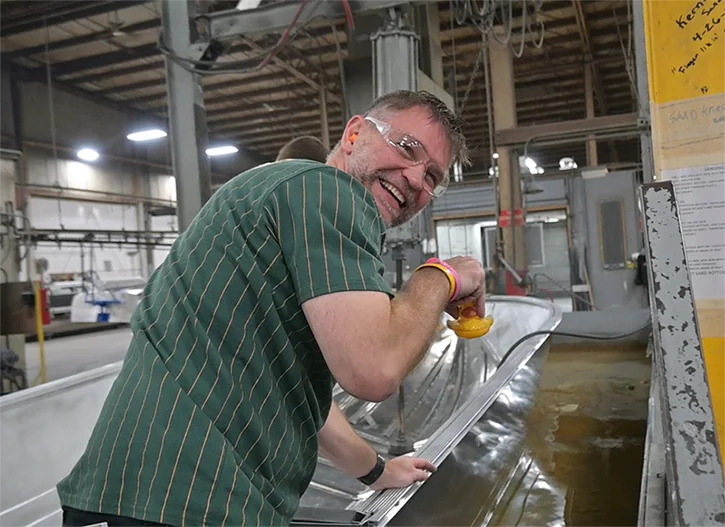
November 29, 2023
HlwQuUr4D6cGILLETT – If you see a fishing boat or pontoon cruising around the lakes, rivers and bays of Northeast Wisconsin, there’s a (minute) chance I had a hand in making it.
In my 15th Just dropping by visit, I headed to Northport Marine in the City of Gillett.
The Oconto County company, located at 39 N. Harding Ave, manufactures and assembles MirroCraft boats and Montego Bay pontoons.
“I’d say we manufacture and assemble about 90% of the boats we put out,” Mike Belongia, president, said. “A few things – like upholstery and flooring – we don’t do here.”
I witnessed the process of making a MirroCraft fishing boat and even took part in a few of the operations.
I had no idea how detailed the process was – which I guess in hindsight makes sense as you don’t want your boat to sink.
With enough horsepower, this Montego Bay pontoon could hit 60 miles per hour. The Business News Staff Photo
Beginning as Mirro Aluminum Company in Manitowoc in 1956, the company offered aluminum fishing boats from 10-19 feet in length.
In 1982, several employees of Mirro Aluminum purchased the business and relocated operations to Gillett.
Northport has undergone a few ownership/name changes over the years, and in September 2012, the company added its own line of pontoons.
Belongia said both the recreational boats and pontoons are distributed all over North America.
When I think of pontoons, I think of a nice relaxing day meandering at a slow pace, but he said that’s not necessarily the case anymore.
“Because outboard motors are bigger and better, a pontoon can go as fast as 60 miles per hour,” he said. “Imagine the shock when you go zipping by a recreational boat in a pontoon going 60 miles per hour.”
A bit into the process of putting together the aluminum hull of a MirroCraft, I tried my hand at putting in a dozen rivets that help hold the boat together – and hopefully, prevent it from leaking.
With safety glasses on and earplugs in place, I grabbed the drill with a firm grip and went to work.
After completing the task, I got a thumbs up from a Northport employee on the underside of the boat saying I did a good job and all rivets were in place.
Rich tries his hand at putting in a dozen rivets that help hold the bottom of a MirroCraft boat together. The Business News Staff Photo
Next, I moved to the sanding deck and buffed out a few scratches.
I then jumped inside a boat that was floating in a tank of water, and armed with an air gun checked for leaks.
The key in this process was holding the air nozzle at an angle close to the rivets and spraying them with a full blast of air.
If there was a leak, I would have witnessed water spraying out from the rivet – fortunately, I saw none of that.
“Every once in a while, we’ll get a boat where none of the rivets leak, but that’s rare,” Belongia said. “If a rivet leaks, we’ll mark it and replace it to make sure it’s good to go.”
Though I only participated in a fraction of the boat-making process, I had a fun time checking Northport Marine out.
I’d like to thank Mike and Tim Allen, vice president of sales, for their hospitality in showing me around the facility.
The company takes pride in what they do, and it shows in the quality of the boats.