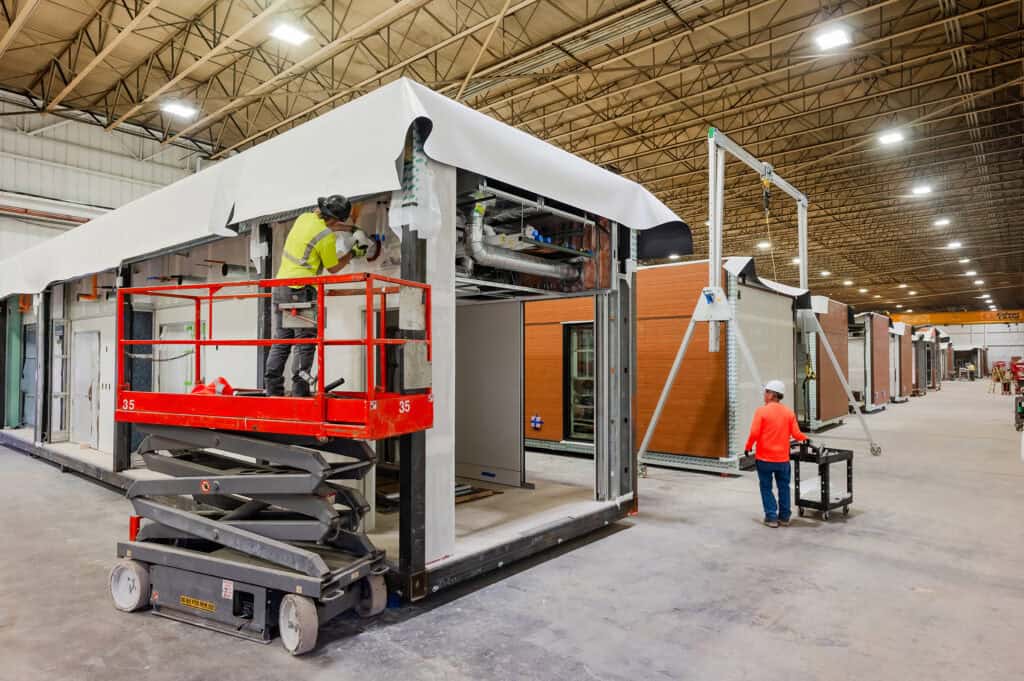
January 27, 2025
OSHKOSH – By 2031, the National Center for Construction Education and Research projects that 41% of the construction workforce will retire.
As the industry continues to do what it can to inspire the next generation to choose a career in construction, companies are turning to other strategies as well to help address the looming gap.
In response to evolving industry dynamics, one such company, Appleton-based The Boldt Company, is reimagining how buildings are planned, designed and delivered by launching Bildt, a modular and prefabrication manufacturer.
Dave Kievet – president and CEO of The Boldt Group, which encompasses Boldt and Bildt – said by leveraging manufacturing techniques to industrialize construction, “Bildt can deliver higher-quality work at a lower cost, with complex work broken down into simpler tasks that can be learned quickly in a manufacturing environment.”
“Additionally, Bildt is able to strategically locate its manufacturing centers in more densely populated areas where labor is more readily available, minimizing the cost to perform work in more rural and remote regions,” he said.
The right time
Vice President of Modular Ben Bruns – who leads the new Bildt organization with Vice President of Manufacturing Melanie Taylor – said Bildt was created in response to interest from facility owners, general contractors and architects to reduce project costs and increase speed to market.
“In my view, it’s past time the industry does this,” Bruns said. “I think it’s time that the industry makes it easier to come to work in the construction industry, makes it easier to be productive in the construction industry and makes it easier to have a better buying experience as a customer.”
The lack of reliability of conventional construction supply chains, combined with the cost escalation brought on by the COVID-19 pandemic, Bruns said both played a part in the need for an organization like Bildt.
“I really do think that we’re past due as an industry to grow up some,” he said.
