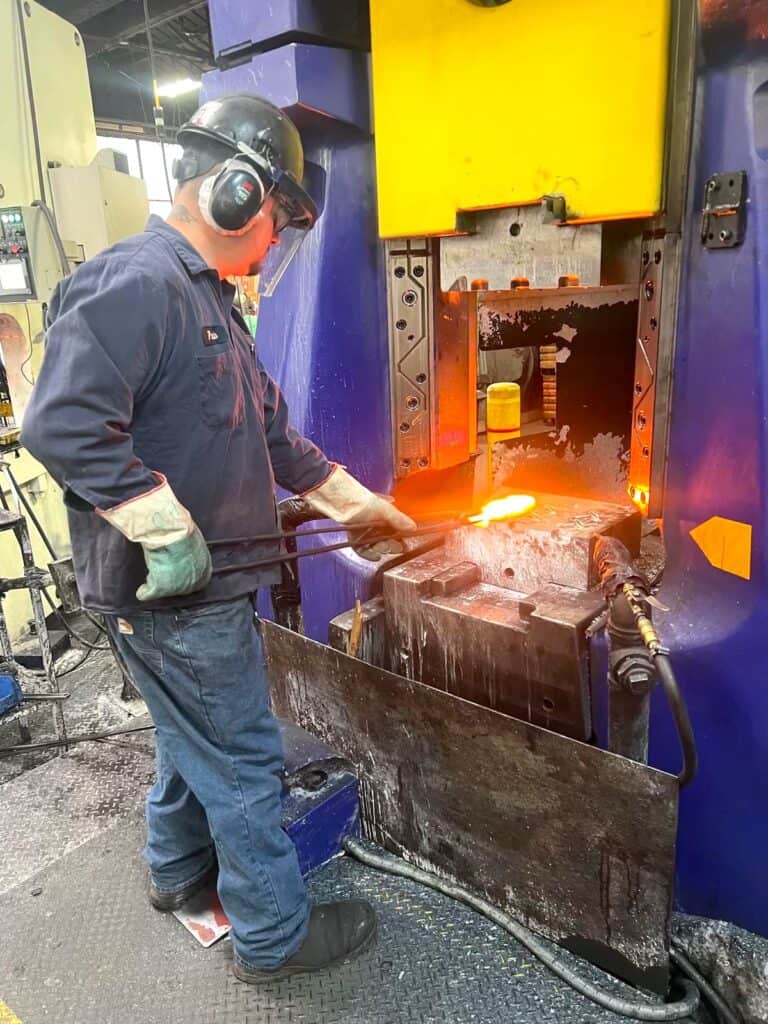
December 30, 2024
GREEN BAY – Green Bay Drop Forge, located at 1341 State St., recently announced it has gone 1,000 days without any lost-time incidents – a milestone in safety, President Bill Hoban said.
“This accomplishment speaks to the daily efforts of our employees who prioritize safe practices and look out for each other, creating a workplace where everyone can return home safely,” he said.
Shannon Young, director of human resources, said 1,000 days is a significant amount of time.
“We’re lucky to have employees who have been with us a long time mixed in with relatively new hires,” she said. “Our long-time employees are careful and understand our process to better teach the new employees we have brought on board. (Our 1,000 days’ achievement) also shows that we have a good training program and a good safety culture in general.”
Young said what makes the milestone even more special is the fact that forging does come with certain risks.
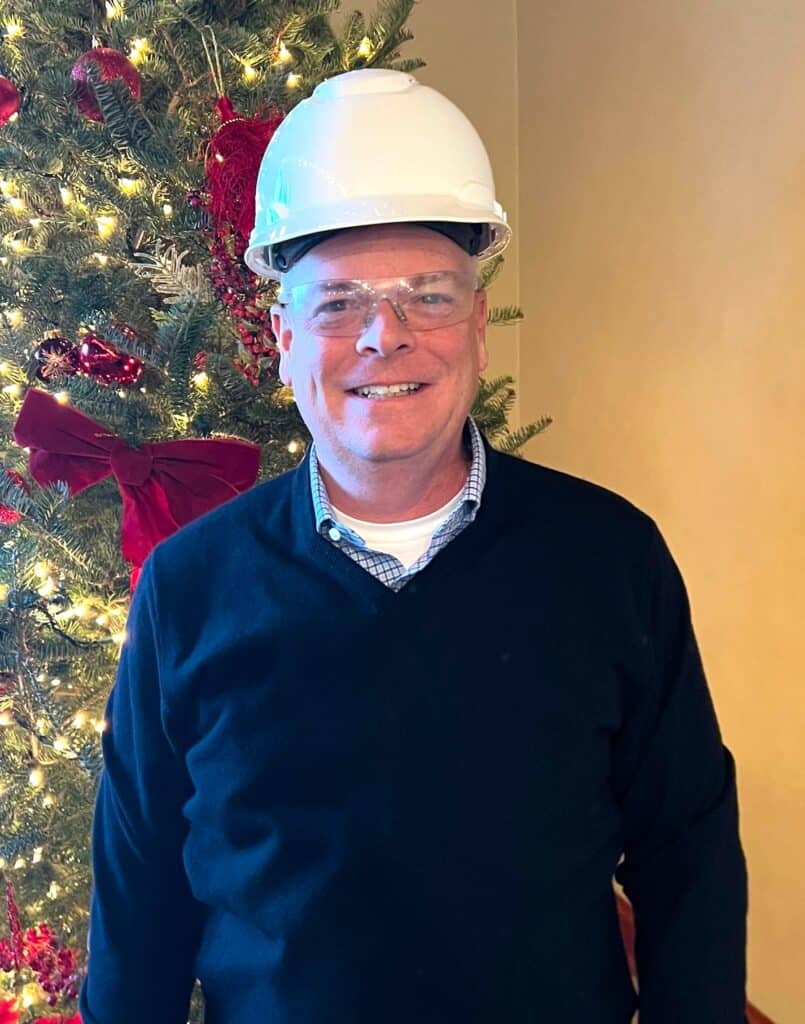
“We’re not only a forging company,” she said. “Forging is one part of our business, but we also have a machine shop. We’re machining, we’re grinding, etc. When somebody hears the word ‘forging,’ they might think that sounds dangerous or scary. Our employees work around a furnace and large pieces of equipment. I think it’s reasonable to say there is some potential risk, like in many jobs. That’s why we stress safety so much.”
