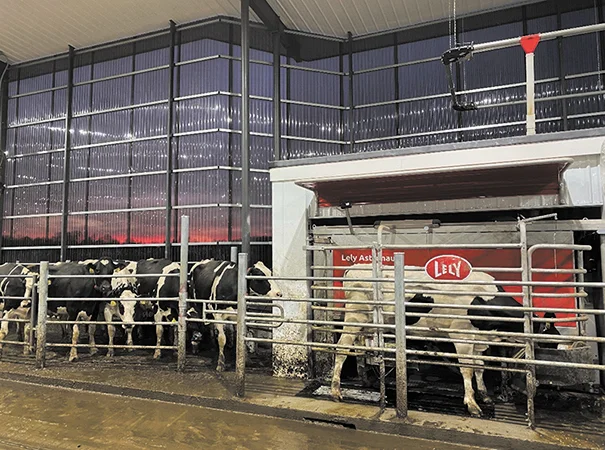
December 12, 2023
APPLETON – For the last 72 years, Fox Valley Technical College (FVTC) has brought students and members of the community to farms throughout Wisconsin to get an inside view of what the farming industry looks like, and how things change and evolve each and every year.
This year, FVTC’s 72nd farm tour looked a little different.
The technical college hosted the event right on campus, with a virtual tour of two farms: Strassburg Creek Dairy (N7339 Regina Road in Wittenberg) and Wayside Dairy, LLC (7937 Stone Road in Greenleaf).
“Some of you may remember the days of the tours with the bus rides and the farm stops, the wonderful meals and the camaraderie,” Sara Maass-Pate, instructor of farm business production management at FVTC, said. “With today’s challenges, trying to secure bussing and everyone’s busy schedule, we’re looking to take the tours to you, where it might fit you best.”
Maass-Pate and Jeremy Hansen, an instructor of farm business production management at FVTC, toured Strassburg Creek Dairy and Wayside Dairy, respectively – and shared those tours through video presentations.
During the tours, both farms highlighted the evolution of technology in farming, and generational ownership – both prevalent topics in the realm of agriculture today.
Farming and technology
The virtual tour started with Strassburg Creek Dairy, where members of the farm – Jeff Strassburg (fifth generation) and Jacob and Alyssa Strassburg (sixth generation) – spent a great deal of time discussing the integration of technology in dairy farming.
The dairy farm, Jeff said, milks about 650 cows in the milking parlor and 750 cows in the robot barn.
“(We’re) milking three times a day in the parlor, and 2.8 to 2.9 times in the robots,” Jeff said.
Strassburg Creek Dairy started out by adding nine Lely A-5 robots – and then later added three more.
?Jacob said the purpose for the robots was to “decrease labor.”
“We’re basically milking 500 more cows with the same amount of labor,” he said. “We were able to do it without really adding any other people, and just maintaining the people we’ve got.”
The robot milkers take about a third of the labor as the milking parlor, he said.
The Lely A-5 machines each bring in anywhere from 5,700 to 5,890 pounds of milk every day.
“It’s a free-flow barn,” Jacob said. “The cows can just come and go as they please, they can eat, milk, sleep or drink water any time of the day that they want.”
When the Strassburg family first started working with the robots, Jacob said one of the things they discovered is that the teat length and girth of first-time lactating heifers can be an issue.
“A lot of times, if we have a heifer that comes in and we have trouble with the robot attaching to her, she goes back to the parlor,” he said. “And that’s the advantage of having the parlor alongside the robots.”
Jeff said Strassburg Creek Dairy has two Grade A licenses – one for the robot barn and one for the parlor.
The evolution of technology in the dairy industry, he said, also benefits the heifers themselves, both for comfortability and for their health.
“There is a laser that handles the teat cup and post treatment,” he said. “But then there’s a 3D camera over top of the cow that looks at her hips and pins as she moves forward and backward in that box, the arm will actually follow her according to that camera.”
Between the robot barn and milking parlor, Jeff Strassburg said they have about 1,400 cows. Photo Courtesy of Strassburg Creek Dairy
From collars that the cows wear, Alyssa said the robots are able to provide more information about the heifers, such as the milk weights.
“The robot takes milk temperature, conductivity and all their activity – rumination, eating minutes, and that goes to Lely’s program,” she said.
Cows in the parlor also wear a collar, this time through Afimilk, another dairy technology company, which Alyssa said tracks similar measures.
