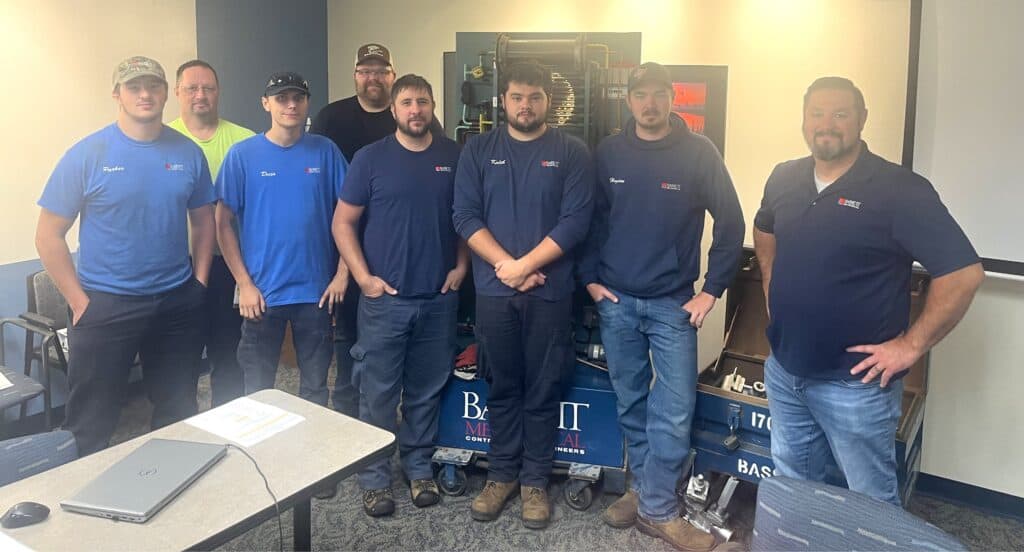
December 2, 2024
KAUKAUNA – Patty Van Ryzin, chief human resources officer, said Bassett Mechanical, a full-service mechanical contractor in industrial refrigeration, has always been known as a leader in the industry.
She said it’s one thing to be known as a leader, but it’s a whole different challenge guiding the next generation of employees.
To combat losing the knowledge from its long-tenured employees, Van Ryzin said Bassett is focused on ensuring that expertise was passed down to its younger employees by starting a training academy.
“We don’t want to lose anything and want to make sure we continue to give the customers what they need,” Van Ryzin, who has been with Bassett for 34 years, said. “When I first started at Bassett, I was pretty much a jane-of-all-trades and did anything I had to, but during the last year or two, one of the things I’ve focused on is getting this training academy going.”
To begin, Van Ryzin said Bassett gathered a large group of experts to discuss how to develop the program.
“We said, ‘Okay, what are all the key elements our people need to know as we’re bringing in new people and our long-term people are retiring? How do we capture all that knowledge and make sure we don’t lose anything and continue to give the customers what they need?’” she said. “We’re known for high quality and high safety, following all the codes and having good quality output, but how do you capture all that?”
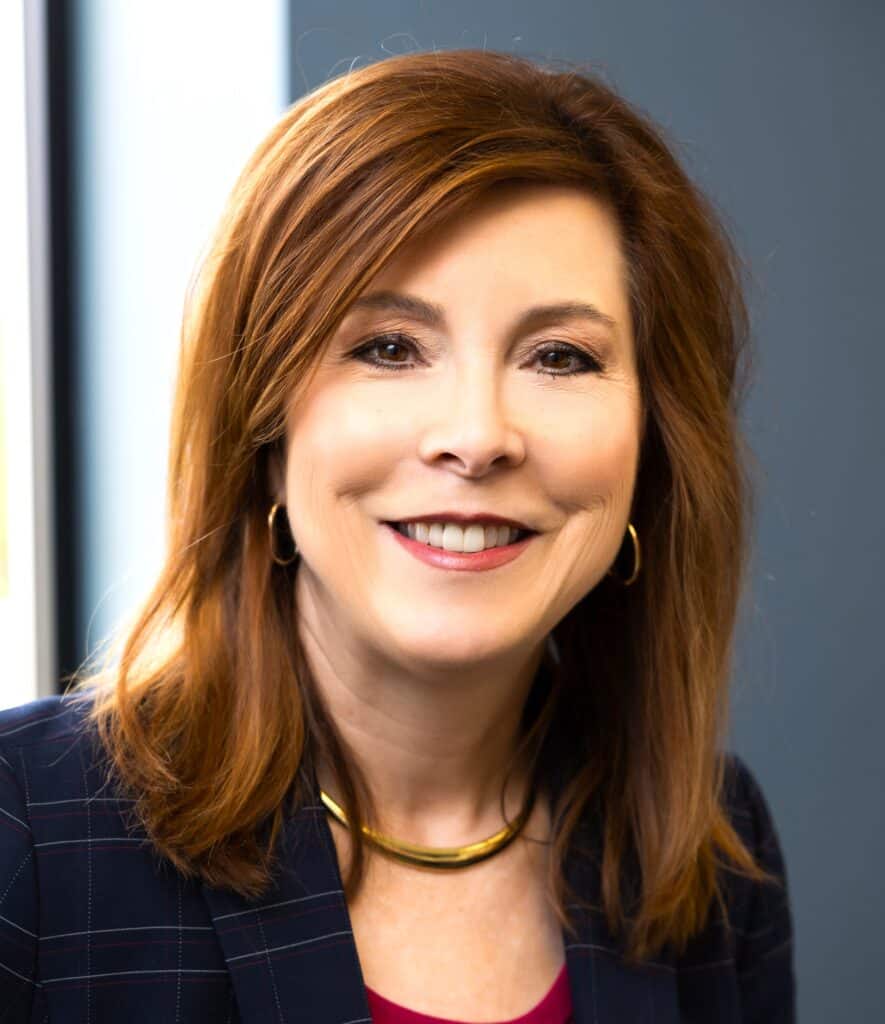
Van Ryzin said she knew Bassett was already capturing elements of passed-down expertise, but she also knew the company needed something formal to ensure it was capturing every single element.
“Creating a curriculum in a training program and (steps on) how to deliver that is a whole different animal,” she said. “I took (the training program) as far as I could, but that’s not my area of expertise.”
