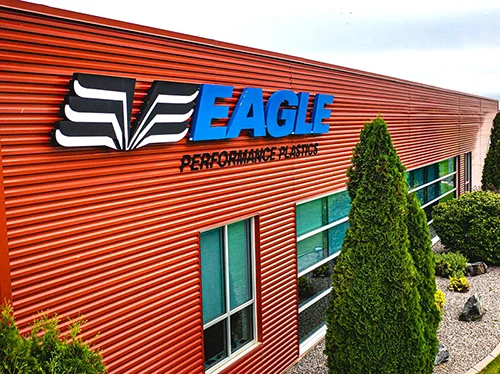
February 6, 2024
APPLETON — Various materials on the market can be machined to specific specifications, but none might be better than plastic, said Jared Bailin, president/CEO of Eagle Performance Plastics (EPP).
“Plastic components are not the do-all, end-all for every application, but (comparing) plastic (to other materials), it’s impact-resistant, wear-resistant, it weighs less and helps in noise reduction,” he said. “When you have metal parts sliding against metal parts, it creates a lot of friction. Plastic parts might be used in contact with metal, and that will make the machine operate faster and be able to use smaller motors, which can save on power.”
EPP, located at 2929 W. Evergreen Drive in Appleton, manufactures custom-machined plastic components with unique properties that improve quality and save costs, Jared said.
“We use the latest in CNC technology to provide high-quality components in small or large quantities — nothing is custom,” he said. “We manufacture plastic components for a wide variety of industries, including packaging, food processing, conveyors, pharmaceutical and special machinery, among others. A lot of food processing equipment has to be chemically washed down, so there are a lot of benefits to using plastics in that industry.”
How it started
EPP was originally founded as Eagle Supply & Plastics in 1971, by Jared’s father, David, and his uncle, Ivor Lewis.
At its inception, Jared said Eagle Supply & Plastics was primarily a distributor of engineered plastic stock shapes, such as sheet, rod, tube and film — as well as other industrial supplies to local manufacturers.
“My dad used to work for a company that is now called Russel Metals in Appleton,” Jared, who has been the president/CEO for about 15 years, said. “In the 1960s and ’70s, the company (my dad worked for) had a whole bunch of different divisions — rubber, plumbing, plastic, etc. — and my dad and uncle purchased the plastics division.”
In 1988, EPP installed its first manual lathe and manual mill.
Over time, Jason Bailin — head of business development and Jared’s son — said EPP gravitated away from distribution.
“Maybe 15-20 years ago, EPP evolved into more of a machine shop,” Jason said. “Then in 2013, Eagle moved into a new, modern, 42,000-square-foot, climate-controlled facility right off the highway. Now, we only machine plastic. At the same time, we eliminated the distribution part of our business. Everything we do now is custom, plastic components.”
How the process works
Jared said EPP first purchases different plastic materials — rod, plate, tubular bar — from companies, primarily located in the United States.
“There are a lot of high-tech, engineered-grade plastics that all have different capabilities and specifications,” he said. “We have quite a large inventory of stock on hand where we can pull it off the shelf and machine the parts to our customer’s specifications.”
Jared said there are “probably more than 100 types of plastics available.”
“People are always trying to formulate new versions of things,” he said. “New materials are always coming on the market — they each handle different requirements and needs.”
Jared said most of the orders EPP receives come in small quantities.
Eagle Performance Plastics manufactures most of its plastic components for its customers in smaller quantities. Submitted Photo
“Sometimes it’s one or two parts, other times it’s a dozen, 20 or 50,” he said. “On occasion, we do hundreds or thousands, but the majority of our orders are in small quantities. Some parts are repeated, but most are custom.”
Jared said all the parts are programmed on a CNC (computer numerical control) machine.
To remain at the top of their game, Jason said much emphasis is placed on cutting-edge equipment.
“Every year, the company reinvests a lot back in the form of new machines and equipment — about two or three a year,” Jason said.
Sustainability
Like other materials, plastic can be recycled, but Jordy Krall, materials and applications technical resource at EPP, said there are difficulties with it, too.
“When we’re cutting off a large chunk of plastic for a part, we’re easily able to separate that,” he said. “We put that scrap in different bins. Where we see more problems is the shavings that are created from machining. Those shavings mix with other things, so there currently isn’t a good way to separate those. We’re currently looking at some options.”
Jason said there’s a company in Green Bay that can take the waste plastic and combine it with other things to make it useful.
“They can combine it with different fibrous paper materials, and they use that as a sustainable fuel source,” he said. “We’re exploring that option for 2024. There’s a lot of work being done on our part, and we’re continuously looking at different ways to recycle the plastic.”
Youth apprenticeship programs
Jared said since EPP’s inception, “we’ve always used youth apprentices or co-ops as they used to call it.”
“During the last 15-20 years, we’ve gotten even more involved with high schools and other programs for youth apprenticeships,” he said. “I was the founding board president of ATECH (Appleton Technical Academy), which was started at Appleton West High School.”
Jared said current Appleton Area School District Superintendent Greg Hartjes had the idea to start a charter school in Appleton, dedicated to manufacturing.
“After he and I chatted about the need for machinists and other types of manufacturing careers, that’s when things came to fruition,” he said. “I don’t think most kids — or people in general — understand what manufacturing is about — especially modern manufacturing.”
Jared said manufacturing is a very important contributor to the Northeast Wisconsin economy.
Eagle Performance Plastics is housed in a 42,000-square-foot, climate-controlled facility at 2929 W. Evergreen Drive in Appleton. Submitted Photo
“Manufacturing has a bad rap from its history of being not a prestigious type of career,” he said. “In actuality, today’s manufacturing jobs are high-tech. Most of the manufacturing shops around here are clean, organized and modern, and they use up-to-date equipment. The knowledge level of a manufacturing person around here is high — people don’t generally understand that.”
Jared said folks can “have an incredible career” working in manufacturing without necessarily needing a four-year college degree.
“We try to get kids in high school exposed to the different areas of our shop,” he said. “If this is something they have an interest in or an aptitude for, we help support them through Fox Valley Tech, usually, or any two-year trade school while they are working. We also have our own in-house training program where we train young people and our employees on new levels of machining.”
On a monthly basis, Jason said one or two local high school classes come through and tour the EPP facility.
“We do a hands-on tour with them and show how the parts are being made,” he said. “We recently had a machinist who went to an area high school and led a program in class. He was there twice a week for three weeks. He worked with the students hands-on — we’re always looking for ways to jump into the schools and get students involved.”
Jason said they typically have two to four youth apprenticeships every semester.
“It’s been that way for a long time,” he said.
Jared said the youth apprenticeship program is one of EPP’s missions.
“Not only do we need solid, talented employees, but all of our customers need that, too,” he said. “Whether we expose (our youth apprentices to opportunities in the industry) and they come work at Eagle or work somewhere else in Northeast Wisconsin, it’s a win-win for us.”
For more information on Eagle Performance Plastics and its youth apprenticeship program, visit eagle-plastics.com or find it on Facebook.