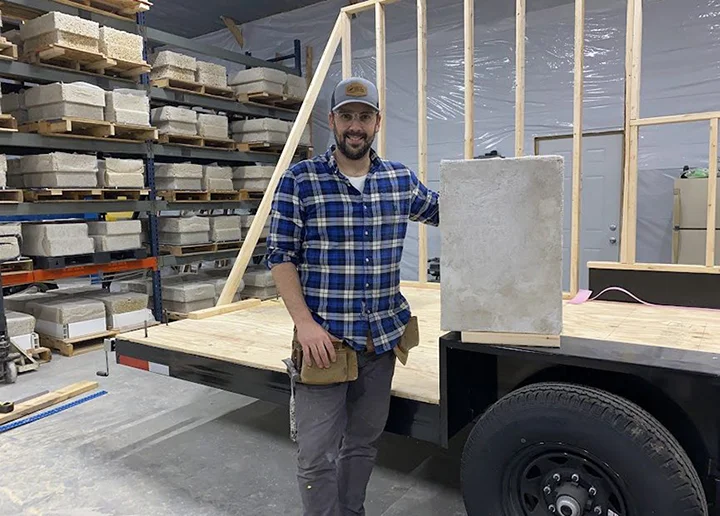
January 9, 2024
WITTENBERG – Oftentimes, the idea or inspiration behind a business stems from a personal experience or connection of its founder.
According to the U.S. Chamber of Commerce, one of the top reasons people start businesses is “to create a solution they wish they had.”
Zach Popp said this is exactly what served as inspiration for him to start Sativa Building Systems in Wittenberg.
“I got into this because of a negative experience with toxic mold in the home we live in,” he said. “My youngest daughter at the time was sick through the whole first winter we lived in the house. She was a newborn and we moved into a new house and community, and we thought ‘oh, she’s catching new viruses. I guess this is typical.’”
It wasn’t until Popp noticed a handful of black dots under the window of his daughter’s window that he said they discovered the entire inside of her wall was covered in black mold.
“That was a north-facing window that created an ice dam and water pooled there for probably weeks and was leaking into the wall without us knowing – there’s no way for us to know,” he said. “When I tore into that wall, the whole inside was covered with black mold.”
This discovery, Popp said, sent him on a journey to find alternative building materials.
“My background in construction, my dad was a contractor and I worked in carpentry for many years – so, I was familiar with what was already on the market,” he said. “But I thought maybe there was something I’m not aware of. Maybe there’s something that is more mold-resistant.”
Sativa Building Systems Owner Zach Popp built an entire tiny home using Z panels. Popp said the tiny home serves as an example of what is possible with hempcrete. Submitted Photo
Popp said his research eventually led him to Europe and a product called hempcrete – which is a combination of hemp shiv or hurd (the inner woody part of a hemp plant stalk), line and water.
“This was around 2010-11,” he said. “At that time, it was only popular in Europe – no one was doing anything with hempcrete here in the U.S. because hemp was still illegal to grow – you couldn’t source it domestically.”
Hempcrete, however, Popp said was everything he was looking for.
“It is mold-resistant. It is pest-resistant. It is rot-resistant. It is fire resistant – it could check every box I wanted to check,” he said.
That being said, Popp said hempcrete is not perfect.
“It’s not load-bearing – so, it’s not as strong as concrete,” he said. “It also takes a long time to dry. Concrete can dry in like a day. Hempcrete can take up to two months.”
Popp said if he was able to engineer out those two deficiencies and figure out how to source hemp affordably – “there’s a real viable business opportunity.”
Then in 2018, the federal farm bill legalized hemp production in the United States.
“I thought it was going to be the future, it was just a matter of time,” he said.
Shortly after that, Popp said he patented a design called Z panel.
“It is essentially a hempcrete block panel that doesn’t need to be load-bearing because it works with standard wood or steel framing – so that’s how I fixed that one deficiency,” he said. “And it’s a precast product, which means it doesn’t have to do any drying on the job site. It shows up pre-dried, which is done at the Sativa facility.”
Though he created the LLC in 2018, Popp said he didn’t hit the gas on the business until 2022.
“(In 2018), I was still balancing my day job – I was doing this mostly on the side,” he said. “Then in 2020, I got the Z panel patented. And then in September 2022, I left my day job and began putting my full-time efforts into the business.”
New to market
Before Sativa can move forward in its business plan, Popp said, it has to go through the code certification process.
“Whenever you are entering the building materials market, you need to demonstrate your product meets building code standards,” he said. “This product is semi-structural, so it must meet code standards.”