Safety, Young said, is a top priority at Green Bay Drop Forge – which starts with effective training.
“Our on-the-job training and our general safety culture are built into our company,” she said. “It’s not just one person enforcing safety measures, rather, it’s everybody holding each other accountable.”
Young said Green Bay Drop Forge also conducts additional training throughout the year.
“This is to make sure everybody is up to date with everything and understands the importance of why we are doing what we’re doing,” she said.
According to the Forging Industry Association, forging is a metalworking process that involves shaping metal into a desired shape by hammering, pressing or rolling it.
The metal is heated to a certain temperature – which varies by metal type – before being worked.
Forging is one of the oldest and most effective methods of metalworking and is different from casting because the metal is never melted and poured.
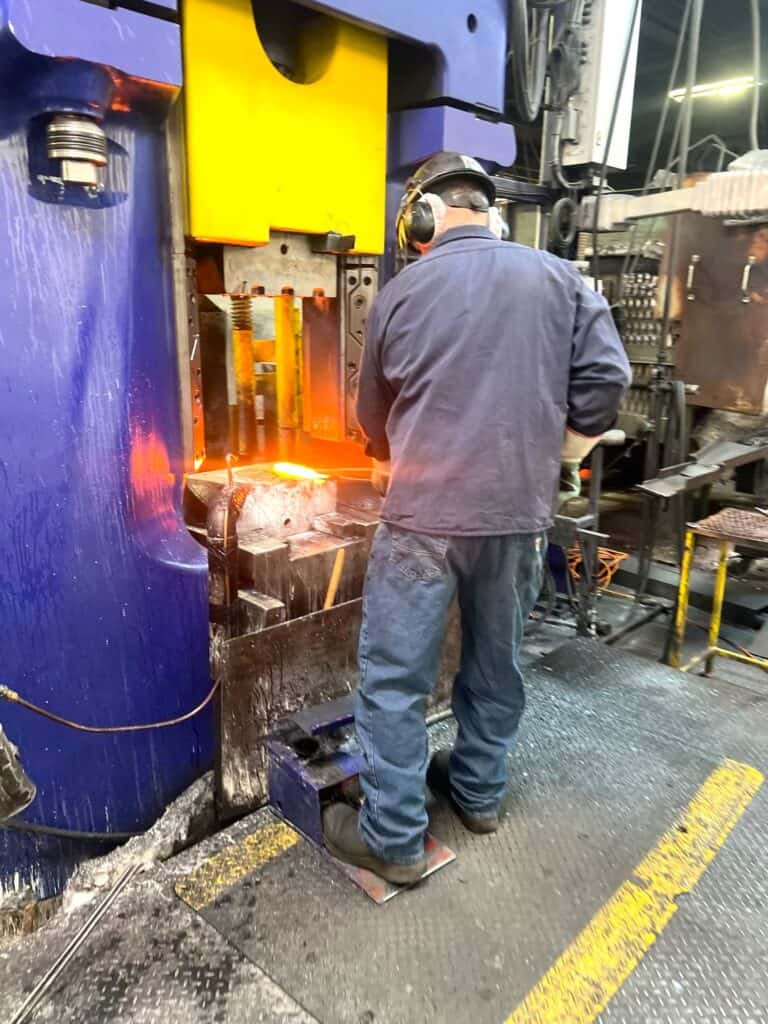
Instead, the metal is kept in a solid state while it’s shaped – which results in a stronger, more durable product.
