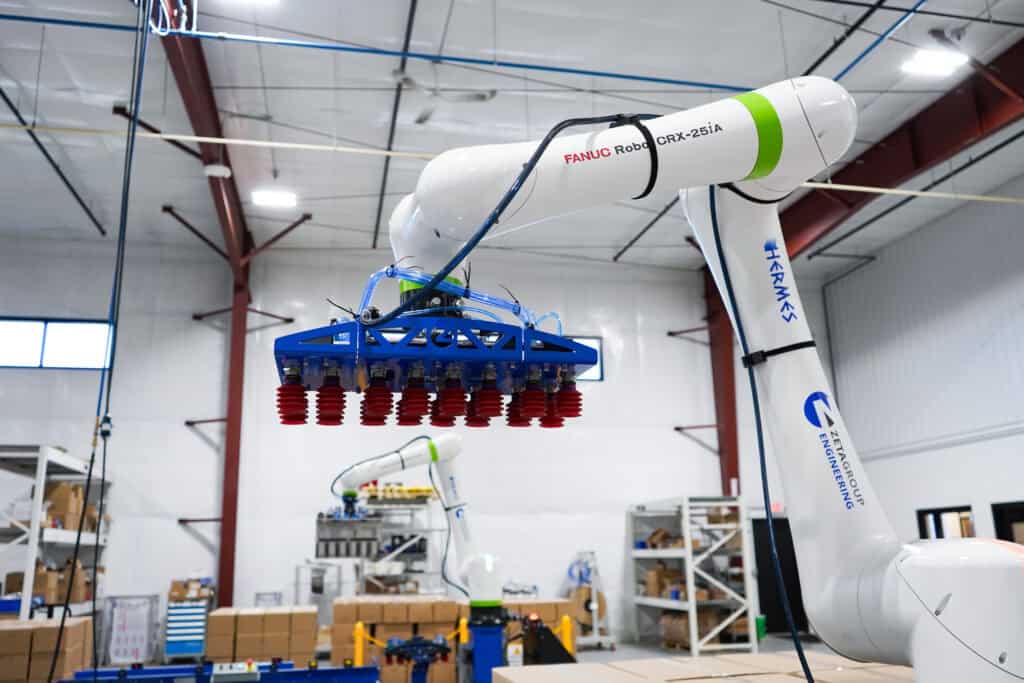
June 17, 2024
WRIGHTSTOWN – Though the complicated terminology of the robotics industry may be “Greek” to some, the leaders behind Zeta Group Engineering can ably translate the advantages of automation.
“The benefits for sure are labor, No. 1; safety is the other one; consistency; and then ultimately the labor pool is shrinking – massively,” Aaron Zimmerman, senior sales engineer at Zeta Group, said. “By 2030, there are going to be 2.2 million manufacturing jobs short of people. That timeline is not stopping, so people need to start getting on board with the automation, because there is going to be a problem.”
Zimmerman, as well as Zeta Group Owner Kevin Marrick and Director Gregg Wheeler, said solving such problems is what inspires their company’s progress.
Their go-to solution for manufacturers, they said, is named after an Olympian god – perhaps fittingly, the god of trade and commerce.
“Hermes – that’s the cobot (collaborative robots) on a mobile cart that can be utilized for palletizing, case packing and machine tending,” Wheeler said.
Zeta Group Engineering (located at 501 County Road U in Wrightstown) offers numerous robots and cobots as part of its automation solutions.