Looking at the launch through the lens of employees or potential employees, Taylor said the Bildt facility provides stability and consistency.
“Our location is permanent, and our shop workforce is local, allowing our team to go home to their families every night,” she said.
Taylor said the facility also offers employees numerous amenities that aren’t necessarily standard on an off-site job site – including clean break rooms, indoor bathrooms, climate-controlled conditions and convenient parking.
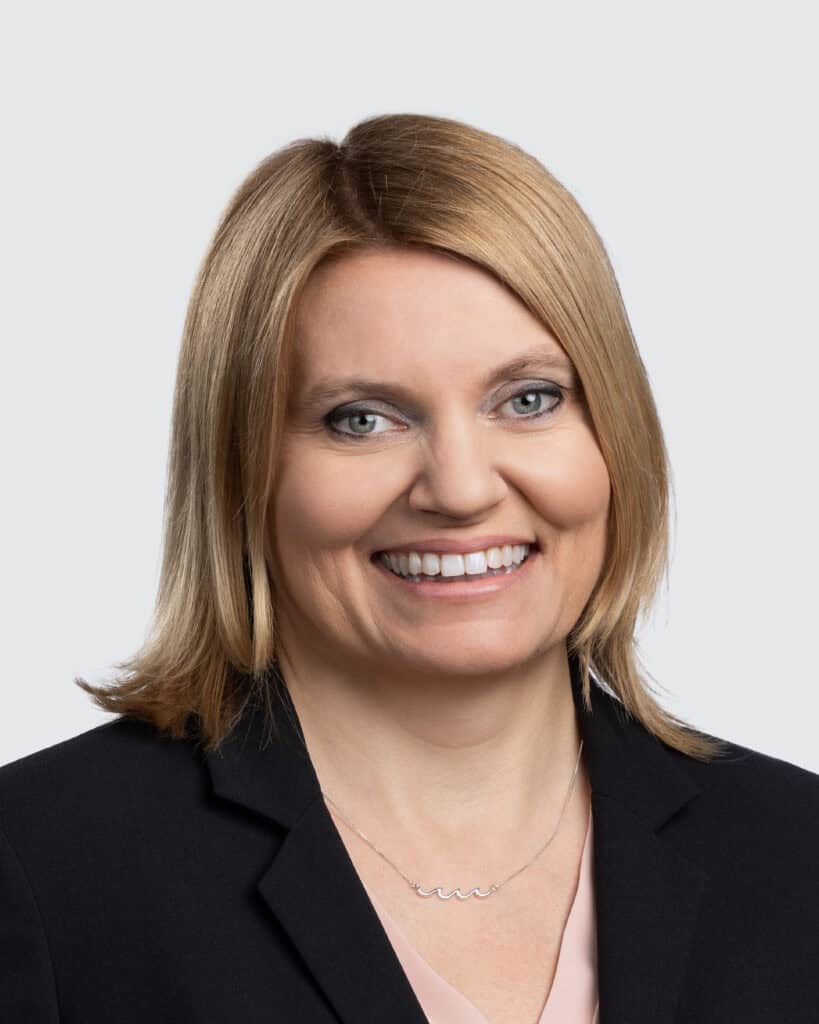
Beyond the creature comforts, Taylor said Bildt’s prefabrication and modular facility minimizes variability, improves safety and reduces some of the physically demanding conditions of a construction site.
“Work is performed at ground level with ergonomic considerations,” she said. “Overhead cranes handle heavy materials and pathways are marked for safe travel. Tools are stored in carts instead of heavy tool belts.”
Personally, Taylor said she’s most excited that this approach is attracting more women and other people from the community who might not have previously considered construction as a career option.
“The accessibility and face of construction is changing,” she said.
