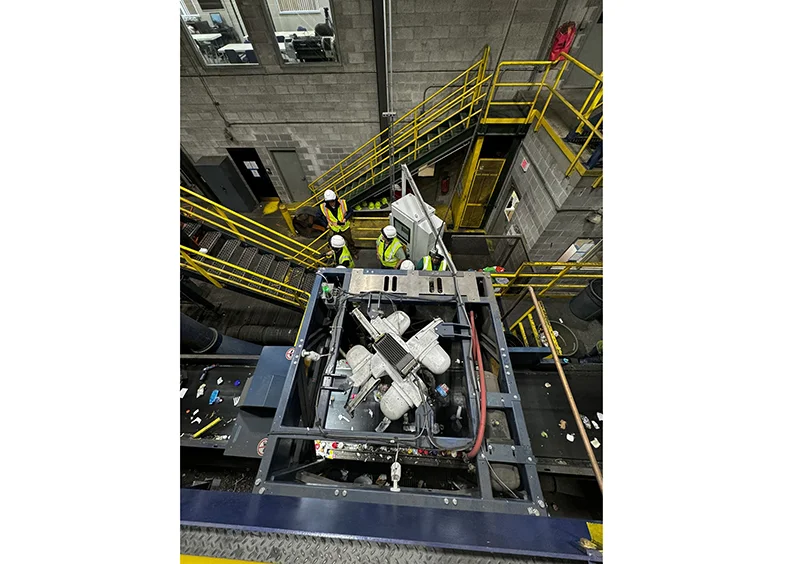
April 3, 2024
APPLETON — Up until late last year, about 8-9% of all material collected by the Tri-County Recycling and Solid Waste ended up in the landfill.
Granted, Jordan Hiller, Tri-County Recycling and Solid Waste Program Coordinator, said it’s not a bad number — the national residual rate average among recycling centers is about 25%.
But Hiller said he knew Northeast Wisconsin could do a lot better.
“Even with that low residual rate, we thought that anywhere from 3-3.5% of that is still recoverable material — so things like plastic, aluminum and metal made their way through the system,” he said.
Hiller said Tri-County determined, based on its compactor audit, that only some things were getting thoroughly sorted.
“We determined we could potentially be throwing away upward of $1,000 a day in materials that could be processed and recycled,” he said.
At the same time, Hiller said the recycling facility was having trouble remaining fully staffed — with some processing lines being left open because there was no one to staff them.
“We were severely understaffed when I came on board in December 2022,” he said.
Enter the robots.
Hiller said Tri-County added three robots to its operations, with a fourth coming this year — additions he said have amplified the work the facility can do.
The robots don’t do anything their human colleagues on the line aren’t able to do, but Hiller said because of the sheer amount of materials Tri-County takes in — it is more than a couple dozen workers on two shifts could reasonably be expected to catch.
He said the robots have allowed facility staff to be shifted around so that now, all areas are covered.
“We’re now back up to 100% and almost 105% staffed,” he said. “We’ve been able to move people to areas that have not seen sorting staff in months, if not years.”
Hiller said it has meant the facility’s contamination rate has gone down — meaning fewer non-recyclable items are getting into areas they shouldn’t be in, and vice-versa.
It is also important to point out, Hiller said, the robots haven’t replaced people.
“Zero employees have been laid off,” he said.
Instead, Hiller said the robots support the work Tri-County employees are already doing.
Sensing garbage
Hiller said Tri-County’s three (soon to be four) robots were developed by AMP, formerly AMP Robotics Corp and are among fewer than 200 robots of their type in the country.
Each robot’s housing unit, he said, stands about six feet tall and measures about five feet wide and four feet deep.
Though the robots have been in place and operating since November, Hiller said they wanted a few months without fanfare to make sure the robots were established and running smoothly before making a public splash.
That splash came last month when Tri-County held an open house and welcome event for the robots.
Like a heat-seeking missile
The machines, Hiller said, are suction-oriented and use artificial intelligence to sort recyclables from trash.
The robots remain motionless as a conveyor belt moves goods along, until they spy certain items and with what he describes as eagle-like reflexes, a device’s tube reaches out and sucks up materials.
So, how do they sense No. 2 plastic from No. 5 plastic or No. 1?
The robots, Hiller said, use a vision system that works a little like security footage.
“The vision system is like the eyes of the technology,” AMP Director of Communications Carling Spelhaug said.
AMP’s software, Spelhaug said, has pattern recognition and looks for traits such as color, textures, shapes, sizes and logos, rather than for the little triangles with numbers on container bottoms.
Hiller said the machine matches what it sees with what it knows, based on the information it already has.
“It uses all of that information it already has stored in its database with millions upon millions of data points in its cloud system,” he said.
Hiller said it’s able to determine, with a high degree of certainty, that the material is what it thinks it is, and that’s what tells the robot what to pick.
Spelhaug said the technology is growing in use among recycling centers throughout the country — with the company designing solutions specifically for the waste management arena.
Other uses
After the recyclable items are sorted into paper, plastics, metal, etc., Hiller said they get sold to processors.
Shingles, paper, cardboard, aluminum, etc., he said, all go to facilities that can process it and make other goods from it.
Plastics, Hiller said, get sent to companies that chip it, melt it down and turn it into pellets or flakes — who then sell it to manufacturers who make new items out of it — such as new bottles, jugs, etc.
Mitch Becher — of Becher Plastics of Appleton, a manufacturer of recycled plastic — said recycling can save a lot of money.
Becher said for a manufacturer buying plastic, the difference between virgin plastic and recycled plastic can be 25 cents per pound.
“That is quite a bit of savings when you multiply 40,000 pounds on a semi-truck,” he said.
According to the Plastics Industry Association, plastics are made from raw materials, such as natural gas and oil, that are refined into propane and ethane — another reason Hiller said why recycling is important.
“When you recycle, you are saving those virgin resources from being mined or pulled from other places, as well as the emissions it takes to create those,” he said.
For more on Tri-County Recycling and Solid Waste and its robots, visit recyclemoretricounty.org.