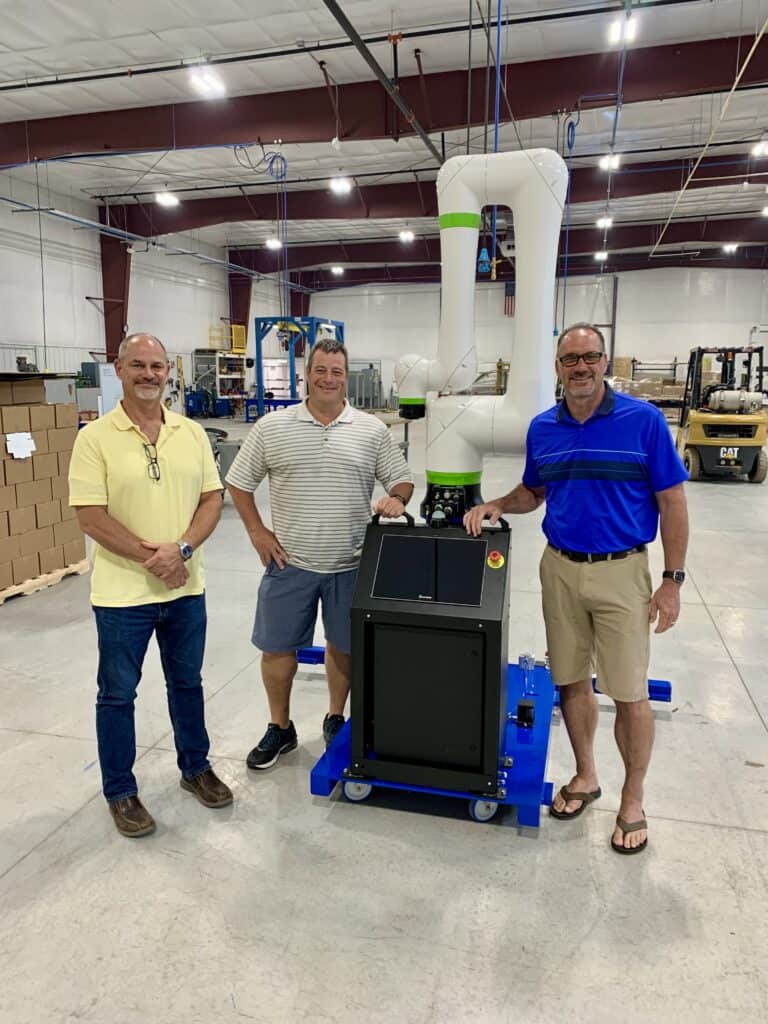
“When we talk automation, we don’t have to fully automate the process – where there was a mindset years ago like it was all or nothing,” Wheeler said. “But being collaborative – it opened the window up of, ‘what if we got you 80% there, or 60% there or 50% there – is that enough?’ It takes the burden away. Lifting heavy things – no one likes that job, so a robot doing that repetitious (task) is an ideal situation and takes away those strain points for an operator. We can automate pieces within a process – and that’s the beauty of the collaboration.”
Man + machine
Marrick said he founded the Zeta Group with two partners in De Pere in 2010.
Initially, he said, the business model focused on providing engineering services.
“That’s primarily how we started, and then in 2016, I purchased the company from my partners,” he said. “I wanted to take the company into a different direction, which was in automation – specifically with robots. (Automation has) been happening for 30 or 40 years, and it continues to be even more.”
Cobot technology, Zimmerman said, was developed within the last decade.
“Our motto here is, ‘reimagine the manufacturing floor,’” he said. “Robots before were put behind a cage – they were big, heavy, non-mobile and not easy to reconfigure. The cobot takes up the room of a person, and with that, you don’t need any of the safety cages – it’s easily deployed to other locations.”
Wheeler said among Zeta Group’s palletizing solutions are machines named after Apollo, Poseidon and Zeus, as well as conveyor solutions named after Odysseus, Perseus and Theseus.
The Hermes cobot, especially, he said, is a “game changer,” requiring only 110 volts of power, which contributes to its increased mobility compared to larger automation systems.
Wheeler also said compared to past robots where safety was ensured by separating people from close contact with machines, with cobots, “the safety is all within the robot.”