Furthermore, Taylor said Bildt’s prefabrication and modular construction addresses the construction industry’s skilled labor shortage by:
- Lessening barriers to entry
- Mitigating the effects of labor shortages in remote locations
- Reducing the need for constant presence of specific skilled tradespeople on a job site because a significant amount of labor occurs in Bildt’s manufacturing facility
- Making training easier because the complex work done within the manufacturing facility is broken down into simpler, repetitive tasks that can be learned quickly
A welcome addition
Over time, Taylor said productivity and efficiency have drastically improved in manufacturing, “while remaining stagnant – or even declining – in construction,” which further supports the purpose of Bildt.
“For years, innovative construction companies have been integrating Lean manufacturing principles into Lean construction,” she said. “We are in the next evolution of this journey.”
Beyond production improvements, Taylor said modular and fabricated construction offers several advantages, including:
- Faster delivery or speed-to-market for customers
- Improved safety
- Enhanced quality
- Increased sustainability
- Better employee well-being
“Additionally, clients facing challenges like adverse weather, economic conditions and shortages of localized skilled labor find modular and fabricated construction to be the ideal solution,” she said.
Bruns said one of the aspects of Bildt that other general contractors find intriguing is “we are a general contractor.”
“So we know what it’s like if something doesn’t show up on time, and how cascading the effect of that is,” he said. “We understand the general contractors in particular are often the bearers of bad news that wasn’t their own makeup.”
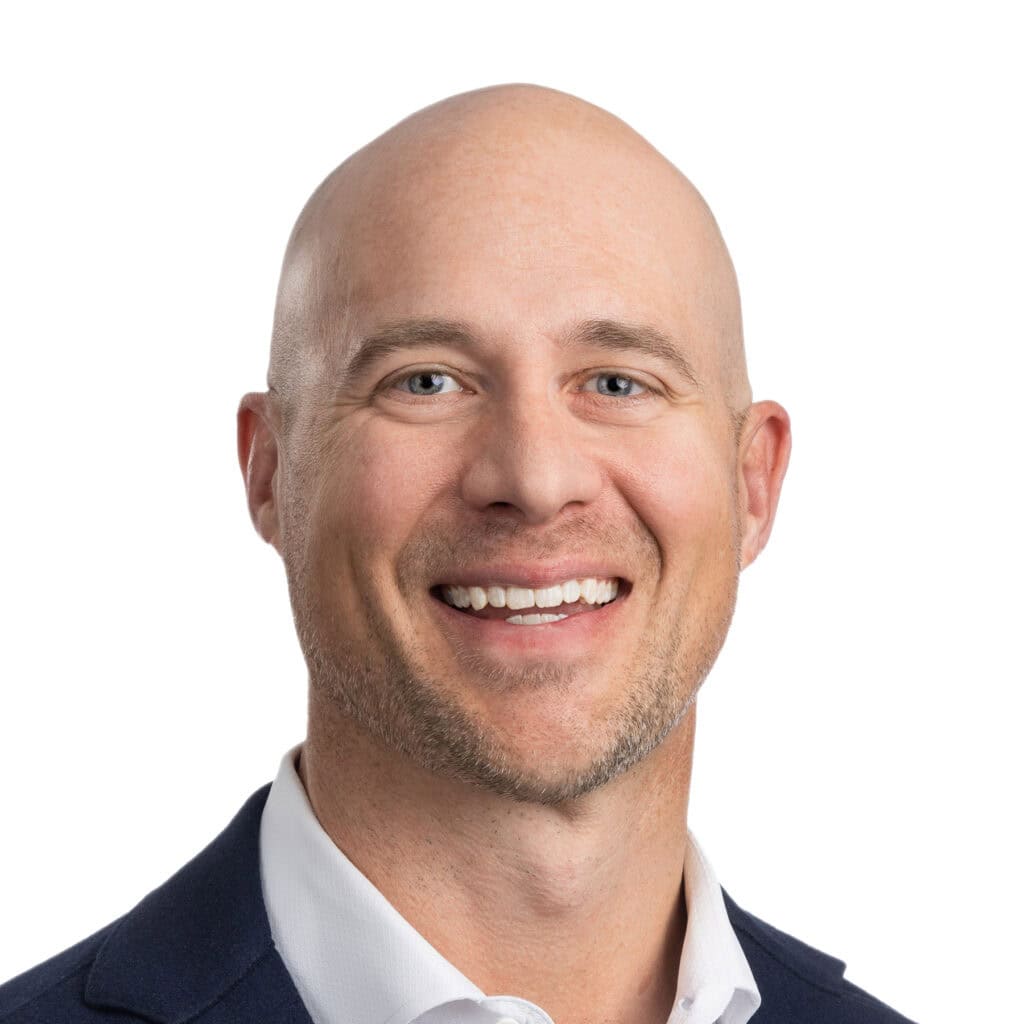
Launching Bildt – which is solely focused on helping support the ever-changing construction industry – Bruns said, can help dramatically improve the reliability of those promises they’re making.
