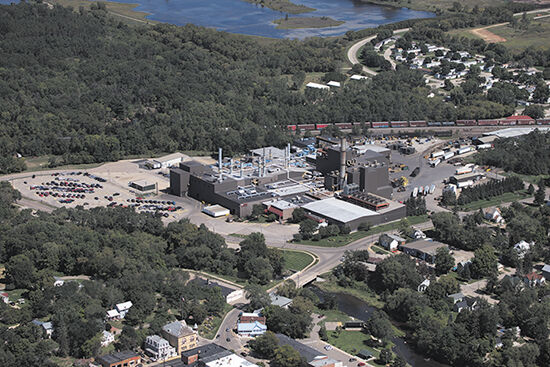
January 9, 2024
WAUPACA – For the second consecutive year, Waupaca Foundry was awarded the American Foundry Society’s (AFS) Green Foundry Award for its ongoing commitment to sustainable production processes and energy reduction.
It’s a recognition, Bryant Esch, corporate sustainability manager, said the foundry takes seriously.
“Several years ago, the AFS came up with this idea of a Green Foundry Award, which is meant to recognize those in the industry doing those sorts of things and moving the industry forward,” he said. “They have a regimented process for how submittals are brought in and have third-party judges who review these things. We’re honored to have it happen two years in a row where we’ve won the award.”
This year in particular, Esch said, the foundry was recognized for its sustainability report – “which oddly, and maybe a little disappointingly, is not common in the industry.”
“(In terms of) independent foundries – which are a large percentage of the foundries that are out there, and a lot of them tend to be smaller businesses – you don’t see anybody doing a corporate sustainable report in that market space,” he said.
It’s a report Esch said Waupaca Foundry started producing nearly a decade ago.
“We decided back in 2014… (after recognizing) there could even be neighbors near our properties or facilities who don’t even know what we do here – as far as they know we have monsters inside the walls,” he said. “So, we started working harder at sharing things that we’re working on and how the process works.”
The response the foundry received since, Esch said, has been nothing but positive.
“We’ve tried to put that information out into the public,” he said. “And that gave us the spirit of wanting to be more transparent and showing (the public the) things that are important to us. Here’s where we have the potential for our biggest impact on the world at large, and here’s what we’re doing about it and how we’re doing on our success.”
As one of the largest independent foundries in the world, Esch said he is not aware of another jobbing independent foundry – which are fully-equipped foundries that do not have their own individual casting business, but undertake contractual casting for other companies – that has issued a report yet.
And though the AFS’s Green Foundry Award is relatively new, Esch said Waupaca’s focus on sustainability has always been at the forefront of how the foundry does things.
“We were doing environmental things and sustainability practices before (we began releasing an annual report) – we just weren’t broadcasting it to the world,” he said. “That’s what changed in 2014.”
What’s the impact?
Esch said many people aren’t familiar with what a foundry does and are often presented with that question.
“The way I always sum it up, the easiest way to explain it, is we basically take scrap metal that other folks don’t want and turn it into something new,” he said. “A lot of people don’t realize that. Sometimes we get confused with steel mills and things of that nature. We’re not using ore or anything like that. We’re taking scrap metal, melting it down and pouring it into something new.”
In terms of sustainability, Esch said the process alone is a “great feather in our hat.”
“But ultimately, it matters how we run the rest of our business as far as how successful we are at being a green foundry or working toward that objective.”
Esch said he often describes Waupaca Foundry as four or five different factories all under one roof doing different things, yet working together to make the finished product.
Looking inward at itself, Esch said the foundry went through a self-evaluation process of all of those things and “the ins and outs of what is happening.”
“We have terms for this, but a simple example would be, most people drive a car at one point or another,” he said. “There are pros and cons environmentally to driving cars. When you have to purchase gasoline and consume it, the gasoline is something you put into your car and then the emissions are the impact of driving the car around. In a facility like ours, we have hundreds of ins and outs, so we looked at all those and scored them based on different attributes.”
Esch said there were four or five items that topped the list of having the biggest impact on the environment, with the highest impact coming from energy consumption.
“We’re bringing in scrap metal and we have to heat it to about 2700 degrees Fahrenheit,” he said. “The pure energy and physics you have to overcome to do that – that’s why we’re such a large energy user. We’ve identified that our consumption of energy is a big deal.”
And even if no direct emissions are happening at the foundry itself, Esch said because of the foundry’s electrical use, it will still be happening at the power plant elsewhere.