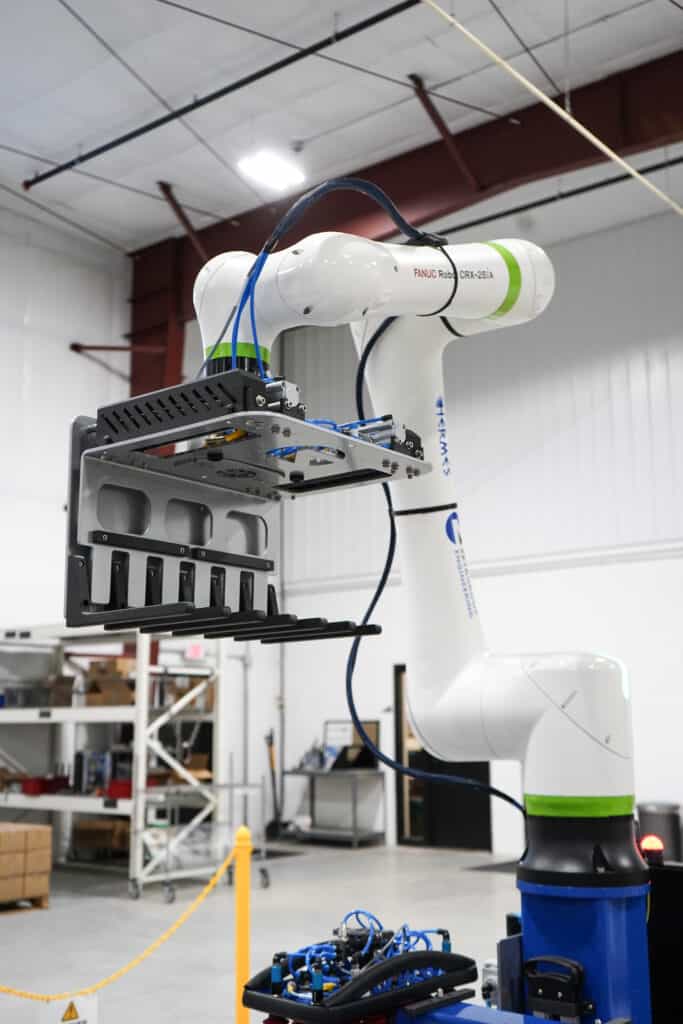
“If you bump it, it stops,” Marrick said. “It has force sensing in each one of its joints, and if any of them exceed what it’s expecting, it stops.”
These safety measures, Zimmerman said, allow for maximal integration in a manufacturing setting.
“Say it’s (working) on a conveyor belt, and the robot’s performing some task, but the next task is better created for a human to do it,” he said. “Well, you can be right next to each other and do those tasks.”
Additionally, Wheeler said, employees don’t have to shut down the system to work with it, “like you would have to do with an industrial robot.”
“(You would have to) shut it down, open the cage, go in there, do whatever you have to do and come back out,” he said. “You can work while this robot’s still working.”
Marrick said Zeta Group’s robots’ ability to work continuously provides a significant boost to manufacturers’ productivity, citing one of their customers whose annual throughput was “40% more – running through breaks and never stopping the machine.”
“When we first installed a collaborative robot that was mobile into a customer’s plant… the general manager and project manager were trying to figure out – ‘where else can we use this thing?’” he said.
Full automation: Mythical for now
Though Zeta Group primarily focuses on partnering with Northeast Wisconsin’s many manufacturers, Marrick said the company has overseen the installation of its machinery all over the United States.
Furthermore, Zimmerman said the company’s products have been uniquely implemented all over the world by various integrators.
“We evaluate each project…,” he said. “We’re based on a series of standard concepts, more than anything, and then we try to leverage that whenever we can.”
Zeta Group itself, they said, has around 16 employees, yet its partnerships – with international robotics companies for parts and knowledge and with local fabricators for additional parts – bolster the “lean” company’s in-house capabilities and expertise.
“We’re able to spread ourselves out with having these good partners,” Wheeler said.
Marrick said it’s working well now, “but we’re looking to grow.”
“Everybody’s looking to grow, but you can only grow so fast,” he said.
