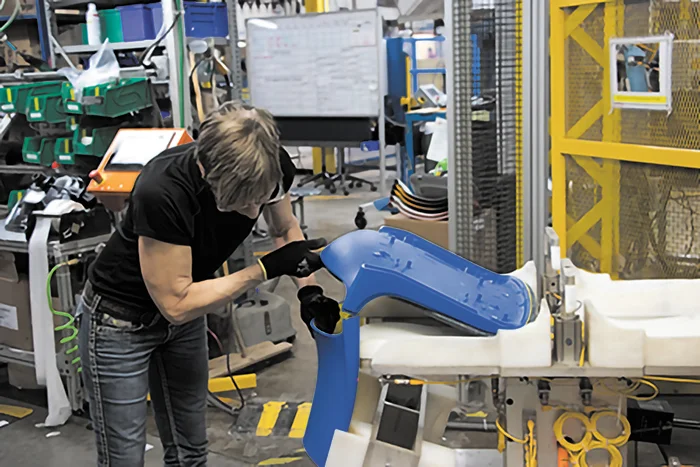
October 19, 2023
GREEN BAY – From chairs to tables and architectural walls to workspace systems – Green Bay-headquartered KI is well known in the office furniture industry worldwide.
What may not be as well known is the Northeast Wisconsin manufacturer adds an additional 150 employees during the summer to keep up with demand.
“(Summer) is when the colleges, universities and K-12 (institutions) want their furniture – when the kids aren’t there,” John Kersten, operations manager at KI, said.
Kersten said the manufacturing company – which recently showcased the work it does to members of the community as part of the Greater Green Bay Chamber’s “Celebrating Manufacturing Month” tours – sees a 400% increase in the summer, stemming mainly from educational institutions’ orders.
“In January, we may ship $8 million out of this plant,” he said. “In August, we may ship $32 million… that’s all the K-12 and college and university market, and (we serve) those two markets with the products we have here in Green Bay.”
The heavy influx in orders during the summer months, Kersten said, has been constant throughout the last 30 years of business.
“We are so linked to those markets,” he said. “We’ve gotten good at it. We do infrastructure and inventory build in the spring to get ready for (the busy season).”
Boosting up the team
With such a large increase in orders and revenue each summer, Stuart Kolb, general manager at KI, said “we can’t do it all” with the company’s year-round workforce numbers.
To make the summer months and influx of orders go as smoothly as possible, he said KI hires 150 seasonal employees in addition to the nearly 310 employees on staff year round.
A majority of those hires, Kolb said, are high school and college students.
“We’re (hiring) as young as 17 years old,” he said. “We get seniors in high school we’ll recruit… and (we) have job fairs right at local high schools. We have regular job-fair type things, along with community-sponsored job fairs – KI will be represented.”
Of the 150 employees hired annually, Kolb said about 35-40% of seasonal employees return each year.
Kersten said a lot of family members of year-round employees come to work at KI in the summer as well.
“A lot of our own sons and daughters and nieces and nephews (will come work for us),” he said.
During the summer, Kolb said there are 18 shifts in a week – three shifts a day on a five-day work week, and three shifts on a Saturday or Sunday.
“It’s pretty much 18 shifts to get the numbers we’ve been getting the last couple of summers,” he said.
Because many students tend to leave toward the end of August, when KI is still in its busy season, Kolb said the company incentivizes those who stay.
“If the summer workforce stays with us through the fourth Saturday in August, we give them an extra dollar an hour they work through the summer,” he said. “A lot of times, that can be an extra $1,500. That helps us get the big shipments of August over the finish line.”
In the instance that KI does not have adequate staffing to complete all the summer orders, Kolb said some employees in the corporate office will come to help.
“There are qualified folks in this office who can handle it and they don’t mind helping,” he said. “We thank them (for all their help).”
Staying ahead of the game
Though everything is made to order in the warehouse, to help keep up with the demand in the summer, Kolb said preparation starts early.
“One of the tools we’ve used forever (to stay on track) is building summer stock of some prefabricated frame styles, and they’re either painted black or chrome plated,” he said. “It’s a major component of the chair. In an inventory build in one of our warehouses, we’ll stock thousands of frames at that component-part level.”
Then, when the orders come in, Kolb said the backstock of chairs will be painted the correct colors and customized to the customer’s needs.
“We do that with probably up to $2.5 million to $3 million dollars’ worth of component part value we know is generic enough in its raw state,” he said.
