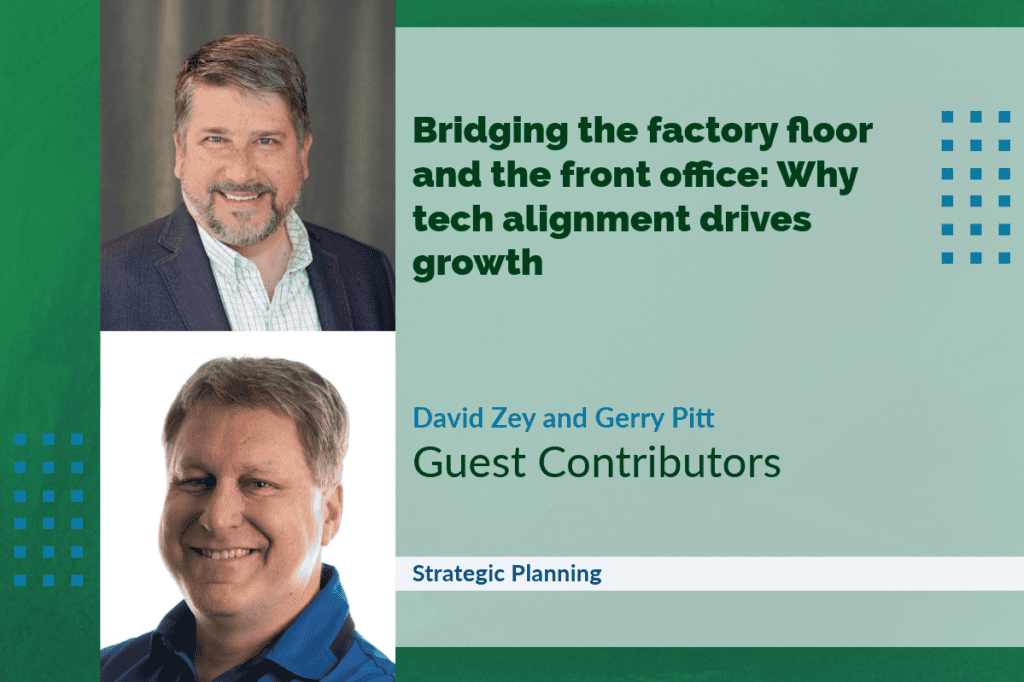
April 7, 2025
For decades, manufacturing operations have quietly maintained a divide between the plant floor and the front office.
It wasn’t necessarily intentional, just a reflection of the different priorities and pressures these sides of the business face.
The plant floor has long been focused on safety, uptime and the consistent execution of processes.
Meanwhile, the front office is focused on efficiency, productivity and, ultimately, profitability. These two worlds have operated in parallel – aligned in purpose but often siloed in execution.
Technology has served both sides, but historically in very different ways.
On the plant floor, investments in operational technology (OT) – things like programmable logic controllers (PLCs), SCADA systems and human-machine interfaces (HMIs) – have kept production moving reliably and safely.
In the front office, the rise of information technology (IT) has introduced software platforms, such as ERPs and CRMs, automation tools and business intelligence dashboards, that help decision-makers optimize growth and manage performance.
Though most businesses may not consciously separate their challenges into “IT” or “OT” categories, technology providers often do.
The distinction is baked into how products are developed, marketed and sold.
What’s interesting is these efforts, though targeted at different parts of the organization, often overlapped in intention.
Both sides were looking to lift performance, reduce waste and create a competitive advantage.
But they were often marketed to entirely different audiences, sometimes even within the same company.
Though IT vendors might pitch solutions to CFOs or CIOs, OT providers were often working with plant managers or operations leads with a direct line to the CEO.
These competing channels made it easy for parallel strategies to emerge, duplicating capabilities and even conflicting in execution.
Now, as Industry 4.0 technologies bring together IoT, data analytics, cloud computing and AI, the line between IT and OT is blurring.
For many Wisconsin businesses, especially those rooted in manufacturing, this convergence offers a chance to modernize and strengthen operations.