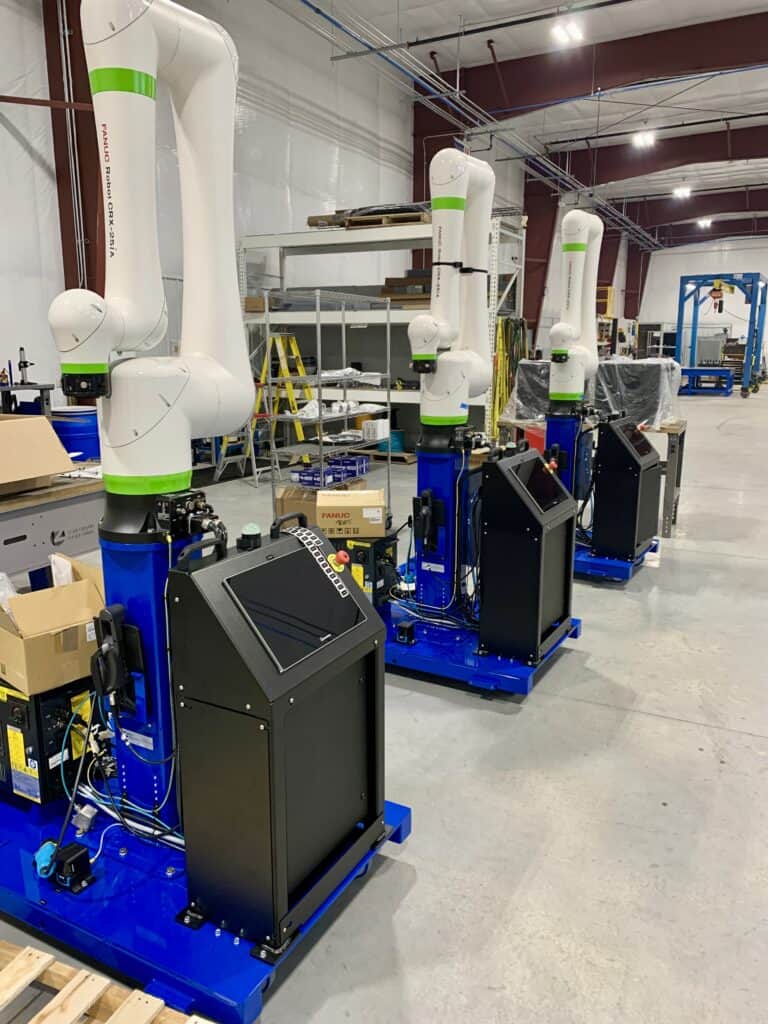
The automation industry itself, Wheeler said, is set to evolve and expand as the Fourth Industrial Revolution is embraced.
“The industrial internet of things (IIoT) and Industry 4.0 – that’s a whole new level of automation,” he said. “Smart systems, smart machines – we’re diving down that path.”
Wheeler said in anticipating these advancements, Zeta Group will be at the forefront to help its customers in implementing the latest robotics.
“You’ve got to be cautious because there’s so much there,” he said. “You have to learn how to choose small, small bites. Get the organization up and raise it together to where everyone understands what’s happening.”
Amid the imminent changes, Marrick said Zeta Group will continue to focus on developing partnerships while understanding the best ways to “interface” with the new technology.
He said human workers are still entirely necessary to manufacturing, though he said he warns manufacturers, “either you’re going to automate, or you’re going out of business.”
“This whole idea with the IIoT is applying to more stuff, and it’s better, faster and smarter,” Wheeler said. “But to get that change over in the mindset of people who own businesses that make widgets… to change their system and philosophy is a bit nuanced.”
Cobots like Zeta Group’s Hermes, Marrick said, are valuable to that transition.
“It’s more palatable, too, because when you have to automate 100% of a project, it’s probably got a higher cost,” he said. “If you’re automating 50% of it, it’s scalable, and you can phase it in.”
Learn more at ZetaGroupEngineering.com.