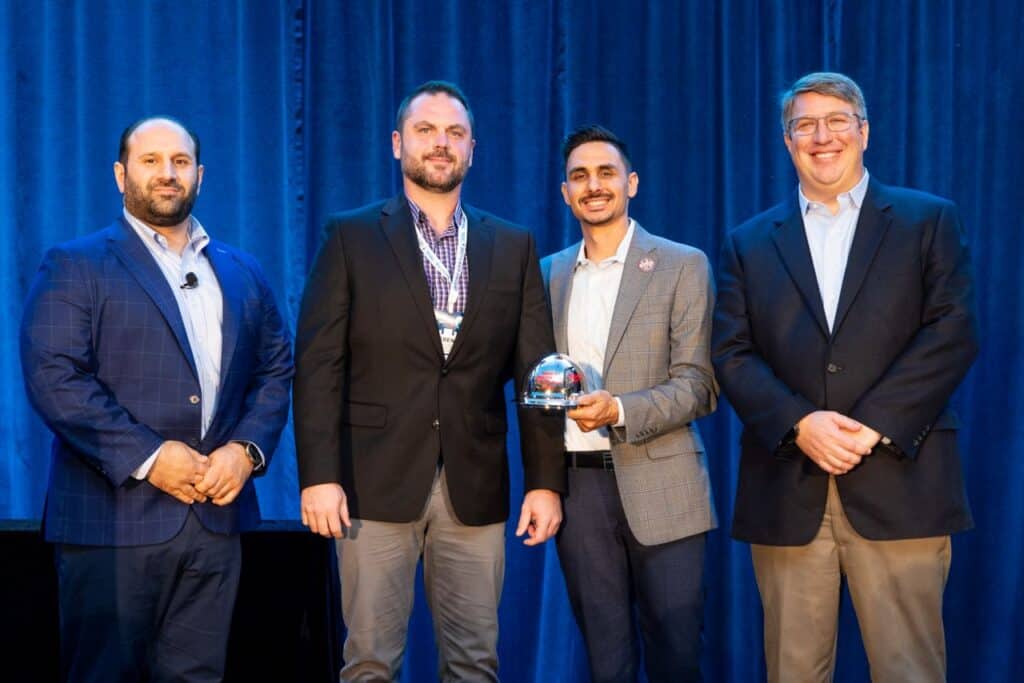
February 10, 2025
KAUKAUNA – Bassett Mechanical’s Director of Safety Sereno Steindl was recently recognized as the 2024 Safety Professional of the Year by the Mechanical Contractors Association of America (MCAA) and Milwaukee Tool.
Steindl – who joined Bassett in March 2022 – said he’s focused his career on safety in manufacturing for the past decade.
“Safety has always been extremely important to me, regardless of what project I’ve been on or what I’ve even done in my personal life,” he said.
According to MCAA’s website (mcaa.org), the safety award is “presented annually to a mechanical industry safety and health professional who helps their company achieve an exceptionally high degree of safety excellence.”
One way Steindl said he’s assisted Bassett in achieving “exceptional safety” is through its ‘Are You Protected?’ initiative – of which he said he believes is one of the many reasons he stood out to the MCAA/Milwaukee Tool awards committee.
“That (initiative) really came from my background of starting through the trades,” he said. “I started with a mechanical contractor when I was 18 (years old). So, the majority of my professional career has been in the field, and with that time in the field, I, at times, had frustrations with what I call the ‘typical safety person.’ I always felt that there needed to be more of a partnership.”
Partners in safety
While working in the field, Steindl said he was often approached by “a safety person” who would inform him of when he was being unsafe.
“They would come up to me and say, ‘Well, you can’t do it that way,’” he said. “I always felt like there was a piece missing on the other side of it, because I have no problem not doing it that way or doing it the right way, but how do I do that? What tools do I have available to me?”
Bassett’s ‘Are You Protected?’ initiative, Steindl said, answers those questions by creating a central location for employees to access information on how to safely operate within their positions.
