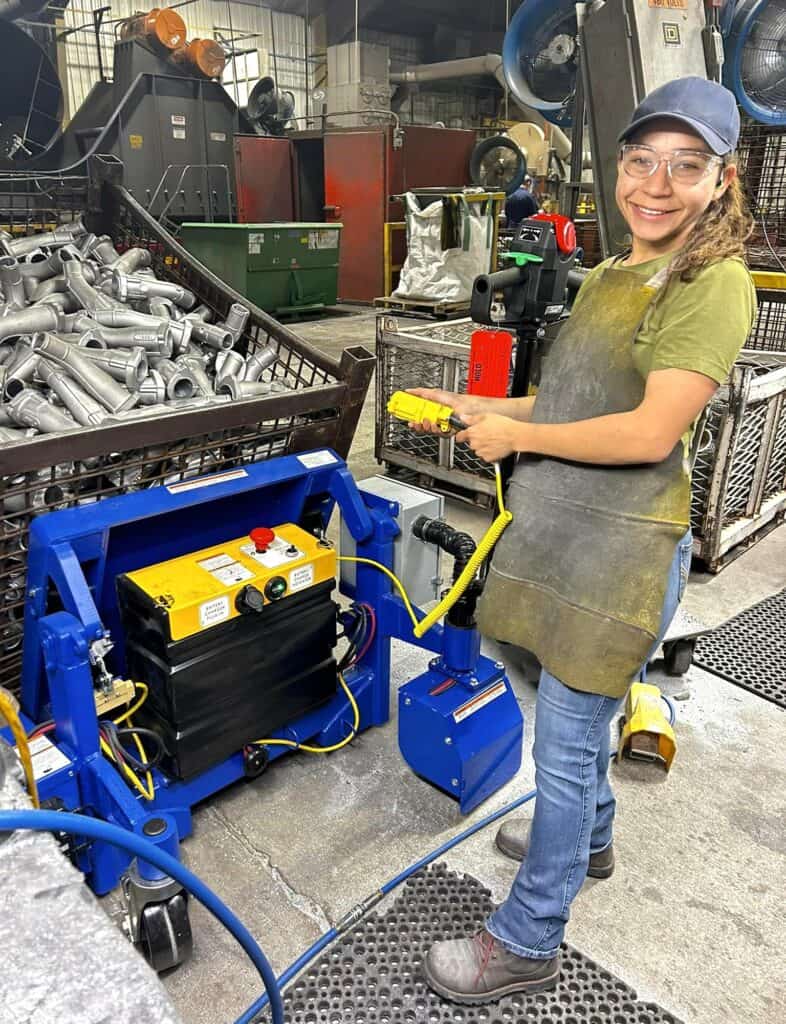
October 7, 2024
MANITOWOC – Beginning operations in 1909 – 10 years before the Green Bay Packers became a franchise – Wisconsin Aluminum Foundry (WAF) had just three accounts: Harley Davidson, Wisconsin Motors and Evinrude Outboard.
Today, 115 years later, WAF (838 S. 16th St. in Manitowoc) employs more than 900 and has multiple divisions, including WAF, Wabash Castings (Wabash, Indiana), Dee Manufacturing (Crookston, Minnesota), Manitowoc Pattern & Machining (Manitowoc), All American 1930 (Manitowoc) and ATEK Metal Technologies (New Hampton, Iowa).
“Here we are 115 years later, and Wisconsin Aluminum Foundry remains family-owned and focused on growth through serving clients, employees and the community,” Rich Schwartz, WAF Board of Directors chairperson, said.
Schwartz said WAF is now known for designing and manufacturing custom aluminum and copper-based alloy castings for specific applications in a wide variety of industries, including automotive, marine, oil, agriculture, defense, medical and residential.
Being in business for 115 years, WAF CEO Sachin Shivaram said, “is extremely rare.”
“When I tell people we’re in our fifth generation of family ownership, they’re always surprised – businesses rarely make it that long,” he said. “It speaks to the philosophy of the family.”
Shivaram, who became WAF’s first non-family CEO in 2019, said foundry leaders routinely invest back into the business.