Young said in simpler terms, the first step in the process of forging is cutting the steel Green Bay Drop Forge receives.
“We’re cutting steel, and then we are heating that steel in our furnaces,” she said. “After the material gets heated, one of our operators forges it by placing (the heated steel) into a die in a process we call hammering. It’s quite a process and art. We create our dies in-house. Dies are what the metal goes into and forms into the piece we desire by applying pressure.”
Young said Green Bay Drop Forge uses drop hammers in its process.
“A newer model we have is a more automated hammer,” she said. “We’re still between our older drop hammers and a more automated hammer to produce the same parts and pieces.”
More on Green Bay Drop Forge
Young said the company’s roots date back to more than 100 years ago.
“We’re a family owned forging company,” she said. “We’re owned and operated by the Hoban family. Bill Hoban, our president, worked alongside his father, who ran Cleveland Hardware for many years, but ownership was eventually transferred to Bill.”
Green Bay Drop Forge, Young said, is seen as a leader in the forging industry – which makes the milestone even more impactful.
“Green Bay Drop Forge actually started as a horseshoe manufacturer,” she said. “Today’s product line in Green Bay… they’re smaller parts and components for a wide variety of industries.”
Those industries, Young said, include automotive, railroad and heavy trucking.
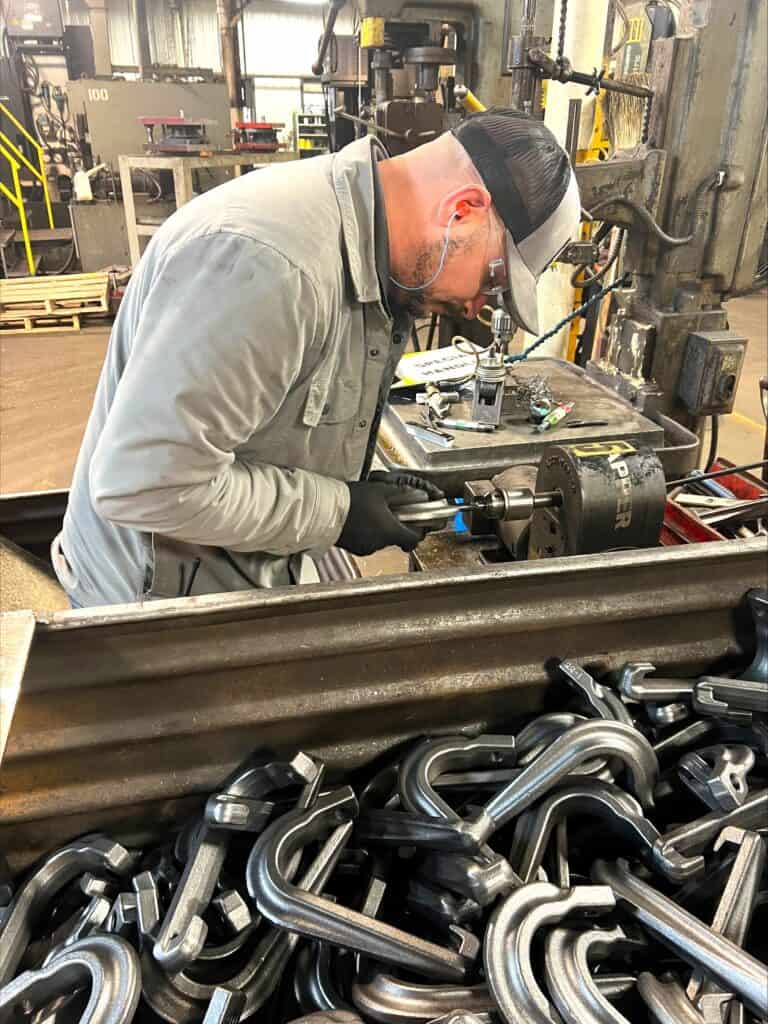
“We also produce a lot of different hand tools, ratchets, wrenches, tools for agriculture, lawn and garden, as examples,” she said. “We also have some assembly work we do as well, producing different locks and things of that nature.”
Currently, Young said there are 72 employees at the Green Bay location.
“We as leaders in the company are continuously looking at current restraints and challenges that we are faced with every day and are in the process of making decisions on what is going to take this company into the next 100-plus years,” she said. “There has been a strong focus on modernizing our equipment and facilities to continue to be a company and employer of choice.”
The future plans, Young said, include an expansion on Green Bay’s far east side.
In addition, she said the expansion will allow Green Bay Drop Forge to bring in more business and employment opportunities.
“It will enhance safety as well,” Young said. “Much of our equipment is manual in nature, so better automation will enhance and streamline our processes, and in turn, improve our safety even more.”