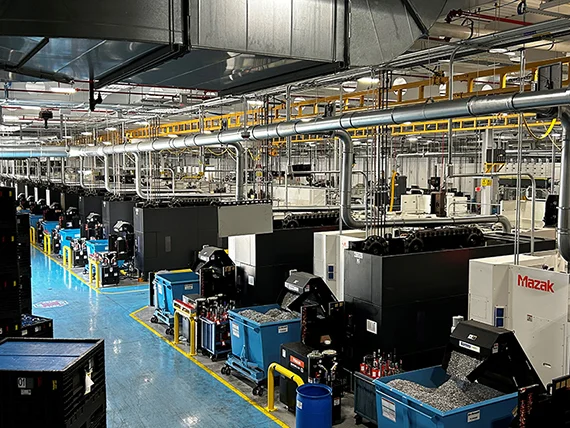
September 19, 2023
FOND DU LAC – With an eye to the future while learning from the past, Mercury Marine’s Gears and Shaft Systems Plant 4 manufacturing facility in Fond du Lac recently celebrated a milestone accomplishment – one million work hours without a lost-time injury.
It’s an accomplishment, Jim Sutton, director of safety and occupational health at Mercury, said hasn’t come without a “lot of work.”
“Safety is something you’re always thinking about,” he said. “When I came to Mercury, safety was something that was recognized and important – no one would say safety isn’t important – but I think it was more something the safety department might have dealt with. Some activities in the plant might have supported (safety), but not as many as today.”
Sutton, who has been with Mercury – a manufacturer of outboard, inboard and electric propulsion engines – since 2006, said the transformation in safety from his earlier days through now has been two-fold.
“After I had been here a while, we started identifying projects that would have an impact on the reduction of risks that were inherent to the business,” he said. “I would say the investment for Mercury (in being safer) started around 2010 – we put an investment toward equipment and operations, which improved the work environment.”
Sutton said advancements were made in improved lighting, better ventilation, improved machine safety and equipment and advanced safety procedures.
“We also gained a better understanding of what the physical demands of the work were,” he said. “Some tasks can be more demanding than others. It led us to think about how some of those physically demanding jobs could be automated.”
Sutton said you can’t always see the progression in safety when you’re right in the thick of it, but looking back, “it’s very obvious.”
“When I look at pictures or information from years past compared to what it is today, you can see the difference,” he said. “Even with me personally, when I first came to Mercury, I worked in our aluminum die-cast foundry. There were a lot of manual operations where we would hold a larger casted part to a buffing wheel – that was a physically demanding job. That’s the type of work we’ve been able to automate.”
Jim Sutton
Sutton said automation hasn’t changed Mercury’s employee base – it’s helped.
“It’s the opposite – our employment numbers have continued to increase because of our growth in the business,” he said. “It’s offered a safer environment for our people and allowed the business to grow.”
Sutton said Mercury may have looked at it from a safety aspect at first, but has since recognized many other benefits as well.
“Our employees can simply focus on the job they’re doing,” he said.
In layman’s terms, Sutton said automation has made Mercury more efficient and allowed it to take on more work, which equals more employees – all while making the work environment safer.
The milestone
Depending on the number of employees a company has, that can mean a different length of time to achieve one million zero-lost work hours.
For Mercury’s Plant 4, Sutton said that equates to about a year and a half worth of work.
“It depends on the plant population,” he said. “More than ever, people are interested in what the safety focus is and sustainability – these issues are important. Being able to stand in front of a new hire or in orientation and talk about what we’ve done, that’s a powerful piece.”
At the same time, Sutton said “it’s not just a milestone.”
“It’s an outcome of the things happening every day at Mercury,” he said.
Sutton said what makes the milestone even more special is that it was accomplished while new equipment was installed in the plant and new operating protocols were implemented during the last year and a half.
“Over a multi-year process within that facility of operation, updating machines and equipment,” he said. “Those are things that require the right focus in terms of engineering and design teams and getting operator input. All of the delivery and installation of the equipment had to be coordinated amid ongoing operations. That all had to be done on top of our employees’ daily obligations.”
For more information on Mercury Marine, visit mercurymarine.com.