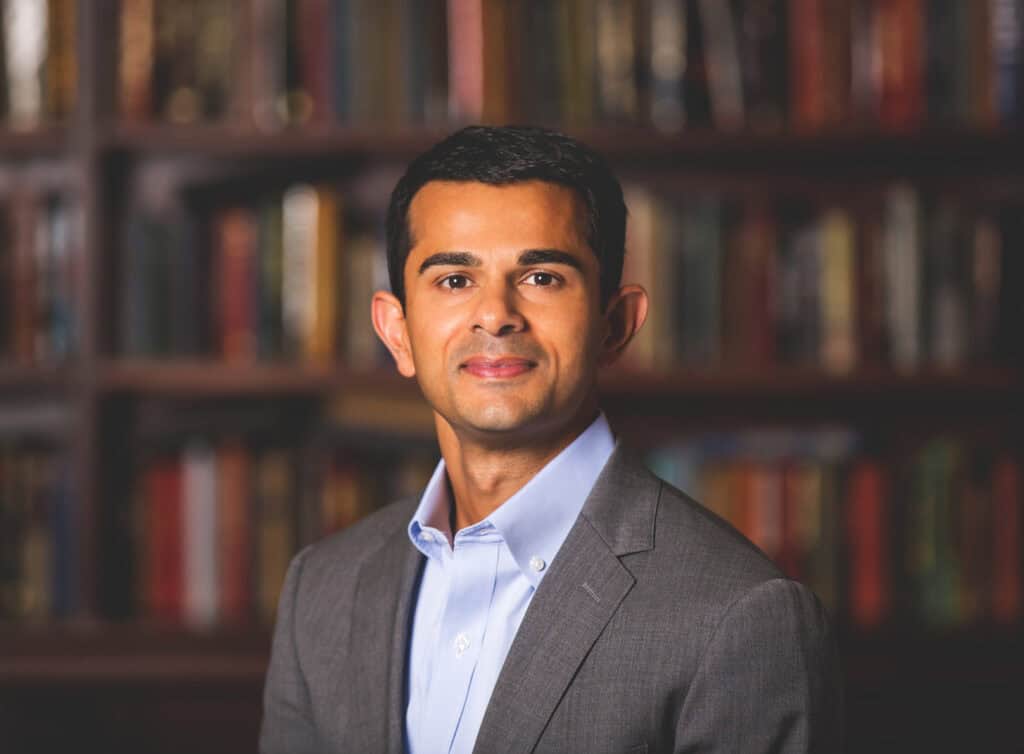
“They are dedicated to investing in the foundry – the building, new buildings, equipment, the people, etc.,” he said. “With many businesses, they might put off purchasing new equipment – trying to make it last another year or two. Eventually, 20-30 years go by, and all of a sudden, you’re left with an under-invested business. The Schwartz family is quite the opposite. At every turn, they’ve always decided to put money back into business and keep it going. I think that’s how we’ve lasted.”
In 2020, WAF invested $11 million into the facility, including a new production line, Shivaram said.
115 years in manufacturing
According to its website (wafco.com), WAF was originally named Manitowoc Brass Foundry Company.
Abraham Schwartz renamed the company Wisconsin Aluminum Foundry in 1912 and began expanding product lines and offerings – which included the opening of a brass and bronze foundry in the mid-1920s that primarily served Manitowoc Shipbuilding Company.
Company leaders, Shivaram said, credit four key areas for the firm’s success: entrepreneurial spirit, high-quality manufacturing, dedicated employees and supportive communities.
“The Schwartz family understood from day one that the future of the company relied on our employees and that each team member had a pivotal role in the company’s success,” he said. “The communities where we are located also play a role, supporting growth and expansion efforts. We take pride in returning that support through active community involvement.”
As for the future, Rich Schwartz said he expects WAF’s growth to continue.
“We view change – positive change and growth – as a constant,” he said. “We look forward to setting the stage for the next 100 years and beyond. On behalf of our leadership team, we want to thank all of our employees, customers and the community.”
More efficiency
Though technology has advanced at a rapid rate at WAF, Shivaram said some things have remained the same in the foundry/casting industry.
