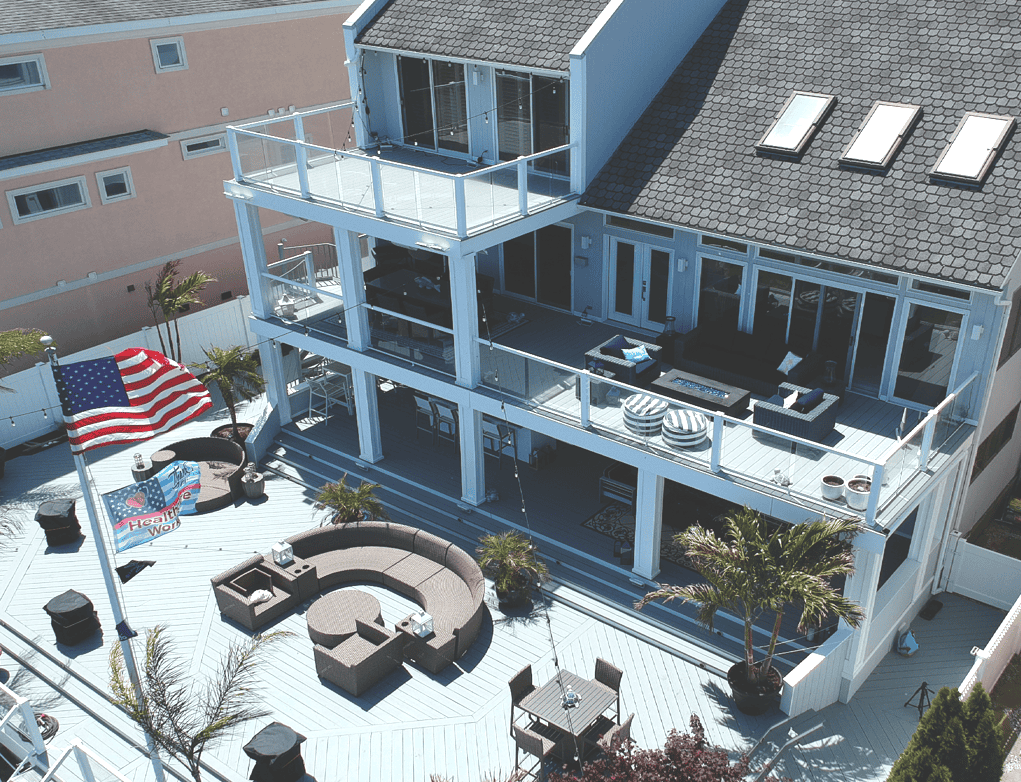
August 26, 2024
GREEN BAY – To help expand its distribution reach and increase sales and customer service across North America, Green-Bay-based DuxxBak Composite Decking recently announced a partnership with AmeriLux International, a distributor of building materials.
Eddie Holzem, vice president of sales and marketing, said DuxxBak – known for its DuxxBak Dekk, a water-shedding design comprised of durable composite materials – began working with AmeriLux earlier this month.
“We believe AmeriLux International is the ideal partner to help us expand our market presence through its distribution network,” Holzem said. “Its commitment to excellence and customer satisfaction aligns perfectly with our values, making this collaboration a win-win for both companies and our customers.”
Matt Balzola, vice president of sales for AmeriLux, said the company is excited to partner with DuxxBak as its master distributor.
“This collaboration allows us to offer our customers a premium decking solution that enhances outdoor spaces and provides superior performance and longevity,” he said.
Holzem said though DuxxBak manufactures the decking material at its Green Bay plant (1518 S. Broadway) it doesn’t build the decks – “that’s left to area decking companies.”
More on the partnership
Before the partnership with AmeriLux, Holzem said DuxxBak “really never had a sales staff.”
“Going back about six years or so, we’d sell through our own distribution avenues, contractors and DIYers (do-it-yourself),” he said. “I’d say organically, we had some marketing and sales efforts, but it wasn’t a huge part of what we did.”
AmeriLux’s success in customer service and the sales side of its business, Holzem said, made partnering with them a good idea.
“They sell other construction products into distribution, so our main relationship with them is all about sales and customer service,” he said.
