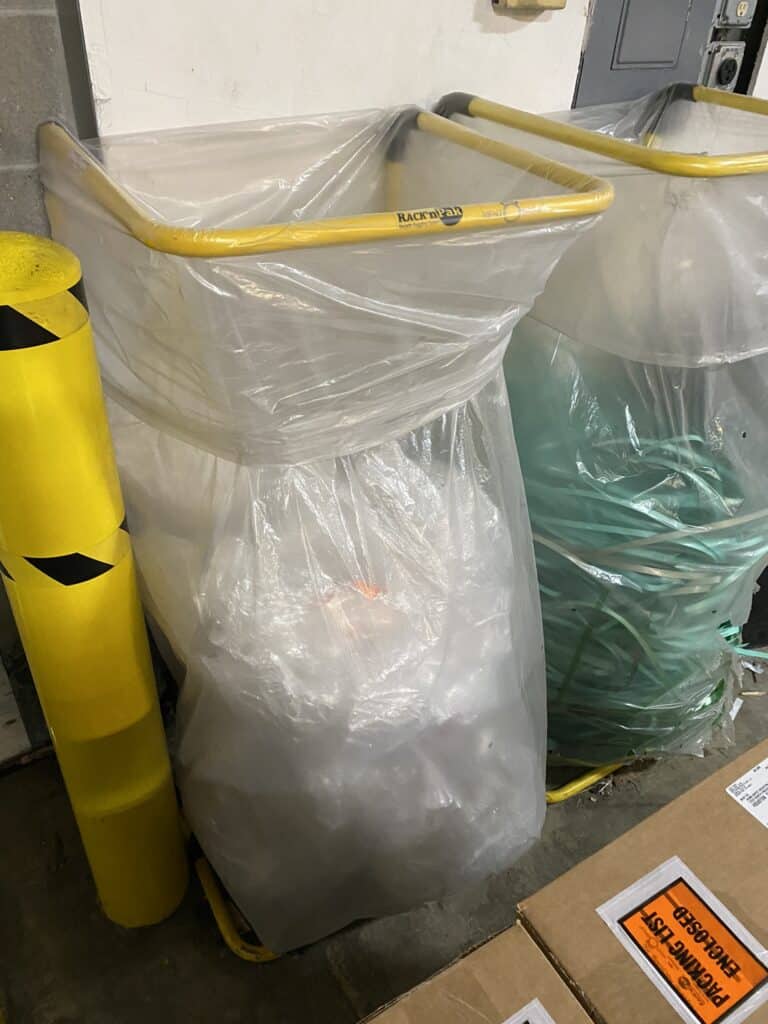
August 26, 2024
SHEBOYGAN – More than 260 million pounds of plastic and counting.
That’s the amount PolyWrap Recycling Inc. Co-owners Jim Theodoroff and Jeff Haen calculate has been diverted from the landfill using their RACK’N PAK® Recycle Bagging System.
“We’ve made a tiny dent, but we have a long way to go,” Haen said. “It’s good to see some companies understand the significant value plastics recycling offers beyond being an environmental benefit. It’s about dollars and cents, which adds up to new and often profitable revenue sources.”
Through its bagging system, Haen said millions of pounds of low-density polyethylene (LDPE) – a thermoplastic polymer that is part of the polyethylene family of plastics – has found its way to recycling centers instead of taking up space at landfills.
“I can understand why companies use LDPE,” he said. “It’s known for being tough, flexible and transparent, so it has a lot of uses. LDPE is also used in agriculture to preserve the freshness of fruits and vegetables and in industrial applications, such as pallet wrapping. LDPE is probably one of the most used plastics worldwide for any kind of packaging there is.”
Theodoroff said many companies are not taking advantage of the other benefit LDPE provides – “it’s recyclable.”
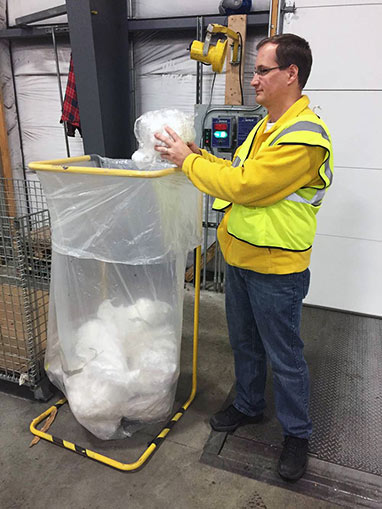
“The reality is, LDPE is convenient and inexpensive for companies to use,” he said. “Plus, the ability to use it within so many different industries makes it a desirable product. It’s great to want to improve the environment, and that alone should drive the desire to recycle. It’s even better when doing so creates a revenue stream.”
Launched in 2015, Haen said the bagging system was designed to make LDPE recycling simple and economical for manufacturers, beverage and food companies and any company that uses stretch film as part of its operations.
Plus, Theodoroff said the bagging system’s size allows it to be conveniently placed in areas where LDPE is commonly discarded.
“Once a bag is full, it can easily be removed and recycled by one person,” he said.
In the United States alone, Haen said, it’s estimated that three million tons – or six billion pounds – of LDPE is produced yearly.
It’s been reported that only around 5-7% of LDPE around the globe, he said, makes their way into the appropriate recycling stream.