But it also introduces real organizational tension.
The core issue isn’t just technical – it’s cultural.
OT and IT evolved with entirely different mindsets.
One values real-time, deterministic control with high reliability and minimal change.
The other thrives on agility, fast iterations and rapid innovation.
When these two worlds are brought together without a clear plan, it can result in confusion over policies, disagreement on security protocols and uncertainty about who owns the data.
In some companies, this leads to gridlock.
In others, it’s a quiet tug-of-war that erodes trust across departments.
It’s a bit like the difference between the U.K. and the U.S. – both speak English, but the words often mean different things.
A “controller” in an IT department might be a software component that governs a web application.
In OT, it’s a physical device mounted in an enclosure that ensures machinery doesn’t overheat.
In both domains, people speak confidently about automation, systems and monitoring, but the definitions and tools are often worlds apart.
First comes understanding
So, what does this mean for leadership in Wisconsin businesses?
First, it’s important to understand where your company currently leans.
Are you an OT-first or an IT-first organization when executing solutions?
This might not be a formal designation, but the composition of your leadership team and who holds influence over strategic technology spending will often indicate which direction you default to.
A company where operations drive the agenda might prioritize investments in plant floor stability and controls.
In contrast, a business steered more heavily by finance or marketing might lean into data platforms, software integrations or cloud-based tools.
Neither approach is wrong, but they come with different strengths and blind spots.
An OT-first mindset might be slow to adopt new digital platforms but will have deep expertise in reliability and throughput.
An IT-first company might deploy the latest software tools with ease but overlook challenges that arise when those tools interact with aging machinery or legacy systems.
Understanding your lean and how your competitors are leveraging theirs is essential.
Some companies are competing on plant-floor precision and output consistency.
Others are winning through agility, leveraging real-time data to make faster decisions.
In today’s environment, the most successful businesses will be those that can unify both capabilities, delivering reliable operations that are also responsive and data-driven.
That means taking a hard look at how your teams and systems are structured.
If IT and OT are still treated as separate islands, it’s time to think about integration.
Multiple tools may serve similar purposes, or policies developed in isolation can create unintended complexity.
By identifying these overlaps and gently aligning your approach, you can reduce friction and build a more agile, responsive foundation for innovation.
Centralizing your view of ROI across both domains is a powerful way to reduce waste and improve collaboration.
This doesn’t mean consolidating everything under one team, but it does mean establishing shared goals and creating mechanisms for OT and IT to work together – especially when evaluating new vendors or technologies.
Process improvement, automation and even AI should no longer be treated as projects that live exclusively in one department.
They’re business-wide initiatives, and their real power comes when they operate across boundaries.
For instance, using machine learning to predict equipment failure has clear value on the plant floor, but it also affects procurement planning, customer delivery timelines and even staffing models.
When these improvements are scoped and evaluated only within one silo, their impact is limited.
As companies navigate this new territory, choosing the right partners becomes critical.
Many vendors still operate within their comfort zones.
OT providers may have limited knowledge or experience with cybersecurity or modern integration frameworks, while IT vendors may lack awareness of how critical latency or uptime is to the plant floor.
Look for solution providers that understand both sides of the equation or at least know how to work across disciplines.
Your ideal partner may not be one vendor, but a small ecosystem of collaborators who can bring deep expertise and shared vision to the table.
In Wisconsin, where manufacturing continues to be a backbone of the economy, this conversation is more than theoretical.
The choices companies make about how they bridge OT and IT may shape their competitiveness in the years ahead.
Those who treat technology integration as a strategic, organization-wide priority will be better positioned to adapt, innovate and grow, while those who let the divide persist may find themselves outpaced.
The future of manufacturing isn’t just smarter machines or better dashboards.
It’s about building organizations where people can work together, with clarity, trust and shared purpose – from the plant floor to the boardroom.
It’s about connecting digital investments to real-world outcomes and aligning technology with the goals that matter, no matter where in the company those goals begin.
And it starts with a willingness to speak each other’s language.