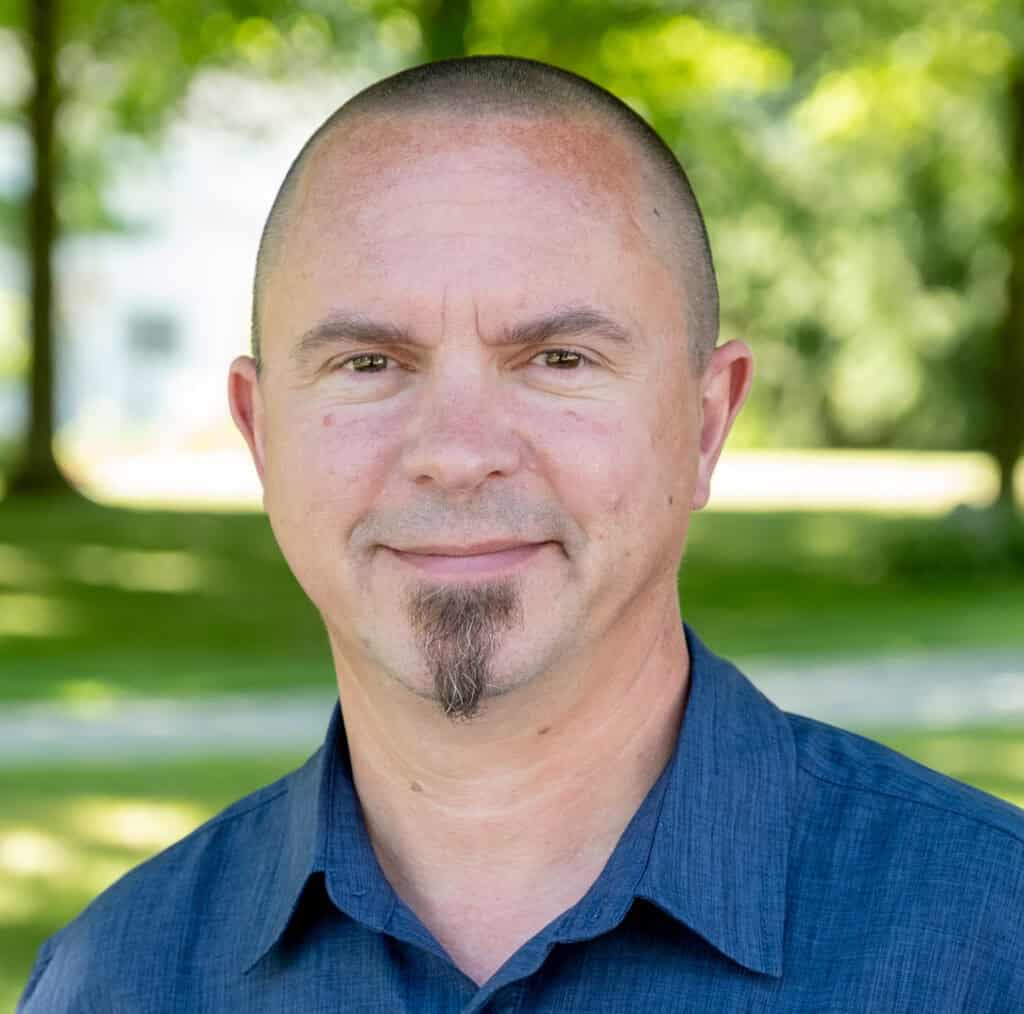
Holzem said he joined DuxxBak this past spring “to help in its future growth” – something the partnership with AmeriLux can help with.
“The one thing that attracted me (to the job) was DuxxBak’s audacious goal for growth,” he said. “I like challenges, and even with a partner like AmeriLux as the driving engine of our sales, my particular responsibilities revolved around branding.”
A big task for a small company in a large industry.
“That’s the attraction AmeriLux brought to the partnership – they also see the growth potential,” he said.
Even before AmeriLux came on board, Holzem said DuxxBak distributed all over the country, as well as in parts of Canada.
“We have been selling in Canada for quite a few years,” he said. “We are currently working on a potential distributor in Japan. I think AmeriLux will help us expand the distribution network, which is why they’re on board.”
A leader in the industry
Entering the market 24 years ago, Holzem said DuxxBak’s decking is known for its unique water-shedding properties – which divert water away from the deck surface, creating a dry space beneath the deck suitable for additional outdoor living or storage.
“The uniqueness of our product isn’t necessarily the composite itself, though our composite has some unique characteristics,” he said. “What makes our composite unique is that most composite deck boards are made of wood fiber. I say most because not all are made with a combination of wood fiber.”
Because Northeast Wisconsin is a known leader in the manufacturing of paper products, Holzem said DuxxBak came up with a solution to use that to its advantage.
“We have replaced that wood fiber with the leftover waste product from the manufacturing of paper products,” he said. “That waste product essentially gets sold to us to use in our decking.”
Conveniently, Holzem said Georgia Pacific is right across the street from them.
“Its waste product becomes an additive for us, which ultimately ends up being pure minerals that replace the common wood fiber,” he said. “The wood fiber in normal composite decks absorbs a lot of water, so the minerals in the paper waste make our product resistant to absorbing water. It’s also much stronger.”