What that means, Popp said, is that Sativa has to go through third-party analysis – or the International Code Council (ICC) evaluation services report.
“We’re working through that, and are potentially going to be the first company with a hempcrete product to have an ICC report on file,” he said.
Starting out, Popp said he knew there would be some barriers he’d have to overcome to get the Z panel to market.
Zach Popp said Z Panels were designed with many unique features to make building with hempcrete as simple as possible. Submitted Photo
Part of that, he said, has to do with the novelty of the product.
“If we were to try to enter the market with, let’s say, a new type of roofing material, they would say, ‘okay, this is a new type of shingle, we know how to evaluate this because we’ve evaluated shingles in the past,’” he said. “Because this product is different – it’s meant to take the place of multiple standard building materials. Your wall envelope typically has your sheathing, your insulation, your sheetrock – there are multiple components in a wall envelope – and the Z panel is meant to take the place of several of those. So, there wasn’t anything on file to say, ‘we know how to evaluate this.’”
The first step in the ICC evaluation process, Popp said, was the creation of a new acceptance criteria, which was completed in October 2022.
“I had to do a brief presentation at a quarterly board meeting before the International Code Council board,” he said. “And they had to say, ‘yep, we like what you propose for the acceptance criteria,’ and they did – they accepted it.”
Up next was product sampling and a quality audit.
“They had to do an audit of our quality practices to ensure part of the plan is to produce a consistent product,” he said. “And then there’s the actual testing, and that’s the stage we’re in right now.”
The testing stage, Popp said, is a series of laboratory tests – which in Z panel’s case, is six tests – that the acceptance criteria has laid out.
“So in our case, it’s things like a compression test, a density test, fire resistance test, an insulation test,” he said. “Once those are all completed, an engineer with ICC will put together a report and say, ‘here’s the structural properties of this product, and here’s the applicable applications.’”
Popp said Sativa is working toward having the Z panel used in what’s called one- and two-story, type five, light frame construction.
“So, that’s predominantly almost all of your standard residential structures, and a good majority of even commercial structures – about 60% or more,” he said.
Popp said the Z panel has completed three tests with the final three tests hopefully being completed by the end of February.
“It’s extensive and it’s expensive,” he said.
Funding for the business, Popp said, has come from a handful of seed rounds of fundraising, done partially through his involvement with gener8tor – a Wisconsin-based startup accelerator.
Recently, Popp said Sativa was chosen as a Phase 1 recipient of a state matching grant as part of the latest round of funding from the federal Small Business Innovation Research program.
“I am going through a lean startup course as part of the matching grant program, which is all about customer discovery,” he said.
What’s in store for 2024?
Currently, Sativa is housed in a 2,400-square-foot building in Wittenberg, which Popp refers to as the R&D facility.
“It’s not something I intend to be our long-term manufacturing facility, because my goal is to outgrow this spot quickly, but it’s a new building I built on land I own here in Wittenberg,” he said.
The facility, Popp said, has the necessary equipment to mock-up production, but isn’t, at this point, set up for large-scale production.
“Right now, I’m working on getting some of the production processes down,” he said. “In 2024, I anticipate going into some level of production and building multiple structures (with hempcrete) – that’s my goal.”
Popp said that doesn’t mean, however, that he hasn’t created hempcrete structures already.
“I’ve built tiny homes with the panels so far,” he said. “So, we’ve been able to demonstrate to some degree the sufficiency of the material.”
Once the ICC report is on file, Popp said “there won’t be any more barriers at that point for the average customer, architect, contractor, whoever, to say, ‘let’s incorporate hempcrete into our build project.’”
Zach Popp received a patent for his Z panel hempcrete design in 2020. Submitted Photo
“We’re just waiting to pull the trigger,” he said. “But the goal for this year is to establish some consistent production and to build multiple structures to start getting some traction in the market.”
Even though hempcrete is going through the necessary code tests, Popp said, like with anything new, he knows there will be some hesitancy for being the guinea pig, per se.
“We have a plan to build our own, full home here in Wittenberg using hempcrete – hopefully this coming summer,” he said. “It will be something people can come and feel and touch and experience and see what a Z panel home looks like.”
Popp said one of the barriers to alternative building materials becoming mainstream is “they oftentimes look different.”
“I’ve known about things like straw bale homes or cob homes or Earthships, or whatever – all these cool, but unusual ways to build homes,” he said. “I never saw any viability to them becoming mainstream because no one wants their home to be the one weird home in the subdivision. They are fine with alternative materials, but they don’t want their home to look goofy.”