“Unfortunately, that percentage hasn’t changed in 15 years,” he said. “It’s not like we’re making progress. There’s a lot of online presence trying to get LDPE recycled more, but for some reason, it’s been a material that has been a real struggle to get companies to say, ‘hey, let’s not throw this away – let’s get this recycled.’”
The other 93-95% of LDPE not recycled, Haen said, is landfilled, which he suspects is the result of a lack of awareness or time.
“Whichever it is, they are wrong,” he said. “And that’s what our mission revolves around – to show businesses the numerous benefits to recycling LDPE and how doing so not only improves the environment but also the bottom line. Not only that, but it can also be done easily and in a manner that improves daily operations.”
How it started
Haen said the story behind how the bagging system began is simple.
“We went into facilities and saw how inefficiently LDPE was being collected and bailed for recycling,” he said.
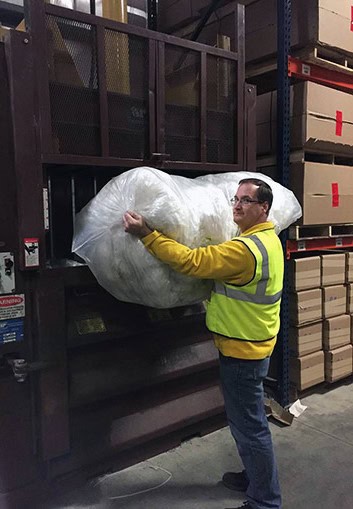
From there, Haen said they began brainstorming different directions they could go.
“We knew most companies have a six-inch vertical baler, so we tried to maximize what we could do using that information,” he said. “We created the bag first and the rack next – some reverse engineering.”
How it works
Most companies not utilizing PolyWrap’s bagging system, Theodoroff said, use Gaylord Boxes.
A Gaylord Box is a large, heavy-duty cardboard box that sits on a pallet and is used for shipping and storing materials.
They are often rectangular or octagonal in shape and can have up to three layers of corrugated material.
“Using Gaylord Boxes is not the most efficient way of collecting LDPE,” Theodoroff said. “They take up floor space, and then someone has to forklift the boxes to the vertical baler and then have an employee reach into the box, which can get difficult toward the bottom. When you grab LDPE (from the Gaylord Box), you’re only grabbing a pound or two at the most (at a time), then it’s on the floor, which becomes a hazard for an employee to trip on. Then you’re moving that one-pound bundle into the baler – it’s inefficient.”
Haen said the PolyWrap’s rack-and-pack system is meant to “totally replace the use of Gaylord Boxes.”
“Our rack essentially creates a new collection point,” he said. “With replacing the Gaylord Box, you’re not having to empty that box. So essentially, you fill our bags with as much material as a Gaylord Box can hold. You fill the bag to the top, and a simple knot on the top ties it off, and then the bag goes directly into the baler. There’s none of that labor of having to load the baler. You push the bag in, hit the button to compress it and walk away. So there’s a huge labor savings on how long it takes to create a bale of material.”
PolyWrap’s collection bag, Theodoroff said, has holes in it, which helps release air when compacted.
“We figured the system would increase bale weight, which it did,” he said. “Then we continued to work together and did prototypes. We have patents on the rack and bags – the rest is history.”
Theodoroff said the bagging system – which is stationary – also increases bale weight, which makes it more economical for companies to recycle.
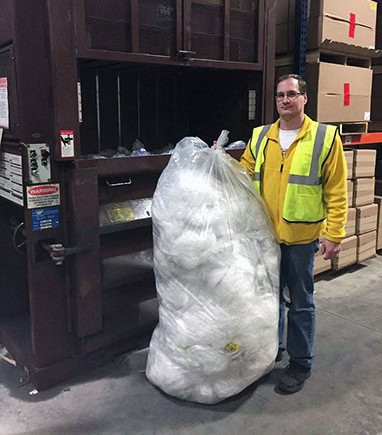
“With the rack-and-pack system, you increase your bail weights by 10-20%,” he said. “If you’re bailing this stuff and then selling it off to someone, you maybe get 800-900 pounds. With our system, you can increase it to 1,100-1,200 pounds. That’s important because you’re maximizing that semi-truck (load) that comes to pick it up.”
Theodoroff said the bagging system can recycle anything that is a flexible plastic.
“We have companies that recycle the green banding that goes on to bail, companies that recycle bubble wrap and different kinds of foams,” he said. “We have companies that use it for Styrofoam. Anything that isn’t severely serrated that would puncture a normal bag can easily be collected.”
Offering support
Though PolyWrap doesn’t specifically recycle the LDPE once it’s collected – it just manufactures the bagging system – Theodoroff said he and Haen help “connect people to people.”
“We have the knowledge of saying, ‘okay, let’s say you’re in eastern Wisconsin, we can help you get rid of material and help you set up a program,’” Theodoroff said.
Theodoroff said PolyWrap ships five days a week throughout the United States and Puerto Rico.
“We have connections even in Hawaii and Alaska,” he said. “We want to increase that plastic collection and make the earth a little better place.”
Theodoroff said PolyWrap is even willing to let companies try out the system before they buy to see how it works.
“One of our taglines is, ‘there’s no gimmick about it,’” he said. “You can try the system for 30 or 40 days. If you have 20 Gaylord Boxes, you’ll get 20 rack-and-pack systems. If it doesn’t work, you can ship them back.”