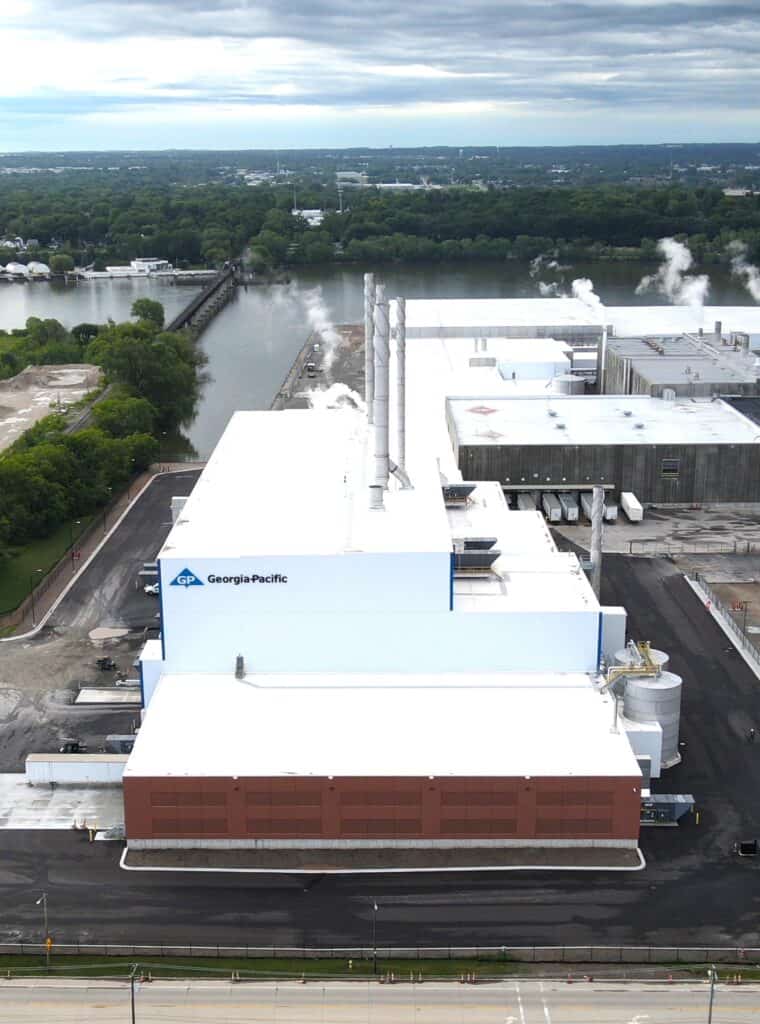
October 7, 2024
GREEN BAY – Almost three years in the making, Green Bay’s Georgia-Pacific (GP) mill (1919 S. Broadway) recently celebrated the grand opening for its $550-million expansion.
The 600,000-square-foot expansion will exclusively manufacture Brawny paper towels and other premium private-label brands for the retail market.
“What a great day for Georgia-Pacific, the Green Bay community, Brown County and all of Wisconsin,” Christian Fischer, president/CEO of Georgia-Pacific, said. “We have five facilities in Wisconsin – about 1,900 people employed – and 1,700 of those work in Green Bay.”
Fischer said GP has invested about $1.2 billion in its Wisconsin plants in the last 10 years.
“We invest so we can continue to produce the products we manufacture to give our customers and consumers better alternatives – that’s what we’re about,” he said. “Our products are in hospitals, entertainment venues, hotels and a lot of other places. We’re proud of the products we make.”
Dean Wesolowski, the expansion’s operations manager, said GP could have picked any one of its other 150 mills in the country, but thinks the company chose Green Bay for several reasons.
“Location was part of it, but I think mainly, this facility and the people who work here have a history of delivering on investments,” he said. “I think the culture and work ethic of our people had a big part of why GP invested in Green Bay. I think this investment sets up our facility for another 30-40 years.”
Wesolowski said GP hasn’t started a new paper machine in Green Bay in 30 years, “so it’s a big deal.”