“The intent was to provide our associates with information on related equipment to protect themselves,” he said. “That’s really taken on a life of its own, if you will. (The) Are You Protected brand is (used as) internal branding now. It’s really sparked a lot of creativity on our team.”
Steindl said he believes the initiative has made a big impact on Bassett Mechanical over the last couple of years.
“We’re giving them that basic information with real solutions,” he said. “Whether it’s through the tools that are provided, or equipment or even through our weekly communications (sent) out to the organization.”
The success of Bassett’s ‘Are You Protected?’ initiative, Steindl said, is credited in part to the company’s willingness to be partners in safety with its workforce.
“You should be able to rely on your safety department not as the safety police or the safety cop or the safety authority – they should be a safety partner,” he said. “We have really tried to engage with our workforce with that type of thought process of partnering with them.”
Prioritizing safety from the top, down
To create a safe manufacturing work environment, Steindl said safety should be a priority regardless of one’s position within a company.
This, he said, includes leadership’s consideration of safety when making decisions on what projects to take on.
At Bassett Mechanical, Steindl said leadership will review a customer’s policies and procedures to determine whether safety is a similarly prioritized consideration.
This, at times, he said, means leadership will walk away from projects that don’t align with their safety objectives.
“We’ve done that, and I commend our leadership team for being able to make those hard decisions,” he said. “That says a lot to our workforce if we are willing to turn down a project because (it does) not align with our safety standards. That’s a big deal to me. That makes my job a lot easier.”
Taking control of the company’s safety by choosing projects that align with its priorities, Steindl said, creates real change outside of simply reporting reduced rates of injury.
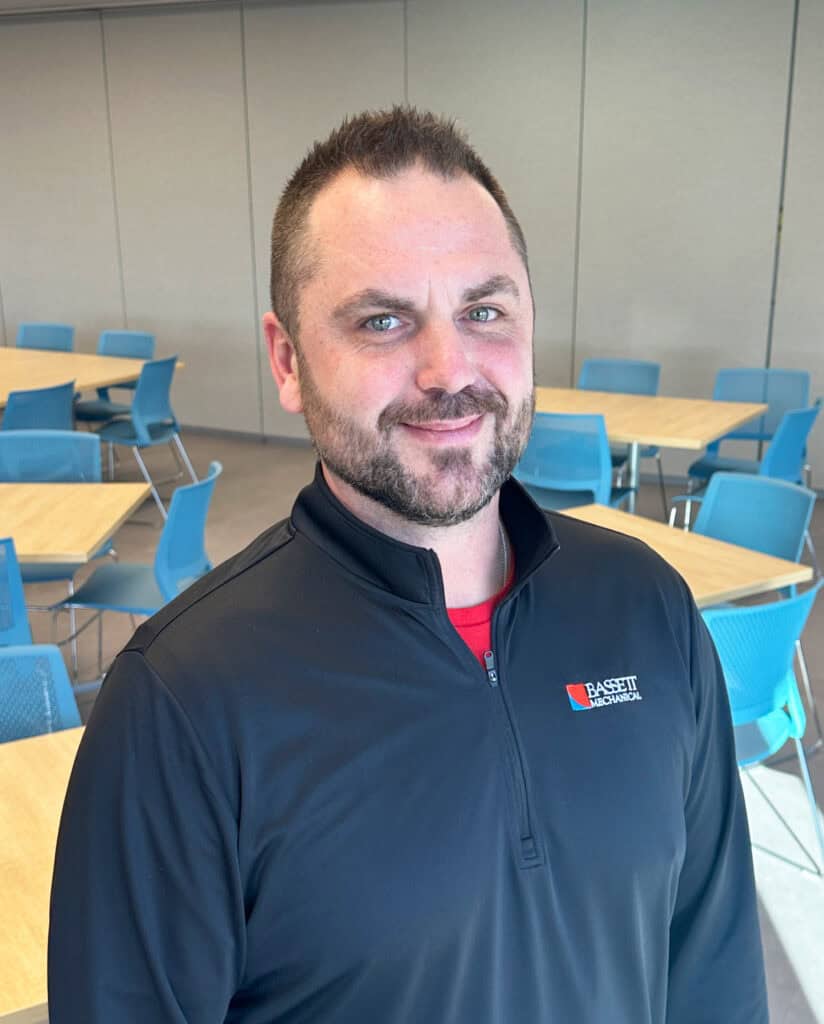
“It’s easy for a safety professional to sit here and say, ‘We reduce rates, and we reduce injuries,’” he said. “But I think if you’re able to step back and not be so hyper-focused on the numbers, all the really important things are happening during normal business operations. Are we, the safety (team), being included in project planning? Is leadership engaged with our frontline associates? Are we reviewing current customers to ensure that they align with our safety requirements? Are we doing the same for our subcontractors? And I think if you can answer ‘yes,’ then you know that is where the real impact is happening.”