“By taking some of the most repetitive, complex components off the table, we are adding a much higher degree of reliability,” he said.
In the construction industry, Bruns said it’s a given that there will always be some sort of challenge – “it’s still construction” – but how a company responds also matters.
“How you communicate in that setting when something isn’t perfect and how you react and respond and deal with adversity – how you own those things – is such an important part of doing good business,” he said.
The Bildt team, Taylor said, is “energized, prepared and ready.”
The industrialized construction industry, she said, has also shown “incredible support and enthusiasm for our launch.”
“As a growing industry, advancements by one benefit us all,” she said.
Going the extra mile
Bruns said Kievet has had a vision for Bildt for a number of years.
“Dave started to put together the architecture of what our modular business could look like and really wanted to invest in it from a company level,” he said.
Bruns said Taylor and the team “road tested” one of the modules while working on a hospital project around the time of COVID.
“The STAAT MOD concept (within Boldt) was born at that point,” he said. “Since then, we’ve taken this and have been able to adopt the technology into many more parts of the business.”
By creating a new standalone business, Bruns said The Boldt Group is “going that extra mile.”
“We could have continued to do this inside of Boldt, but the point is, the whole industry needs this support,” he said. “Dave is looking to Mel and I to help grow this dramatically.”
Bruns said the plan is for other general contractors and architecture firms to be customers of Bildt – describing the company as “an easy button for both facility owners and contractors alike.”
“The elements that are true about Bildt are: It’s much faster than conventional construction, regardless of what solution we’re talking about,” he said. “(And) it’s very high quality, because it’s built in a factory, so we’re able to control things so much more than you would otherwise.”
Many of the conflicts that exist inside of traditional design and construction, Bruns said, are “ironed out on the front end” through Bildt.
“There are no change orders, because we had to talk through what the product was going to be on the front end,” he said. “There are no requests for information, because we already know everything that needs to be known. The line we like to use is, ‘We’re buying rebar and coat hooks at the same time.’”
In addition to providing reliability and consistency, Bruns said there is also a sustainability component of Bildt.