“For instance, we invested in a new production line a few years ago,” he said. “We can make three times the amount of production with one-fifth of the people. For some people, that might be a chilling statistic in terms of reducing the need for labor, but we all know we operate in an environment of a labor shortage. We’re not reducing jobs with automation – we’re enabling our people to be more productive. Technology has changed a lot.”
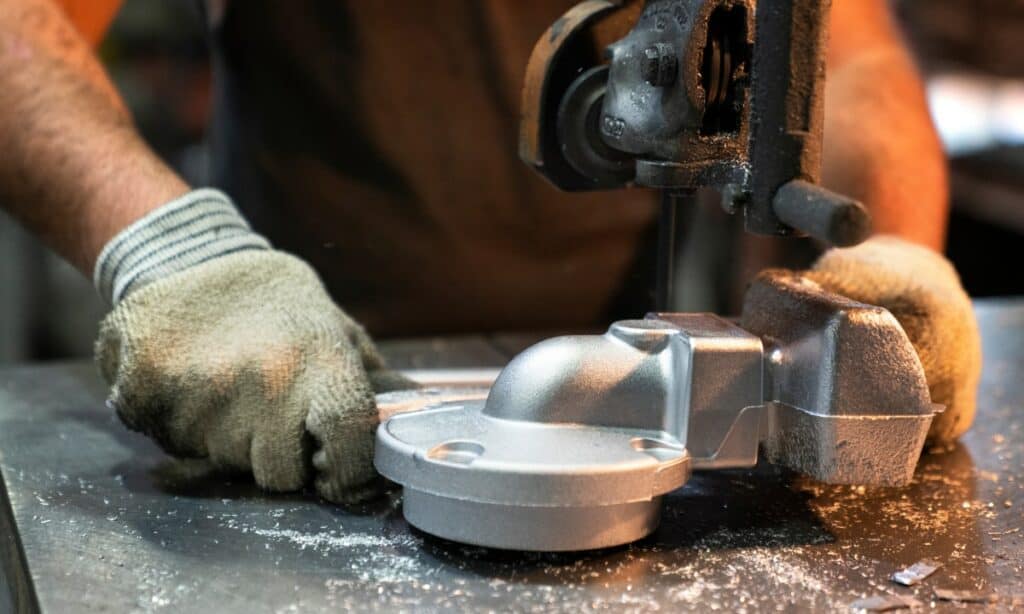
Shivaram said the new production line in Manitowoc “has amazing technology.”
“In terms of robotics, it’s nothing like anyone imagined years ago,” he said. “I’d say the pace of technological change is accelerating, but in many respects, the foundry industry also hasn’t changed. This is truly a millennia-old practice of making sand molds.”
Sand, as a material, Shivaram said, is perfect for castings.
“It’s insulating and holds its form,” he said. “For thousands of years, people have done it this way, and in many respects, that act of making a mold and filling it with molten metal is the same.”
Though WAF doesn’t have the vacancies it used to, Shivaram said like many other companies, the foundry has experienced workforce challenges.
“It’s certainly down from where it used to be,” he said. “I think right now, we maybe have about 30 vacancies, which is a little bit less than 5% for overall jobs.”
According to its website, WAF employees have an average tenure of 22 years.
“I think that says something about our company,” Shivaram said.
Sustainability efforts
Though sometimes foundries get a bad rap for being dingy and dirty, Shivaram said WAF is far from that.
“When people walk through WAF, one of the first comments I always get is, ‘wow, this place is clean,’” he said. “Our people take a lot of pride in cleaning up after themselves and ensuring that it’s bright and airy. A foundry is definitely hot in the summertime, but we have a lot of great systems to keep it a good working environment and very clean.”
Shivaram also said WAF does some “cutting-edge things” – specifically with its carbon footprint.
“We track all of our carbon emissions,” he said. “Many people might be familiar with the concept of Scope 1, 2 and 3 regarding carbon emissions. These are terms for different degrees of carbon emissions.”
Emissions directly emitted from an operation, Shivaram said, would be Scope 1.