Ensuring safety, Steindl said, involves more than just planned initiatives and requires a breakdown to the “basics.”
“We aren’t trying to invent new things here when we have enough to do, but are we doing our basics the right way?” he said. “Are we making sure that we have our training requirements covered? Are we providing impactful solutions and communications to our organization?”
Steindl said over the past few years, Bassett has “completely revamped” its training program – providing tailored training schedules to associates in each trade that exists within the company, as well as enhancing communication to those in the field.
“Every week, we send out our ‘Toolbox Talks,’” he said. “At Bassett, that is our main communication out to our associates here, and we provide very specific, targeted, sometimes even awareness-level-type training through those weekly communications. So, it’s been very pointed with how we are engaging and communicating with our associates here.”
The impact of safety
Because safety is a two-way street between leadership and associates, Steindl said there are liability concerns to be shared with both the company and its employees.
“There’s a lot of liability that comes with this,” he said. “That translates to some big dollars, and at the end of the day, yes, of course, we need to protect our people – but if we aren’t protecting our companies, we won’t have a place for our people to go.”
Steindl said protecting the company and protecting its people are both top priorities for professionals in the field of safety.
“You are managing both sides of a business,” he said. “You are managing the people of it, the human aspect – our frontline associates. But then, of course, the other side of it is the business side, and those two are equally as important. So, at times, there can be some very hard conversations that need to be had and hard decisions to be made. But if you are always honest with both sides of that, and you hold true to what you believe in and are black and white with the rules and regulations and requirements that are out there, you’re usually going to come out ahead.”
Though maintaining a safe workplace is not a new revelation in the manufacturing industry, Steindl said there has been increased awareness around it recently.
“We are certainly in a new way of doing things,” he said. “I think there’s been a shift in society, at least over the last decade, of stuff that maybe wasn’t accepted prior and it is now. I think that there is a realization to the cost of injuries that necessarily wasn’t there – insurance costs, comp costs – that has all certainly skyrocketed.”
Though skyrocketing costs haven’t been the primary driving force to increased workplace safety, Steindl said they certainly have had an influence.
“Owners and organizations, I would say, kind of stepped back a little bit and recognized that it’s not necessarily about getting it done as fast as we can, because if we aren’t getting it done as fast as we can safely, we aren’t getting it done at all,” he said. “I know it sounds kind of cheesy, but I think culturally, we have certainly had a positive shift toward understanding the importance of safety and the impact that it can have on business.”
A personal endeavor
Though his career in safety began in the field, Steindl said his passion for it began when he was a child.
“A very close person to me passed away when I was about nine years old, they died in a motorcycle accident,” he said. “I remember the detectives coming in late at night to our home and letting us know that this person had passed, and this is all speculation (because I was) nine at the time – but I remember them saying if he would have had a helmet on, he probably would have lived. And that always has stuck with me through the years.”
Steindl said the combination of that experience and his time enduring unsafe conditions while working in the field fueled his desire to promote the importance of workplace safety.
“I’ve always seen safety as something incredibly important in my life,” he said. “Through my years of working in the field and just having the experiences I’ve had – I mean, I’ve suffered injuries myself, and I’ve seen the devastation of that and experienced that in my own personal life and with very close friends – I always felt drawn to the world of safety.”