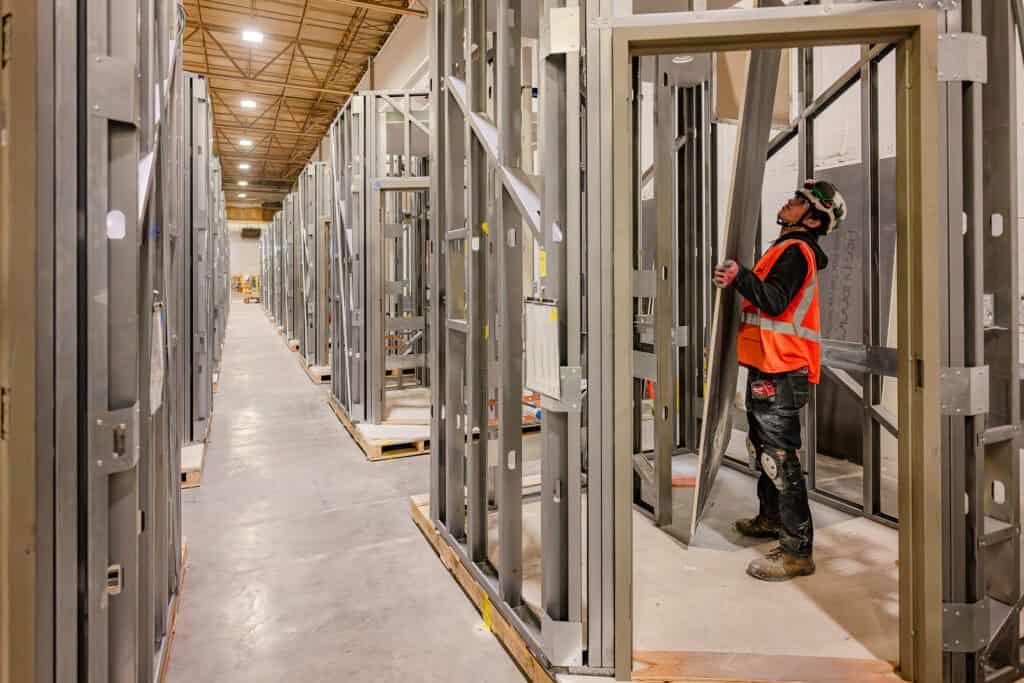
“Think about the carbon footprint of a job site, all these people and all this equipment, all this stuff coming to the job site,” he said. “We had metal studs set up at the job site, and then we had to trim them to length. We have a stud machine in our warehouse that manufactures them, dimples them and puts a hole where the fastener needs to go – so there is no waste from that process.”
Doing all the work at the facility, Bruns said, also cuts down on transportation costs and emissions.
“The whole thing goes on the road one time to a customer, as opposed to everybody driving their vehicles to the job site every day,” he said. “We are producing bathroom pods – all of the bathrooms for these hospital projects we’re working on currently – in our factory.”
Bruns said with a significant amount of Boldt’s portfolio in the healthcare industry – “Boldt has a great reputation (within the industry)” – highlights the capabilities of Bildt in regard to complex and repetitive projects within the healthcare, industrial, education and commercial industries.
“Our customer has done a study that said that’s going to cost them 30-plus% less,” he said. “When you install these elements, you basically just leave the door closed and you don’t have to go back in it. Then all the mess of cutting tile and all those things that you would do on the job site late in a construction process, near a patient room, go away completely.”
In addition to permanent modular units, Bruns said Bildt manufactures prefabricated panels and components, including headwalls; exterior wall panels and systems; steel wall studs; and interior framing assemblies tailored to project specifications.
“There are a lot of different components that go into the headwall of a patient room,” he said. “So, you know, prefabricating those headwalls, prefabricating entire exterior facades of buildings, interior walls.”
Bruns said Bildt also offers what they call slide-in pods.
“If you go into an office building or a clinic and you see the center core office or exam room areas – all of that can be shipped on a truck with all the millwork hung on the walls, sinks installed, all lights, ceilings, etc. done,” he said. “We just slide it into the building and hook it up.”
Just getting started
Bruns said the Bildt team consists of about 30 employees, many of whom have spent the majority of the year setting up the business to be autonomous and focused on a variety of markets.
He said Bildt also allows the overall company to do more things simultaneously.
“Previously, the business had enough resources to sell a project, and then you do a project, and then sell a project, and do a project,” he said. “You would go through these curves of the ups and downs associated with that. We’ve made the investment with (launching Bildt) and in the staff that it takes to be able to sell and do projects at increasing scale.”
Bruns said he anticipates “dynamic growth” as customers continue to learn more about the benefits of this kind of technique.
“We have several stories from customers who have loved (the prefabrication and modular capabilities of Bildt),” he said. “They’re shocked about how fast they come together and the quality associated with them.”