To help, Van Ryzin said Bassett brought on Ashley Phillips as a continuous improvement/training manager.
“Ashley is excellent,” she said. “She’s taken it to a whole new level. She began talking to all those same people and saying, ‘Okay, what is this element, or what are these elements? And then how do we pull that together in a training offering?’ She took it to a level that I didn’t have the capability of doing.”
Van Ryzin said the formal training program is for both Bassett’s engineers and technicians to ensure the transfer of knowledge and information.
The program, she said, is unique as there is no one external source for training or degrees related to ammonia refrigeration.
A variety of resources and industry associations (IIAR, ASHRAE, etc.) offer training, but Van Ryzin said nothing encompasses the breadth of knowledge Bassett’s people need to design and service the unique systems they install.
She said the training academy curriculum is delivered in-house twice per year.
Phillips said when she first started, Bassett had a “really great foundation to build off of.”
“So, I wasn’t going in blind,” she said. “I was able to partner with our refrigeration service manager, Josh Wade. He had been taking the lead on this initiative.”
Phillips said she was able to look at what Bassett currently had and then bring in an element of utilizing technology to uplift the existing program, automate more of the testing, create some of the visuals and create that curriculum the group needed.
“I was able to infuse my expertise and uplift and add to what the program already offered,” she said.
Van Ryzin said before Phillips was brought aboard, Bassett conducted any necessary training via a more one-on-one approach.