And, in most cases, Kersten said most customers put their orders in well enough in advance, which also helps with the process.
“We have customers who put in orders a year in advance,” he said. “And we know that spec isn’t going to change. We’ll go back to them and say ‘hey, we’d like to make your order, or a portion of your order or line of your order in advance.’ So it’s still made to order. We just may choose to make it now when there is capacity.”
Kolb said it is “kind of an industry phenomenon.”
“Sometimes the reps or the school districts, they’ll recognize there’s value to having that order built (in advance),” he said. “So, they know they’re going to get it on time for when their school starts in July or August. I’ve heard some of our reps use our ability to do that and store it for free…. And you’ll know you’re going to get it – so they help us with that. Bring your order and lock the specs down so we can build it and get guaranteed delivery when you need it in July and August. It’s like free warehousing.”
Lead times
Normal lead times, Kersten said, tend to be anywhere from three to four weeks.
Though the goal during the summer is to keep the lead times the same, he said they can become a bit “dynamic.”
“You may have supplied parts that are constraints,” he said. “It’ll be limited, but I may have to extend the lead time on three different products. And then as soon as we get the first parts in for that, I can drop that lead time back down.”
Kolb said the team never wants to go beyond a five-week lead time during the busy season.
With the addition of robots, the process of making chairs and other furniture at KI has become more efficient. Photo Courtesy of KI
He said they can also vary depending on what each order entails.
“Thirty percent of what we do is non-standard, we’ll call it modified product,” Kersten said. “It may be simple, something as simple as color. It may be something difficult. We have a 1,500-chair order going to New York this month, which is two chairs combined – so that would have a little longer lead time because we need to build some tooling to be able to weld that up.”
To put the 400% increase KI sees into perspective, Kolb said one high-volume, K-12 classroom chair will be made 203,000 times between June through August.
Though, Kersten said KI tends to focus more on labor hours and shipping dollars during the summer instead of the number of chairs made.
“(For example, if we have) a custom modified product, I might make one chair, but that chair took triple the time to make as opposed to just a standard offering,” he said. “So, it’s hard to do apples to apples.”
Advancements in automation
Though the addition of robots and other automated machines throughout the years has helped with the efficiency and speed of building chairs, Kersten said it’s important to note they’re not taking from people’s jobs.
“We still need people to program those robots,” he said. “We still need people to feed the robots and then unload the robots.”
The addition of robots helps develop takt times – the rate in which you need to complete a product in order to meet the demand.
“So, you’re loading the robot, the robot’s doing its work and you’re doing other work at the same time the robot’s working,” Kersten said. “You’re able to be more efficient with that robot doing high volume, maybe low complexity work – but I need a human to see color, to load, to expect, to do those types of things.”
Kolb said adapting to the use of automation was necessary to keep up with the manufacturing industry.
“We had to automate to reduce the labor cost and keep it domestic, keep it in the U.S.,” he said.
Kersten said the addition of robots to the manufacturing floor also keeps KI’s employees safer and healthier.
“An employee that’s got 30 years of tenure is going to be much healthier than they were 30 years ago,” he said. “The ergonomic tools that are available, the automation that takes away the high volume, repetitive things that need to be done. And just the safety features – the electronic eyes that don’t allow you to get in trouble, that keep you away from that machinery… Everybody’s standing on a cushion mat. And inline drivers… Tool balancers, so you can let go of the tool instead of a drill you have to aim at a holster.”
A safer environment, Kolb said, also means fewer medical expenses that fall on the company.
KI also has onsite nurses on staff, and Kersten said not just for work injuries.
“If you cut too much wood this last weekend and you strained our elbow, you can go in there and a nurse will help get you through the next two weeks and get you healthy again,” he said.
Looking at the future
Though there have been great strides in automation, Kolb said KI is looking at more customized automation for the manufacturing plant in the future – such as KI’s plastics.
“What you see a lot of in the plant is off-the-shelf automation with robotic welder-type things,” he said. “Not everything can be automated, but we’re certainly looking to uncover wherever there’s repetitive labor we could make automated.”
Kolb said KI is also looking at how to make the handling of finished goods more efficient.
“As we look for further expansions in this facility, we’re going to be looking at more material handling automation, maybe some automated guided vehicles and how we handle the finished goods because that’s a next component of it,” he said. “(There are) some big boxes we’re moving around with forklifts, and it’s a lot of indirect labor.”
To learn more about KI, visit KI.com.