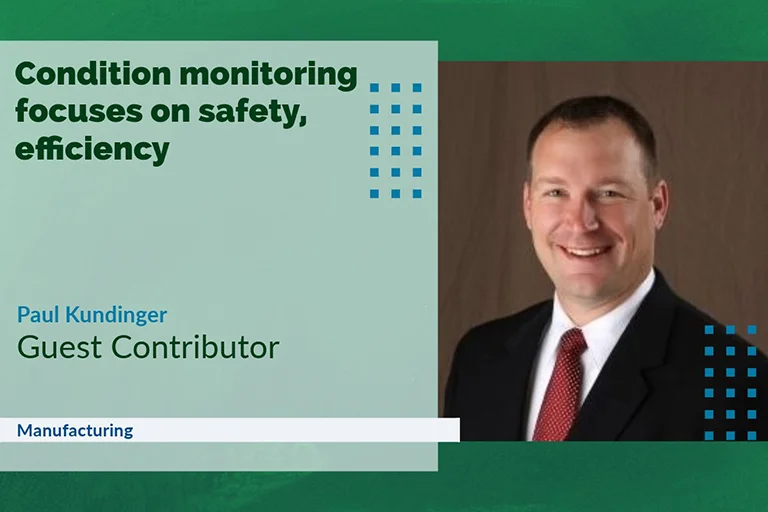
September 5, 2023
The world of manufacturing is becoming increasingly complex, with machines and equipment evolving to keep up with technology.
As a result, proper maintenance is more critical than ever before.
That’s where condition monitoring comes in.
By keeping a close eye on the health of machines and detecting subtle changes that may indicate a developing problem, maintenance teams can perform predictive maintenance instead of waiting until a machine breaks down.
This approach can reduce downtime, save on repair costs and even extend the life of the equipment.
Effective condition monitoring collects data on components, such as the temperature, vibration and pressure that can help determine a machine’s overall health.
Maintenance teams can analyze the data to detect issues earlier to prevent dangerous or destructive equipment failures.
It is a proactive approach to maintenance, which can lend itself to longer-lasting and more reliable machines.
When looking at condition monitoring technology, some of the most common tools include sensing technologies designed to detect and alert operators to hazardous gas, refrigerant leaks and various level, pressure, temperature and flow variations.
Each tool provides unique insights into a machine’s health that can be used separately, as well as together to provide a more comprehensive understanding of the machine, leading to a more effective maintenance strategy.
When investing in condition monitoring equipment, it’s also important to consider remote monitoring opportunities.
Remote condition monitoring can be a useful tool when machines are difficult to access or hazardous to employees.
It also ensures maintenance staff can continually monitor no matter where they are.
Through sensors and software, real-time data on the machine’s health is available and everyday devices and systems can be adjusted or remotely turned off.
Often, multiple sites can be linked together, meaning a single maintenance technician can view and review the data from many facilities at once without being on-site.
These remote capabilities help to keep the safety of equipment and employees top of mind and also, ultimately, save time and money by reducing travel and inspection times.
Condition monitoring also helps identify areas of potential improvement and efficiencies in your plant.
With constant, real-time data being tracked and reported, you have a trove of information to help you make the next-level decision about improvements in your process or technology.
The drawback is it can seem overwhelming to get started.
From understanding what technology is best to implement, how to train staff to optimize the technology and what to do with the data – there are a lot of pieces to consider.
Partnering with an expert in condition monitoring technology can help you on the road to efficiency.
As technology continues to progress, we can expect to see even more sophisticated condition-monitoring solutions in the future.
However, it’s worth noting that while these tools are undoubtedly valuable, they should not replace human oversight entirely.
It’s the combination of human expertise and innovative technologies that will enable companies to achieve optimal safety, efficiency and operational excellence.