“This paper machine building used to be a parking lot, and our converting building by the river used to be piles of coal,” he said. “To see the transformation of this facility over the past three years has been amazing to watch. We built a lot of relationships through this project, and everyone worked together. Things didn’t go perfectly – we had supply chain issues, lead time issues, etc. – but we got it done.”
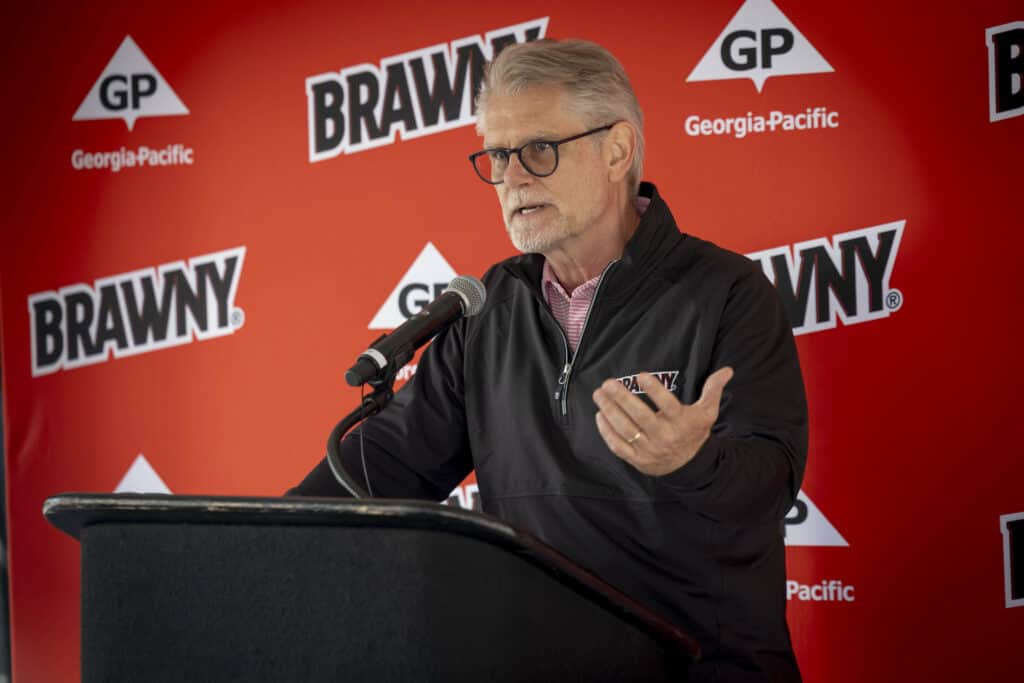
Though Wesolowski said staying on time was a goal, safety was his top priority.
“I said early on, ‘this will not be a successful project if we have a significant injury or heaven forbid, a fatality,’” he said. “The team was proactive in keeping people safe. We didn’t have that significant injury, and I’m proud to be a part of that.”
Wesolowski said the quality of work on the project was “incredible.”
“If everything went well, we thought we could have the paper machine/building up and running by the third week of June 2024,” he said. “We started up this paper machine in the third week of June. We had contractor partners on this project who were competitors outside of here, but on this project, they were teammates. They shared information, resources and people – that’s almost unheard of. That allowed us to start on time.”
A vision in the making
When the Green Bay plant celebrated its 100th anniversary in 2019, Fischer said he had an inkling an expansion might take place, but he couldn’t disclose any details at that point.
“I remember standing (in Green Bay) May 2019 for the 100th anniversary of this facility,” he said. “As I came up to speak, snowflakes were falling. Some people were already discussing putting this new paper machine here at that time. I remember people asking me, ‘can we give people any indication about this new machine?’ We were thinking about it, but it hadn’t been approved yet, so we couldn’t really talk about it.”
Fischer said in hindsight, it may have been the best decision to keep it temporarily under wraps.