“The Afi system is taking milk weight, conductivity, rest time and putting that into their system,” she said.
Each morning, Alyssa said she and other herdsmen will check the system reports for any deviations and then go check in on those specific cows.
“They’re very accurate,” she said. “With the collar, we’ve been able to see the eating minutes, so a lot of times if a cow is going to get sick, where they don’t feel like eating, they’re not going to eat as much, that will show as one of the first signs – that the rumination activity is down. Then we can go check them and find them before they really get visibly sick.”
Another important aspect of the cows’ health is keeping their feet clean, Jacob said, which is why Strassburg Creek Dairy decided to install an automated footbath system.
“We push cows through a foot bath once a day, every day of the week,” he said. “We find that our foot health is very good, we hardly ever have to trim a cow in this barn. It helps them stay mobile, and helps them get to the robots a lot easier.”
New technology at Strassburg Creek Dairy has also played a role with the farm’s calves.
During the summer, the Strassburg family built a calf barn facility with six automated calf feeders – where the milk is piped six feet underground from the milking facilities – for their 120 calves.
“It was easier to feed calves, easier to take care of, and also do a better job of monitoring,” Jeff said. “I can see what every calf has drunk for the last 72 hours. The calves can go up (and) get meals throughout the day, up to four times a day. It would be way too much to ask for an individual to have to come and feed the calf four times a day. We’re really training these calves in this new facility to go get their own meal when we’re not here.”
As Strassburg Creek Dairy looks to the future of the dairy industry, knowing there will be a continued evolution in technology, Jeff said, “we’re always striving to do a better job.”
“That’s the number one goal – to do better for our family, for our farms, for our community, for our environment,” he said. “The next step of technology, for us, is probably starting to look at some kind of gas digester, maybe sand separation.”
Generations of perseverance, and then some
At Wayside Dairy LLC, Dan Natzke said his family knows a thing or two about perseverance over its 160-year history.
“In 2001, we had a major barn fire,” he said. “We were milking 400 cows at the time, and the fire pretty much wiped out the milking center, the feed center and the shop. We couldn’t milk cows here anymore.”
This, Jeremy Natzke (Dan’s son) said, left the family with two options: call it quits, or push through and rebuild.
“We both looked at each other and said, ‘we want to rebuild,’” he said. “‘We want to keep farming. It’s a good way of life.’ Ever since we decided that, we’ve gone forward.”
Now, Wayside Dairy has 2,300 cows.
“The fire back in 2001 was one of the worst days in our history, but it was also one of the best days in our history because it gave us an opportunity,” Dan said.
The fire wasn’t the only time that the family at Wayside Dairy would have to make a big choice.
When Wayside Dairy experienced a fire in 2001 that left them without a milking center, feed center and the shop, Dan and Jeremy Natzke said they knew they wanted to rebuild. Photo Courtesy of Fox Valley Technical College
The family-owned business recently made the decision to bring on a non-related partner, Jesse Dvorachek.
“We’re not a small farm – but – we’re just different families working together,” Dvorachek said. Different families working together, Dvorachek said, “is the future.”
“If we want to keep dairy in Wisconsin, there’s going to be some out-of-family people coming in because we specialize in certain things, and not every farm has those kids that want to come back and do this,” he said.
When it comes to future generations running the family farm, Jeremy said it’s too early to tell because the kiddos are young.
“My wife, Heather and I have three children, they’re 13, 11 and eight,” he said. “And then my sister, Jenna and her husband, Jacob, have two children, they are 11 and seven… Jesse has four children, so we’ve got some possible candidates for the next generation.”
As Wayside Dairy continues to move forward, Jeremy said they too are looking at the best ways to keep the cows healthy.
The addition of biosolids – organic materials that are a result of wastewater treatment of sewage – he said has been more to manage, but is worth it to keep the cows healthy.
“They lay in a free stall… and it’s always bedded and groomed for them,” Jeremy said. “We put in new bedding every day with the biosolids just to keep it fresh on the top, keep it dry, keep them comfortable and keep them laying down.”
Wayside Dairy is also in the process of installing a methane manure digester, which will produce natural gas and be transferred directly into the gas line.
“We’ve been ready to go for quite some time,” Jeremy said. “Things don’t move real fast in that area… and it probably will be April before we break any ground… In the digester business, it’s much slower.”
To learn even more about the advances in the farming industry, visit Fox Valley Technical College’s YouTube page.