Though Holzem said there’s more to DuxxBak decking than just paper waste.
“We also add virgin plastic,” he said. “Virgin plastic creates a stable product versus using recycled plastics. There is decking material out there using some recycled plastics, but we have found that when you introduce that, it creates instability of the product – it’s not as superior, and quite frankly, the cost is virtually the same.”
One of the last ingredients of the decking material, Holzem said, is “unique.”
“We also use rice hulls,” he said. “We encourage people to keep drinking beer so we can take those leftover rice hulls and use them for our product. In most cases, the hulls just get discarded anyway, but we’re able to reuse that in our product – it creates a binder.”
Holzem said all those materials add up to a durable product.
“When you compare our decking to natural cedar, which has a long life span when it comes to wood, there’s no comparison,” he said. “A lot of older decks are put together with treated lumber, which over time, even that treated material weeps out of the board and then creates a wavy board with the potential for splinters.”
Holzem said it’s about longevity and eliminating the need for a lot of maintenance.
“Maintenance for most of us who have ever lived with a wood deck means staining it every two years,” he said.
Holzem said similar to a house window, there might be a little maintenance on DuxxBak’s decking.
“We don’t think of windows as needing maintenance, but I would call the cleaning of a window as maintenance,” he said. “That’s similar to what our decking material needs.”
The cost of composite decking materials might be more upfront, Holzem said, but it more than makes up for that in the long run.
Operations
Currently just shy of 50 employees, Holzem said DuxxBak’s partnership with AmeriLux will inevitably lead to the hiring of more workers.
“We’re still a small business, but our plant is pretty automated,” he said. “A few of our lines run 24/7, but we’re efficient, and it doesn’t take a lot of staff members to run it. Having said that, we know at some point in the future, we will need not only additional staff members but probably additional capacity.”
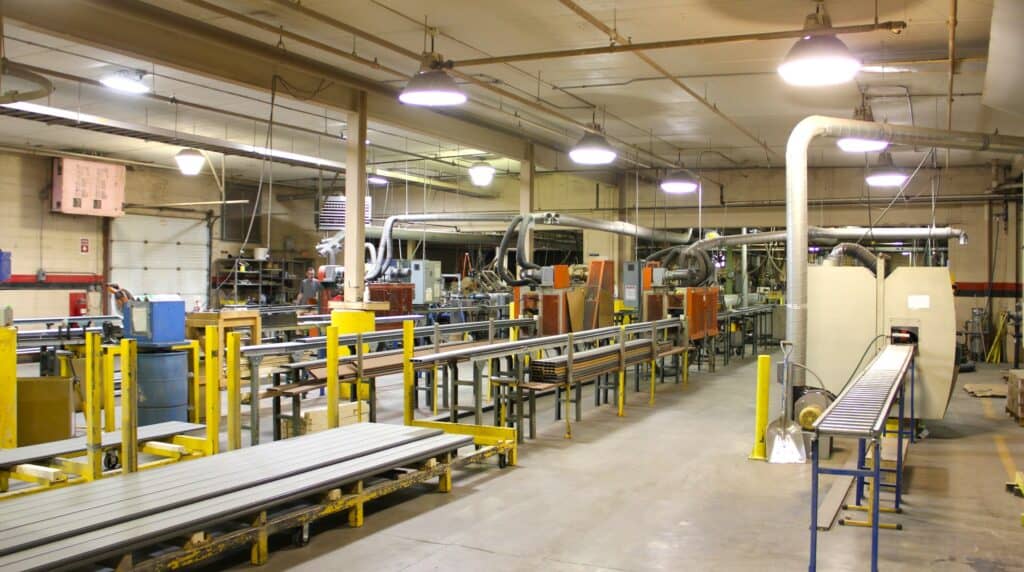
DuxxBak, Holzem said, will likely need to expand its lines in the future.
“We currently have nine lines available to run our product, but we have a lot of capacity left within our current operations,” he said. “It just depends on how quickly we grow.”
The future of composite decking
Holzem said the future of composite decking will continue to evolve.
“Right now, for instance, the key that a lot of the manufacturers are focusing on is the heat of the deck board,” he said. “When it’s installed and people are walking on it with bare feet, it can get hot.”
With that in mind, Holzem said there are efforts happening right now to incorporate cool technology.
“Like any product, competitive manufacturers like us are going to try to come out with innovation,” he said.
Holzem said DuxxBak has experimented with other decking ingredients as well.
“We’ve experimented with siding and roofing material,” he said. “It’s not our focus right now, but we do see that as part of our growth as a company.”
One pathway forward, Holzem said, is to develop other products.
“We’ve learned over the last how many years, that just when you think you’ve got things figured out, something better comes out – you have to adjust,” he said.