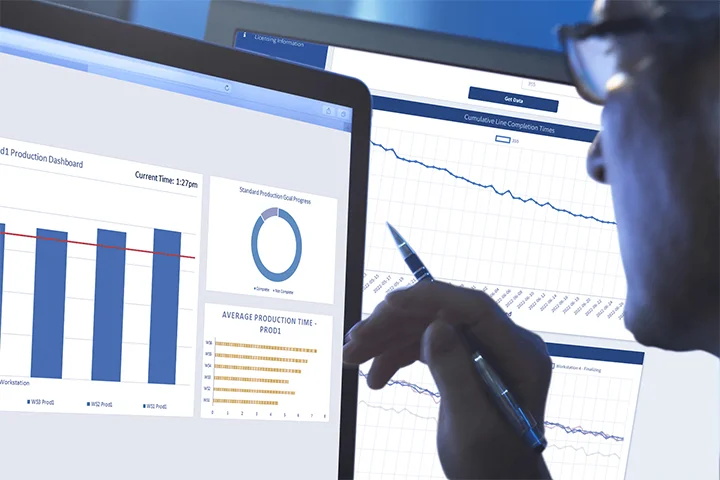
January 12, 2023
APPLETON – Huzzard Data Systems Founder Gary Jahnke said since the company’s beginning more than a decade ago, it has been focused on helping its clients improve their processes for better results.
The same can be said about its most recent offering – cloud-based digital work instruction software, which Jahnke said aims to transform assembly line work and improve quality control.
“This software changes the game for manufacturing performance,” he said.
Process-focused company
Based in Appleton, Huzzard is a process improvement company that utilizes barcode technology to improve workflow.
Jahnke, who started the company in 2010, said his 30 years of experience in labeling systems and barcode technologies served him well in launching the company.
“Most people probably don’t think much about going to the grocery store or the gym and having their information scanned in,” he said. “I have a lot of experience in the manufacturing sector, so everything we do adds value. We help people and companies present data, collect data and then help manage that data.”
Jahnke said efficient barcode technology is more a part of the average person’s life than they may think, including in one’s wallet or purse.
“It’s on the back of your driver’s license, too,” he said. “There’s a lot of data there – your name, date of birth, address and driver’s license number. Here’s the magic – for a policeman, instead of typing all this stuff in at 2 a.m. when you’ve got someone in the backseat, if they have their driver’s license, the policeman can simply scan the license with one of our scanners. Our scanners read that barcode and decode the information into a program we designed. Before this, the process was manual and not as safe. (Efficient barcode technology) is more efficient, more accurate and can save money.”
Setting itself apart
Jahnke said in an effort to differentiate Huzzard while helping its clients, the company recently released Info on Demand Digital Work Instructions.
“This provides assembly line employees with digitalized guidance to correctly perform work duties,” he said. “It helps guide employees through their production processes, offering helpful information while helping them avoid misguided steps.”
Like barcode technology, Jahnke said this new software will save companies time, cut costs, reduce rework and help them communicate more effectively.
“Instead of just using (their) knowledge where they don’t know for sure, project supervisors and engineers can now have a sense of using real data,” he said. “If you have 10 workstations online saying, ‘I think station three needs help today,’ you can see that in the data. Why is it taking this person longer to complete the task than another person? Is it a lack of training or is there something mechanically wrong at the station? The real-time data can be shared on display monitors on the factory floor, traditional PCs and mobile devices.”
Jahnke said the technology also holds employees accountable.
“Supervisors can ask meaningful questions and get meaningful information,” he said. “We make the software and then the employers can use it how they see fit.”
Jahnke said manufacturers can easily upload existing documents to be converted for digital display.
“By eliminating the need for hard-copy procedures, cloud-based Info on Demand Digital Work Instructions empower employees to have information at their fingertips – not in hard-to-reach binders away from their workstations,” he said.
Because the display is shown directly at the assembly line station, Jahnke said this software can also help expedite training for new workers and avoid assembly line stoppage.
Huzzard Data Systems Founder Gary Jahnke said Huzzard, based in Appleton, is a process improvement company that utilizes barcode technology to improve workflow. Submitted Photo
“Throughout production, employees can quickly suggest updates to the work instructions and supervisors can approve updates and revisions that are then reflected on digital displays for all employees – ensuring accuracy on a daily basis,” he said.
Jahnke said because the workforce is changing – older workers retiring and newer, younger ones coming in – it’s also good to update technology.
“One (particular) company, there are a lot of new people in the marketplace,” he said. “They had people there for almost 40 years who have exited. The newer workers are okay with a more modern assembly line, such as a touchscreen. It’s like the hardcopy paper versus looking at your Kindle – it helps modernize their process.”
Jahnke said the real-time data can be shared on a variety of form factors including display monitors on the factory floor and traditional PCs and mobile devices.
The technology, Jahnke said, is also good for workers interchanging jobs on the assembly line or to refresh them after a significant time away from that operation.
“This comes up in terms of training,” he said. “When someone signs on in the morning, if they know they’re going to do a certain thing but haven’t been there for six weeks, the employee can get a refresher – an overview of how to do it again. It will save errors in the long run.”
Jahnke said steps are presented to employees in easy-to-understand, interactive formats that can include audio and video enhancements.
He said the software can also easily translate text to Hmong or Spanish language versions.
More than digital instructions
Though it’s part of the offerings, the technology, Jahnke said, is “much more than a digital copy of the work instructions.”
“That was not our initial intent,” he said. “It started there – it’s a big part of it – but it’s all these other little things we offer.”
?Using an iceberg as an analogy, Jahnke said “for every dollar you spend on something, there’s $20 spent trying to fix the problem or on time wasted.”
“If you think about an iceberg, everybody sees the problem – the tip of the iceberg, but they don’t see all the stuff under the water,” he said. “That’s what we dig into. People say, ‘measure twice, cut once.’ We’re big proponents of investing time upfront to save time on the backend.”
According to Huzzard’s website, Huzzard.com, some of the company’s clients include Americas Styrenics, Dynegy, Miller, Meister, Planet Fitness, Rawlings, Tennessee State Trooper Highway Patrol and the University of Wisconsin-Madison.