“Scope 2 is what your suppliers emit, and Scope 3 is what our customers are doing,” he said. “There’s increasing regulation around that for big companies needing to track and monitor this, but no one is talking about a little foundry in Wisconsin needing to do this. We want to get ahead of the curve and show our customers that we’re good stewards of the environment.”
Because of this, Shivaram said WAF contracted with a company three years ago to track and monitor the company’s carbon emissions.
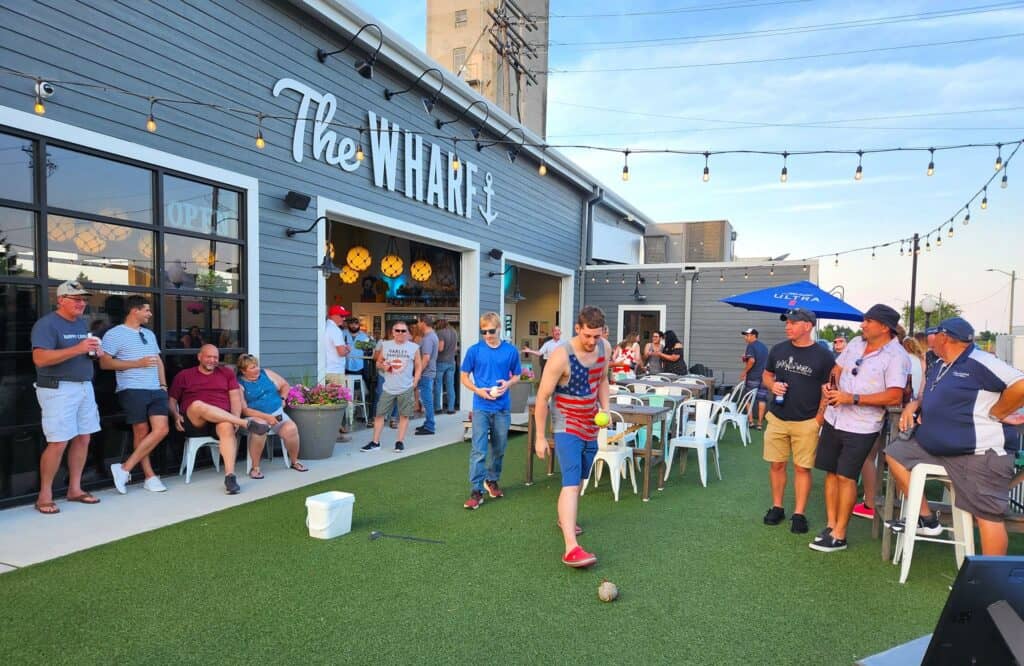
“I haven’t heard of any other company in our industry our size doing what we’re doing on the carbon front, and I think that’s another example of our commitment to sustainability,” he said.
Because of WAF’s sustainability efforts – among other things – Shivaram said, “I have no doubt we’ll be here for another 115 or 215 years and beyond.”
“I think it goes back to the central theme that we started with in terms of what has kept us here this long,” he said. “It’s this commitment to sustainably running the business. We clearly need to act in a way that helps sustain our environment. We also think about the same in terms of our employees. We need to be the type of employer that makes work sustainable for them.”
Shivaram said that comes in the form of having good working conditions and other benefits.
“We don’t want miserable working conditions because then our employees will get burned out,” he said. “For instance, we support our employees in child care because we understand what it takes to sustain a family. If you’re not able to pay for child care, then your work-life balance is not going to be sustainable. We’re committed to this concept of sustainability across generations in all facets of what we do.”
A fun time had by all
To celebrate its 115 years as a fifth-generation family-run business, WAF recently celebrated with its employees.
“We had a dunk tank at the event, and though the line was long (to get a chance to dunk me), some of the supervisors had longer lines,” Shivaram laughed. “In all seriousness, it was a great day of celebrating our accomplishments over the years with our employees. The event was held at The Wharf Manitowoc on the riverfront.”
Though WAF has plants in three other states and half of its employees are outside of Wisconsin, Shivaram said “the beating heart of the foundry is still in Manitowoc.”
“There was no other choice to hold the celebration anywhere else but here,” he said. “We invited all of our employees and their spouses and gave away fun gifts.”