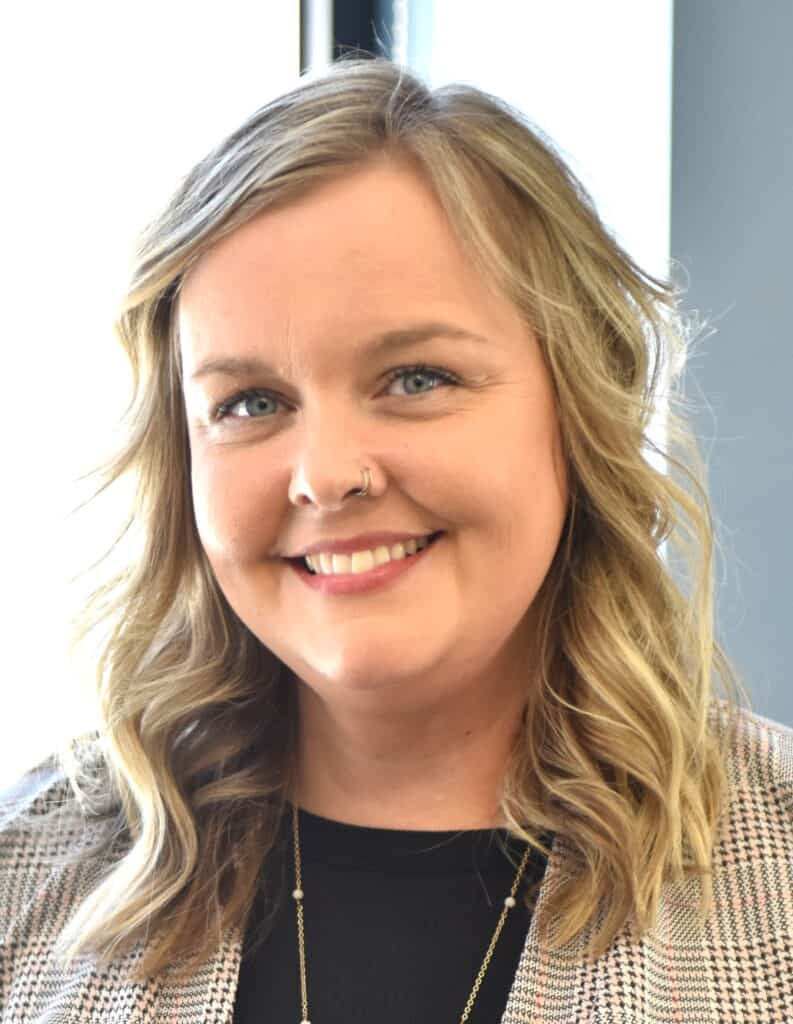
“When we would get a new employee, the supervisor and operations manager would run them through the elements we had, and then they would do the hands-on training with them,” she said. “Sometimes it took longer – to have the time to do that with them. They probably didn’t have the focused attention to all of it they should have had, so this training academy is really helping us accelerate things.”
Van Ryzin said there were eight participants in Bassett’s last training program.
“They had been in the program for different levels of time,” she said. “They were all there together, asking questions and learning from each other. We also brought in a couple of our retirees, and they helped the real experts. They helped shape the curriculum and weigh in on it, and they’re helping us do some of the training when it’s hands-on, out in the field.”
More program specifics
Phillips said to ensure “no stone is left unturned,” the training academy contains several elements.
“First off, there is a classroom component,” she said. “It’s a 40-hour, week-long training that includes in-person facilitation, video elements and some hands-on training they can do in the classroom. Once they complete the classroom training, there is a final assessment they take and pass through to the on-the-job training where they’re actually working hands-on performing the job duties under supervision.”
Phillips said upon completion of each element, “there’s some level of sign-off by their leadership.”
“That’s just to make sure they’re proficient in those skills they have,” she said. “Once they get through all the on-the-job training, then there’s an opportunity for them to get a certification. Then, as technology changes or as new topics come up, we would then bring people in and continue to train them on new or evolving technology.”
From start to finish, Phillips said it could take up to two years for Bassett employees to make their way through the entire program.
“It depends on their proficiency when they come to us,” she said. “As we’re recruiting people, they come in at all different levels. We may get someone who’s worked in a food processing plant and has a background in ammonia refrigeration – they may go on to some basic training right away. They understand the system of that plant, and we can take that knowledge and take it to the next level and show them and grow them from there.”
In the case of someone more knowledgeable, Phillips said it could be as little as six months.
“Others may take longer to really get all that hands-on, on-the-job training,” she said.
Van Ryzin said Bassett’s plethora of clients need to have “extremely qualified people working on their systems,” so that’s why the training academy is so important.
