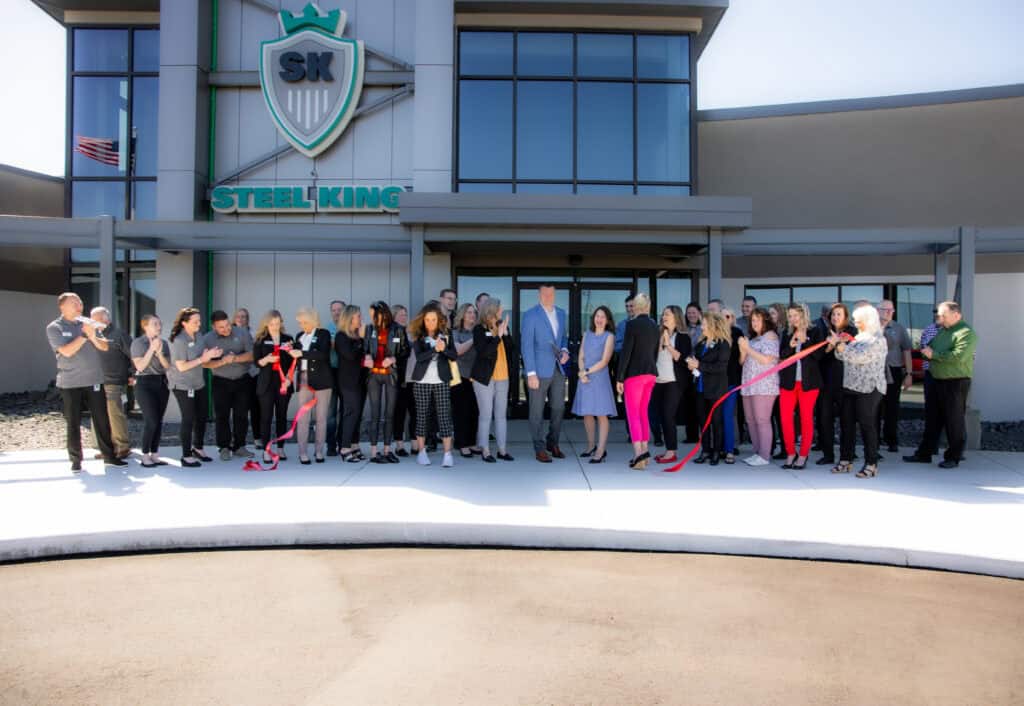
June 10, 2024
STEVENS POINT – There’s a good chance a consumer product you recently purchased sat on a storage rack made by Steel King Industries.
The 54-year-old Stevens Point company manufactures storage rack and material handling products found in large distribution centers across North America.
“Innovation and a focus on building strong customer relationships sets us apart from our competitors,” Steel King President Brian Pfannes said.
Steel King, Pfannes said, knows the importance of using quality materials and skilled labor to produce a superior product with structural integrity and pleasing aesthetics.
He said the company’s continued focus on supporting its growing workforce and client base prompted the construction of a new corporate headquarters.
The building at 5233 Coye Drive, Pfannes said, previously served as the headquarters for another area business but had sat vacant for several years.
Steel King’s newly remodeled 50,000-square-foot facility, he said, features a reception area, employee lounges, a communal dining area, team-working space, a client presentation area, dedicated office space for different departments, an engineering section, research and development space and an employee fitness center.
“The goal for this new headquarters was to create a facility that fostered collaboration, creativity and efficiency while increasing our presence and visibility in the greater Stevens Point area to attract the talent needed to propel Steel King forward for decades to come,” he said. “We were also running out of space at our former location.”
The company, he said, incorporated its pallet racking and material handling solutions into the building’s design.
“We wanted a high-tech facility our employees would enjoy being in and that our customers would come in and be amazed at what we do,” he said.
The marketing showcase area, Pfannes said, is a highlight of the new building.
The company’s products, he said, are displayed, allowing customers and dealers to look at Steel King’s different offerings and see how they work together.
Being able to visualize what a finished materials handling solution will look like when completed, Pfannes said, can be challenging.
Steel King’s Engineering and Design Department, he said, can – at an end user’s request – provide high-resolution 3D renderings that can show the completed install before the first bolt is turned.
The new headquarter’s marketing showcase space, Pfannes said, went from rendering to reality, and it’s hard to tell the difference.
A bit more about Steel King
Steel King was founded by Fred Anderson.
His son, Jay Anderson, served as company president from 2001 to the end of 2022 when Pfannes took over.
Before being named president, Pfannes said he served as vice president of supply chain.
The company employs more than 500 at its Stevens Point headquarters and manufacturing facilities in Stevens Point, New London and Rome, Georgia.