“A few things happened between 2019 and 2024 – a little thing called COVID-19,” he said. “Here we are five years later, and the thing is here. That’s a testament to the people working on the project. It takes a village to get things done, but this project wasn’t just about a local village working together – it took the world. We had suppliers from as far away as Finland working on this.”
More on the expansion
John Nundahl, vice president of manufacturing for GP’s Green Bay operations, said the expansion included a new paper machine, three new converting lines and a lot of associated equipment to go with it.
“The expansion combined with the rest of Broadway brings us to six million square feet of manufacturing space under one roof,” he said. “The project also included a high level of technology and automation, which equates to fewer operator touches, improved safety and increased productivity.”
Nundahl said the expansion also created more than 100 new GP jobs.
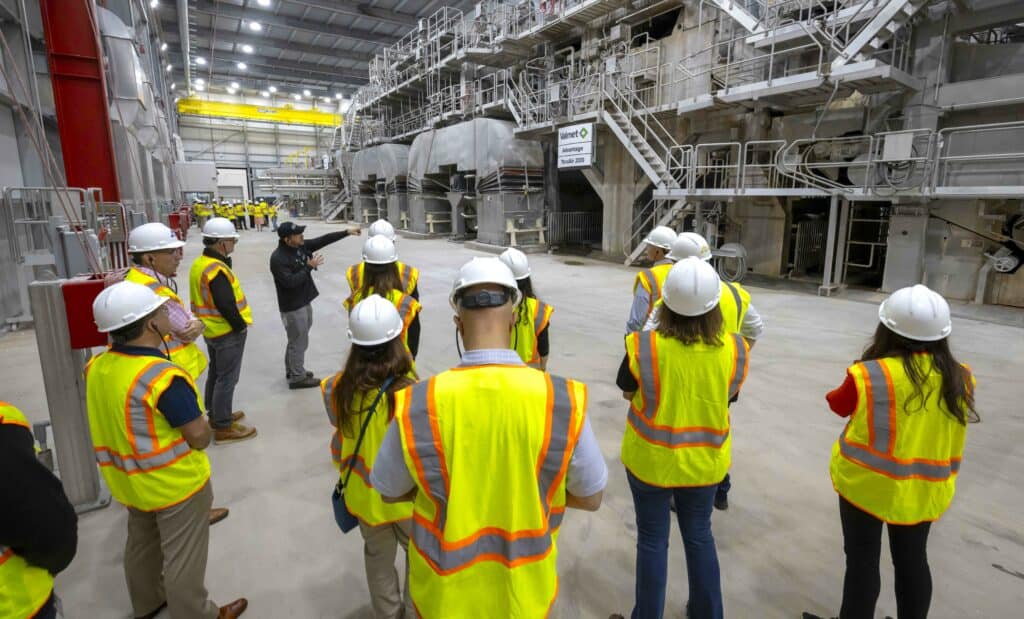
“We’ve got most of the jobs filled, but we still have a few more to add,” he said.
Wesolowski said GP is hiring technicians to operate the equipment, engineers, maintenance workers and supervisors.
During the span of the project, Nundahl said there were more than 2,000 contractors and design partners who worked with GP.
The Brawny way
Nundahl said the system as a whole will make millions of cases of Brawny paper towels.
“It’s a major competitive advantage for us,” he said.
To make “those millions of cases of Brawny paper towels,” Amanda Earley, brand director for Brawny, said a lot of teamwork is needed.
“The new facility is state of the art, which allows us to bring premium, high-quality paper towels to our consumers,” she said. “I don’t know specific numbers, but I know the demand for quality paper towels continues to rise, and this facility helps with that growing demand. Brawny is known for strength and durability, and the mix of a strong community along with great teamwork has helped this project come to fruition. I’m by no means a paper expert, but I believe our teamwork and strong communication helped greatly.”
Earley said she’s had the chance to tour the facility and came away “very impressed.”
“This is a fantastic facility – a lot of care went into it,” she said. “When I first toured the expansion, there was a ‘wow’ factor. If you haven’t seen a paper machine in operation before – especially through air drying – it’s really impactful to see how much goes into making a product people use daily. The machine is gigantic and impressive.”