial field, health care, industrial, power and energy, technology and EV (electric vehicle) automotive.
“Merrill Steel is currently involved in several EV automotive projects throughout the country for Ford, GM, Toyota, Rivian, Tesla, Honda and Scout,” he said. “These projects include the battery facilities in which the batteries are produced, along with the new factories in which the vehicles are assembled. The data center and semi-conductor construction market has also been keeping us busy.”
A bit more history
Merrill Steel got its start in 1962 when it was founded by Roger W. Hinner – who purchased a 5,000-square-foot foundry located in what was known as “Tannery Town” in Merrill.
In its early years, the company’s primary business was the fabrication of steel bulk storage bins for the local farming community.
As demand grew, Merrill Steel quickly expanded, satisfying the commercial agricultural needs throughout the Midwest.
Over time, the company diversified its offerings/capabilities to include the fabrication of structural steel and heavy plates for the general construction industry, along with expansion into industrial construction for the pulp and paper industry.
Again responding to demand, the company relocated to a 365,000-square-foot manufacturing facility in Schofield in 1995.
The company acquired a 160,000-square-foot structural steel facility in Springfield, Missouri, in 2016, which continued to fuel expansion into new markets, particularly projects requiring plate work.
The most recent expansion came last year, when Merrill Steel acquired a facility in Camanche, Iowa – which, due to its sheer size, is used primarily for painting, fireproofing and steel storage.
Brown said over the years, a part of Merrill Steel’s – which is currently under the direction of Company President Fred Schwalbach – history that has always remained true is its original company culture – “We are customer driven.”
Always recruiting
Because of its many projects, Merrill Steel is not only looking for new hires at this time, but they are always recruiting for new talent, as well, with the majority of work available in its three production facilities.
Staffing the facilities, Danielle Hertel, Merrill’s human resources (HR) manager, said comes with a consistent need to recruit new talent – an effort that starts early with local middle and high school students.
“We’ve found if we plant the seed early, we’re more likely to get them once they are graduated,” she said. “When I first started here, I did a study with our new hires that had been here for one year and under. I found a significant portion of them had been through our tours at a younger age.”
The Central Wisconsin Manufacturing Alliance (CWIMA), Hertel said, sponsors a Heavy Metal Tour every fall, during which many middle and junior high students from the area tour the Merrill plant in Schofield.
This past fall, she said, about 200 students toured the facility.
Hertel said Merrill also works directly with the schools to reach students.
“Besides inviting schools in for tours, we also go visit local classrooms to give presentations about the welding industry,” Hertel said, adding the company also frequently participates in career fairs held in the area. “We get in front of as many different schools as possible. We also go to as many college career fairs as we can.”
The company’s most recent appearance, Hertel said, was at the Wausau Area High School Job Fair held last month, which was attended by nearly 500 students.
“A lot of (students) either know what they want to do, or they have no idea what they want to do,” she said. “So, we try to give them an overview of what we do and invite them to come in for a job-shadow. That’s one of the things we’re open to doing for any high school or tech college-age person. By doing a job shadow, they can see what that type of job looks like; and that’s for office positions such as project management, engineering, IT, HR or any of our production-related jobs.”
Whoever they’re shadowing, Hertel said, provides students with an overview of what they do during the day, as well as walks them through their tasks.
“They wouldn’t have them do the job because we want to make sure we’re mindful of safety,” she said. “But, they’d explain to them and then show them what an average day looks like. Sometimes, you might get an idea in your head that something sounds like a great career, and then you come in and shadow someone and find it might not be what you expected.”
Job shadows, Hertel said, typically last for half a day or less – giving “them the exposure of what that job would look like for them without having to put in any manual labor for it.”
“I think the more exposure you can give to students to as many different career fields, the better it is because it allows them to better determine what they want to do when they graduate,” she said.
Going one step further, Hertel said Merrill Steel employees also help middle school students with career training by participating in mock interviews.
“They have classes where they learn job skills or job-related skills, like interviewing skills, so we do a lot of mock interviews for them,” she said.
Though Hertel said she thinks the company’s level of recruitment is probably average for the area of the state, “I like to think we go above and beyond.”
“In this area for recruiting, our population can’t keep up with the demand of manufacturing, so we probably put in more than most to make sure we’re recruiting the top talent for our production floor, and office, too, for that matter,” she said.
Hertel said Merrill Steel evaluates its recruiting efforts every couple of months to make sure it remains competitive.
“We have a weekly meeting to talk about recruiting – it’s that important to our company,” she said. “Our president is usually there, along with all managers from all different areas of the company, somebody from operations and the plant manager. We have all three locations present so we can talk about if any issues are coming up we want to talk about, any career fairs, any events in the community we want to participate in.”
Hertel said recruiting is something companies have to constantly work on.
“(You also need to) revise your efforts, as well as get involved as much as you can in the community to be successful,” she said.
With that in mind, Hertel said Merrill’s recruiting efforts have changed over the years.
“Now it’s more of an active participation effort,” she said. “A lot of it is more of an organic process, too, where you form relationships. So when students do a tour and then remember us in two or three years when they graduate from high school. It’s about planting those seeds early and fostering them through their high school years.”
Hertel said it isn’t just a one-and-done approach.
“It’s perhaps several interactions over their middle and high school years,” she said.
Merrill Steel, Hertel said, does a lot of commercials and social media posts as part of its recruitment efforts.
Supporting refugees
In the last two years, Hertel said Merrill Steel has expanded its recruitment process to include the region’s local refugee population – specifically those from African and Congolese countries.
“We have a strong refugee population in our area,” she said. “We’ve become an employer-of-choice for them. In the last two years, we have begun making a conscious effort to recruit from that population.”
Hertel said the Ethiopian Community Development Council (ECDC), which is headquartered in Arlington, Virginia, has a branch office and multicultural community center in the Schofield area.
This refugee resettlement agency, she said, works closely with Merrill Steel regarding refugee hires.
“We had a lady from that organization come in and speak with us about the refugee population in this area, and we became interested in trying to help with putting people from this population to work,” she said. “We began working with her and have since gotten quite a population of refugees working here. There is still a significant number of refugees still looking for jobs in this area, according to ECDC, and it is a great population to pull from for employment.”
Strong workforce
As of early March, Merrill Steel had 504 employees, with more than half based in Schofield. During the remainder of 2024, Hertel said the company anticipates hiring another 20-30 people needed for its production departments.
For the most part, she said, no experience is required to be hired by Merrill Steel – with all necessary training provided by Merrill Steel.
“Certain things in the office require certain degrees, but if we’re talking strictly production jobs, we’ll train from the ground up,” she said. “We’d prefer to be the company to train them first because then we know they’re training in the way we do things.”
Hertel said another facet the company uses in recruiting is “we have amazing benefits,” including health insurance.
“We have an on-site clinic that is a huge attractor for new talent,” she said. “There are clinics at two of the three locations, and when the one in Iowa hits a certain number of employees, a clinic will also be added there.”
The production facilities are non-unionized, but Hertel said wages are evaluated quarterly to ensure Merrill Steel remains competitive.
“The ownership group here is like nothing I’ve ever encountered before,” she said. “They’re a humble and kind group of individuals who genuinely care about their employees.”