“We’ve put a lot of focus into energy, energy use reduction and carbon and all that fun stuff,” he said.
Historically, Esch said there have been a variety of things that have supported the foundry’s long-tenured focus on sustainable practices.
The first being location – with many of Waupaca’s facilities being located in smaller, rural communities.
“We had to be a good neighbor in those communities,” he said. “Because, when you’re working in a town of 6,000 people and everybody’s kids are going to school together, if you were not being a good neighbor to the community, you would hear about it right away. So, there was always that.”
Esch said over the years, Waupaca Foundry’s leadership has been proactive on these topics as well – “creating an environment where a lot of this made sense to (the employees).”
Relatively early on, because of its automotive work, Esch said the foundry was also pulled into quality management systems that began gaining traction in the late 1980s.
“For us, our history and quality made it easy to transfer or utilize things we’ve learned and put it toward the environmental side of things, and we went from there,” he said.
A changing landscape
In a time when companies across the globe are working on sustainability and energy efficiency goals of their own, Esch said many of their customers are requiring their suppliers to help them achieve them.
“It’s interesting because, let’s say we go back 10-15 years and somebody called your company and said, ‘Hey, I would like to know exactly how much electricity you use to make me one ton of iron,” he said. “The response back then might have been – and not just from Waupaca, but from any business – ‘well, that’s proprietary information, and we can’t share that.’”
Today, Esch said the landscape is much different.
“First of all, because we’re a jobbing foundry, we don’t just have just one customer or 10 customers – we have hundreds of customers,” he said. “And many of them vary in how mature they are in their environmental programs. But there’s a good percentage of them that are well along and have carbon targets – they expect to know exactly what’s going on environmentally for the production of their product. So, we’ve been getting prying questions for some years now, and it’s only cranking up as we go.”
Esch said Waupaca Foundry shared a great deal of information with its customers to help them with their sustainability programs.
“Of course, they have targets and things they want to meet, and we do what we can to help them meet their own goals,” he said. “And I will say, generally, when they come asking and then hear about the things we’re doing, I find they’re pleased with where we are (in terms of sustainability practices) – because it sounds like they don’t hear that everywhere in our industry, which again is unfortunate. That’s something we want to help push.”
The annual sustainability reports, Esch said, identify the ways the foundry impacts the environment, and the world at large – as well as objectives and targets of what the foundry is working on to address them.
In addition to the already mentioned focus on energy and carbon usage, Esch said beneficial reuse, which is basically the reuse of spent foundry byproducts, is also high on the importance list.
“One example of this is foundry sand,” he said. “We can use foundry sand over and over in-house about 30-35 times, which is good. But traditionally, the way of handling foundry sand was disposing it in a landfill. We’ve been working since the late ’80s to try to change that paradigm. We’ve reached the point now where approximately 80% of our spent foundry byproducts are reused for off-site projects.”
This practice, Esch said, contributes to lowering the need to mine more sand elsewhere.
Another big ticket item, he said, is the foundry’s water consumption.
“We’re at the point right now where we’ve reduced our water use by 72% from what it used to be,” he said. “We’re also proud that when you look at air pollution controls, EPA (the Environmental Protection Agency) keeps a list in each industry of who has the most state-of-the-art controls out there. And if you look under foundries and the different types of foundry equipment, you’ll see Waupaca Foundry’s name all over that list. That’s something we’re proud of, and we want to continue to be the industry trendsetter for that kind of stuff.”
Looking to the future, Esch – who is currently working on the 2022 sustainability report – said the foundry plans to continue releasing annual reports to update the community, the region and the industry on its sustainability advancements.
Esch said not only does the report highlight Waupaca’s targets and goals, but it also provides examples of how practices and procedures have been implemented, therefore, serving as a resource for other foundries and companies to follow suit.
“It solicits some interest from others in our industry and even some organizations outside the industry,” he said. “Nothing makes my day more than when I get a call from somebody and they’re like, ‘Hey, we saw you did a heat recovery project where you took waste heat and used it to heat your building in the winter – how does that technology work? What did you do?’ We’re happy to share that information. We’ve had dozens of times where we’ve helped others push for their projects, and that’s cool. I get a kick out of that.”
A full copy of Waupaca Foundry’s 2021 sustainability report is available at waupacafoundry.com.
The 2022 report will be released and available to the public soon.