Staying true to its roots of giving back to the community, Shivaram said WAF used the dunk tank as a means to help local charities.
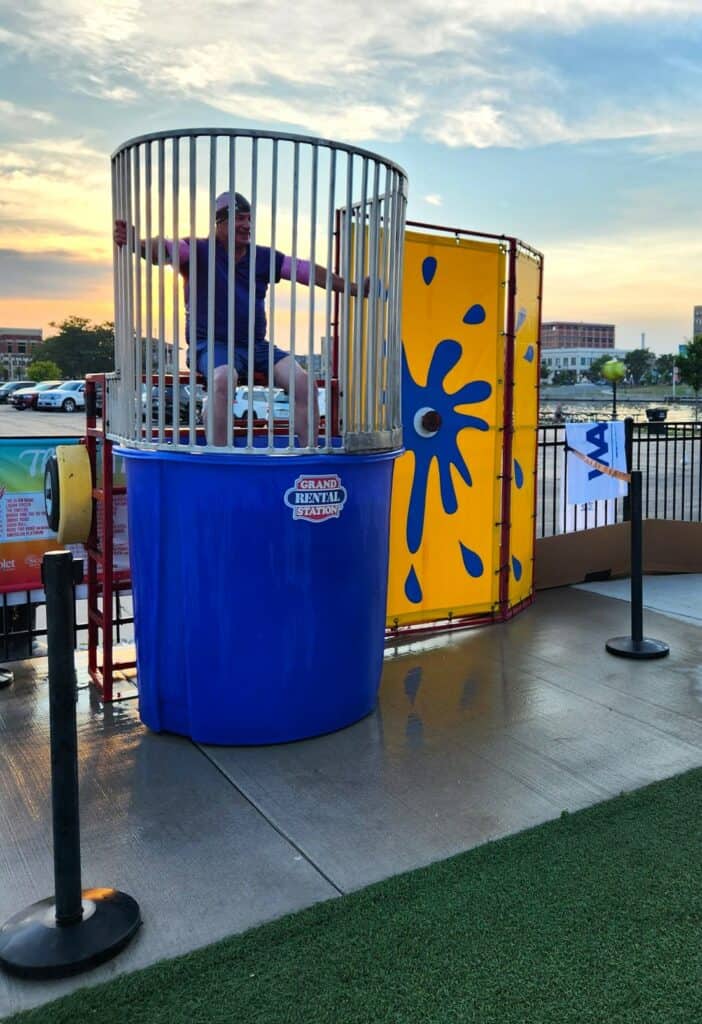
“For every dunk, we donated to a charity of whoever made the shot,” he said. “We ended up donating several thousand dollars to local charities. I think the one we donated the most to was the Lakeshore Humane Society – that was a very popular one.”
Shivaram said WAF’s philosophy has always been about giving back to the community.
“Like so many family companies in the area, investing back in the community has always been a fundamental part of who we are, starting with Abraham Schwartz,” he said. “We found his obituary for when he died in the 1950s. He was an immigrant to the area and built his career. In his obituary, the first line talks about how generous he was. That spirit has carried through the company from its founding days through today. The idea of utilizing our celebration as a platform to give back made so much sense.”
Though the event was “great fun for everyone,” Shivaram said one moment stood out for him.
“Probably the best moment of the whole event dealt with one of our newer employees and her son,” he said. “She’s a single mom and recently moved from Iowa to Wisconsin to work for us. She brought her 10-year-old son as her plus one. She doesn’t speak English really well, but her son does. He’s growing up in America and enjoying everything – that’s what his mom is working for.”
Shivaram said as the event wore on, the young boy started hanging out by the dunk tank.
“With every dunk, he was celebrating,” he said. “At the end of the day, he asked me, ‘can I go on the dunk tank?’”
Though it was previously occupied by only adults and employees, Shivaram said the youngster was able to give it a go.
“He sat in the dunk tank and had the time of his life – it was such a great moment,” he said. “The jobs WAF offers help transform people’s lives. Our employees can make good money at WAF, so many employees can help put their kids through college. They buy houses and do all those things throughout their career. It was touching to see the beginning of that for him and his mom. It’s something I’ll never forget.”