Because the Z panel allows builders to create “average-looking homes,” Popp said people can’t visually tell the difference.
“But then when you get to talk to them about it, and they see it and can experience the difference,” he said.
Since hitting the gas on his idea and going through the steps to obtain the necessary code certifications, Popp said Sativa has been flying under the radar a bit, “partially on purpose.”
“I knew I didn’t have a product I could deliver to people, and I didn’t have the code report yet,” he said. “I want to build excitement concerning our ability to create product because if people want what we can provide, I want to be able to deliver that to them. So, I’ve purposely flown under the radar a little bit, but as we’re getting closer to completing this code certification process, I’m trying to build awareness.”
Being located in Wittenberg – a village just off Highway 29 made up of a little more than 1,000 people – Popp said he’s well aware “the chance of my customer base coming exclusively from this area is 0%.”
“It’s going to be a national, and probably international product (someday) – so that means I need to be a bit more diligent to now start ramping up our efforts to get the word out,” he said. “(Recognition) doesn’t happen as naturally in a small town compared to if we were located in a more urban area, so you have to put in a little more effort into getting your name out there.”
Popp said most of the materials Sativa will need to source are “pretty much already set.”
“The one variable is hemp,” he said. “We have multiple vendors we’ve bought from and we’ve liked all of them. It’s a matter of economics now – who can produce the most efficiently to give us the best price?”
In terms of manufacturing equipment, Popp said there are still some unknowns there as well.
“There are some things we know we need that are pretty straightforward – and some of those things I have,” he said. “One is a large, industrial ribbon mixer – you need something to mix the hemp to pour it into the forms. But then there are still a lot of variables as far as what truly is the most efficient way to move the product through the production stages. Right now, I can produce product, but I can’t produce it most efficiently. So, there are still some things left to be figured out.”
To get a jump start on that while he waits for his code certification, Popp said he is working with some potential consultants and advisors who can provide him with insight on how Sativa can make some of the manufacturing stages more efficient.
“There are about four stages in the manufacturing process, and two of them, for sure, have some room for improvement in terms of efficiency,” he said.
Business name
Popp said the inspiration behind the name of the company – Sativa Building Systems – was very intentional.
“Sativa is the scientific name for hemp – there’s cannabis indica, which is marijuana, and then there’s cannabis sativa, which is hemp,” he said. “Sativa is one people don’t often associate with cannabis.”
Choosing to name the business Sativa, Popp said, was to intentionally make the distinction between marijuana and hemp.
“Because honestly, when I started this company, and it still lingers to this day – people still like to tie those two together, and they shouldn’t,” he said. “There’s no reason for hemp to be associated with marijuana. So, I wanted to give some homage to the fact it is hemp but without people automatically knowing.”
Sustainability
As an alternative building material, Popp said, people often ask about hempcrete’s environmental impact.
“In a world where there’s more of an emphasis on focusing more on sustainability, I’ve always believed you have to get sustainability to market with superior products,” he said. “That has always been my goal with Sativa Building Systems.”
Now that the Z panel is nearly at the end of its code certification process, Sativa Building Systems Owner Zach Popp said he is hitting the gas on getting the word out about hempcrete. Submitted Photo
Last year, the company obtained a third-party environmental product declaration, or an EPD, to essentially quantify the greenhouse gas emissions of hempcrete.
“Labeling Sustainability (the third-party sustainability consulting firm we worked with) found every panel made captures 1.1 kilograms of carbon equivalents – so it’s considered a carbon-negative product, which is amazing,” he said. “That means you can build a home with hempcrete and you’ll capture more carbon in the process of building than you’ll use. That’s something now we can say with certainty – we have a third-party evaluation that has been done – so, we can say that part definitively.”
Goals for the future
Popp said his overall hope with Sativa is to get hempcrete mainstream.
“I want it to be that when people are thinking about building structures, they at least know we’re an option, and they consider us one of the best-in-class options,” he said. “Will we be the most affordable? Maybe one day. Maybe not. But, I want to at least have that degree of recognition.”
Popp said he also hopes one day that hempcrete will be considered synonymous with Sativa Building Systems.
“We’re not the inventors of hempcrete, but I want to be the company that gets it to the mainstream because we’ve found the most efficient path to do so,” he said.
And ultimately, Popp said, “I want to give people healthier buildings.”
“That’s what motivated me to get into this,” he said. “I want homes to be as toxin-free, as mold-free and as safe as possible. I want to live in a hempcrete home, and I will one day, and I want that for other people, too.”
For more information on Sativa Building Systems and hempcrete, visit sativabuildingsystems.com.