Steel King’s employees, Pfannes said, are the key to the company’s success.
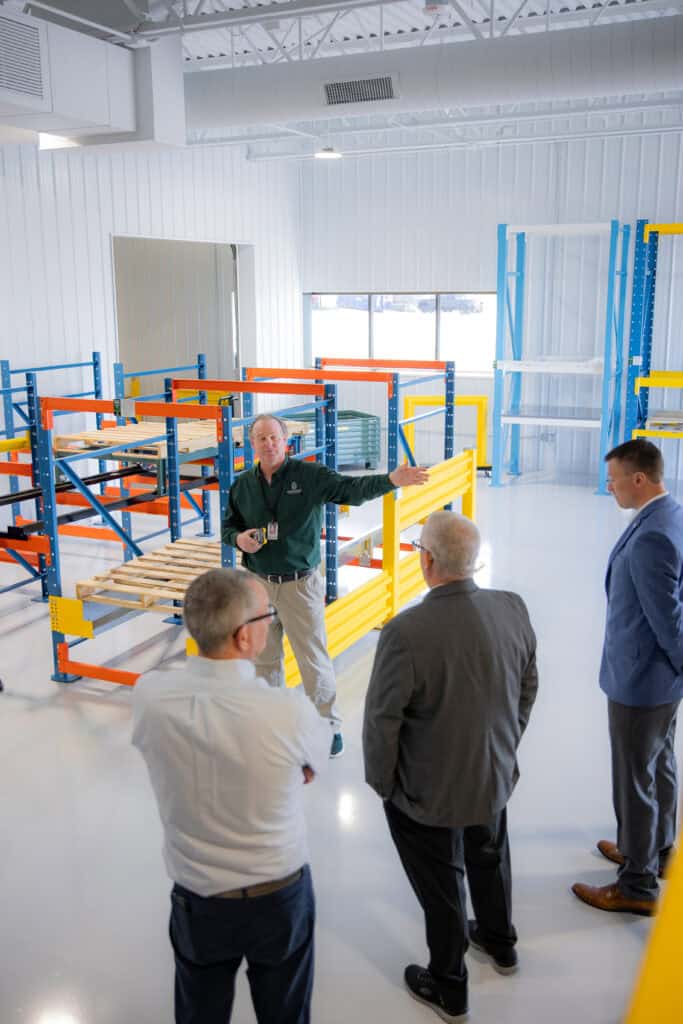
“We are people-centric,” he said. “Every person in our operation is essential and important to our success, and we want to make sure they know that.”
Pfannes said the company uses U.S. steel to make its material handling products, which include selective pallet racks, dynamic flow storage systems, cantilever racks, portable racks, custom shipping racks, industrial steel containers and guard railing.
Steel King products, he said, are shipped throughout North America.
“We have a wide base of customers,” he said. “We help about half of the Fortune 500 companies with their storage needs. When I look at where our products are going, it never ceases to amaze me.”
Pfannes said Steel King believes in leveraging innovation to help its customers solve their problems.
“We are focused on creating long-term relationships with our customers,” he said. “Providing them with excellent customer service is one way to do that.”
Sustainability
Pfannes said sustainability is integral to the organization as more products are manufactured in an environmentally sustainable manner, with practices that emphasize employee health and safety.
Initiatives, he said, extend from raw materials sourcing to manufacturing practices to facilities management.
Pfannes said many of the company’s existing practices – such as purchasing steel solely from North American sources and recycling all its scrap steel – have been in place for years and were inspired by best practices of its Fortune 500 supply base and other industry sources.
“We are leveraging our supply base and learning best practices from them, and we are visiting strategic suppliers to see first-hand how we can embrace new procedures that make economic sense,” he said. “We’ve learned a lot and already are doing things differently.”
Buying only U.S.-made steel, Pfannes said, assures Steel King of the quality of the metal’s composition and reduces the carbon footprint involved in transportation.
Steel King goes even further in that respect, he said, by sourcing materials from locations as close to its three plants as possible, which reduces the products’ overall carbon footprint.
Pfannes said Steel King purchases 90% of its steel from “mini-mills,” which strictly use recycled scrap in their manufacturing, thereby giving the material new life.
LED lighting, he said, was added in the company’s manufacturing facilities, which reduces energy use while creating a brighter – and safer – work environment.
Pfannes said the continued focus on sustainability was incorporated into the newly remodeled headquarters as well – including state-of-the-art energy-saving equipment and devices.
Steel King, he said, also reduced the number of paved parking spaces on site from 209 to 137 and transformed the former parking area into a low-maintenance, drought-resistant prairie.
That, Pfannes said, reduces maintenance costs and allows for filtration of parking lot runoff.
For more information on Steel King, visit steelking.com.