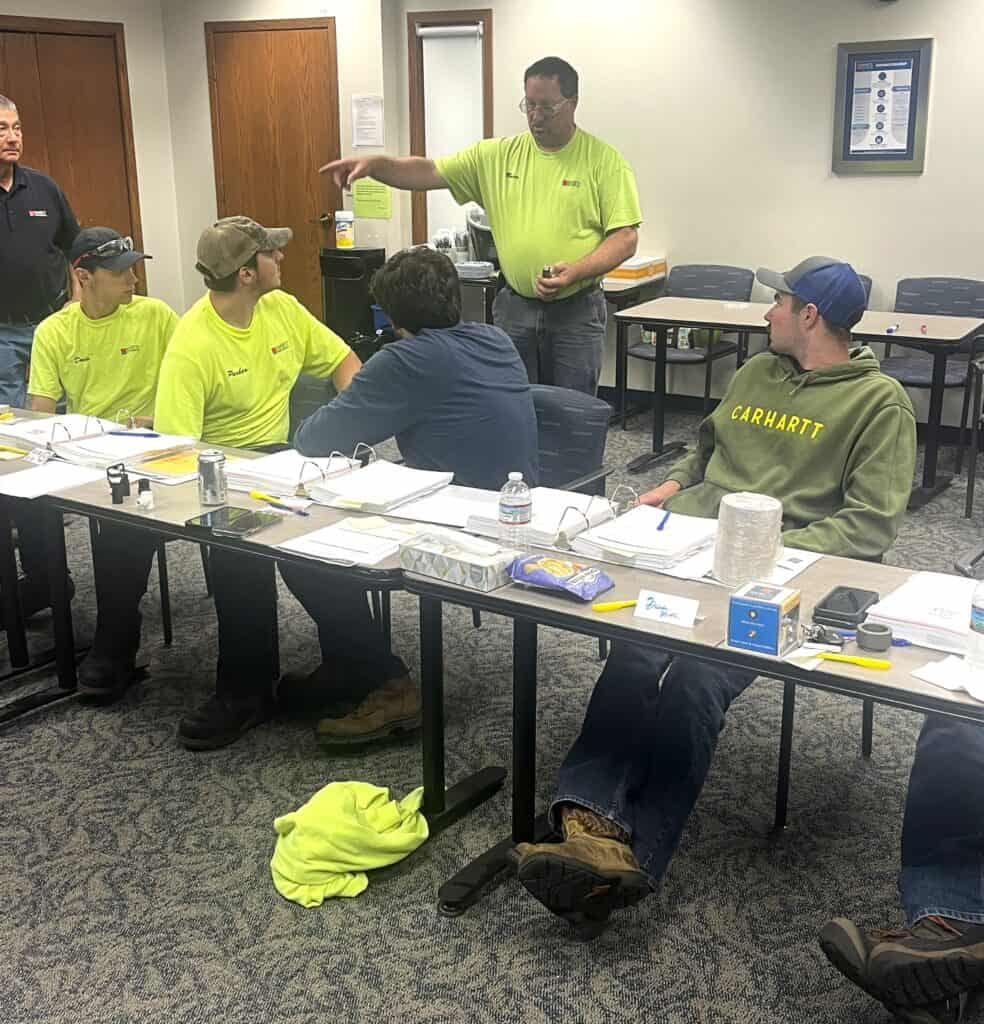
“Our different customers have different products their systems serve,” she said. “It may be something in the cheese industry where we’re cooling the product as it’s being made. It may be frozen fruits, which are all frozen at different temperatures depending on what (fruit) they are.”
Van Ryzin said Bassett has its employees actually go into the different plants to get a firsthand look at the equipment.
“They may be looking at a 50-year-old system that has old components and technology,” she said. “They have to be able to dive into that and troubleshoot what the problem is, or help maintain it. Or, it may be present-day technology from a new build. Our people are exposed to everything.”
Van Ryzin said Bassett employees need to be aware of all that different technology and be able to diagnose and help the customer solve their problems.
“It isn’t just one widget or product we’re making – our customers have such a large breadth and depth of what they do and who they serve,” she said. “Our people have to really be well versed to do that.”
Keeping it cold
Bassett has been around for almost 90 years and has approximately 550 employees, Van Ryzin said.
“Bassett was established in 1936,” she said. “We service the food industry specific to food production and storage facilities. Our expertise involves designing systems for process cooling, space cooling and freezing. Industries we serve include frozen foods, cheese and dairy, meat and poultry, beverage processing, fruits and vegetables, cold storage, ice cream and novelties and pizza manufacturers.”
Van Ryzin said Bassett considers itself more of a regional company, “but we do go national for certain customers.”
“We have some customers that have plants all over the country, and we go where we need to,” she said. “We are known on a national level, but I wouldn’t say we market ourselves to that route.”
Bassett’s approach, Van Ryzin said, is customized to the product and customer’s unique needs.
“No two systems are alike,” she said. “Ammonia is the preferred refrigerant of choice within the industrial refrigeration market, particularly the food and beverage industry. Ammonia is a natural, reliable refrigerant and is environmentally safe but also requires expertise to ensure safeguards for design and installation.”
Because of codes/safety regulations, Van Ryzin said Bassett’s teams have to have a broad knowledge base related to engineering, technology, equipment, code compliance and safety – especially Process Safety Management (PSM) related to ammonia.
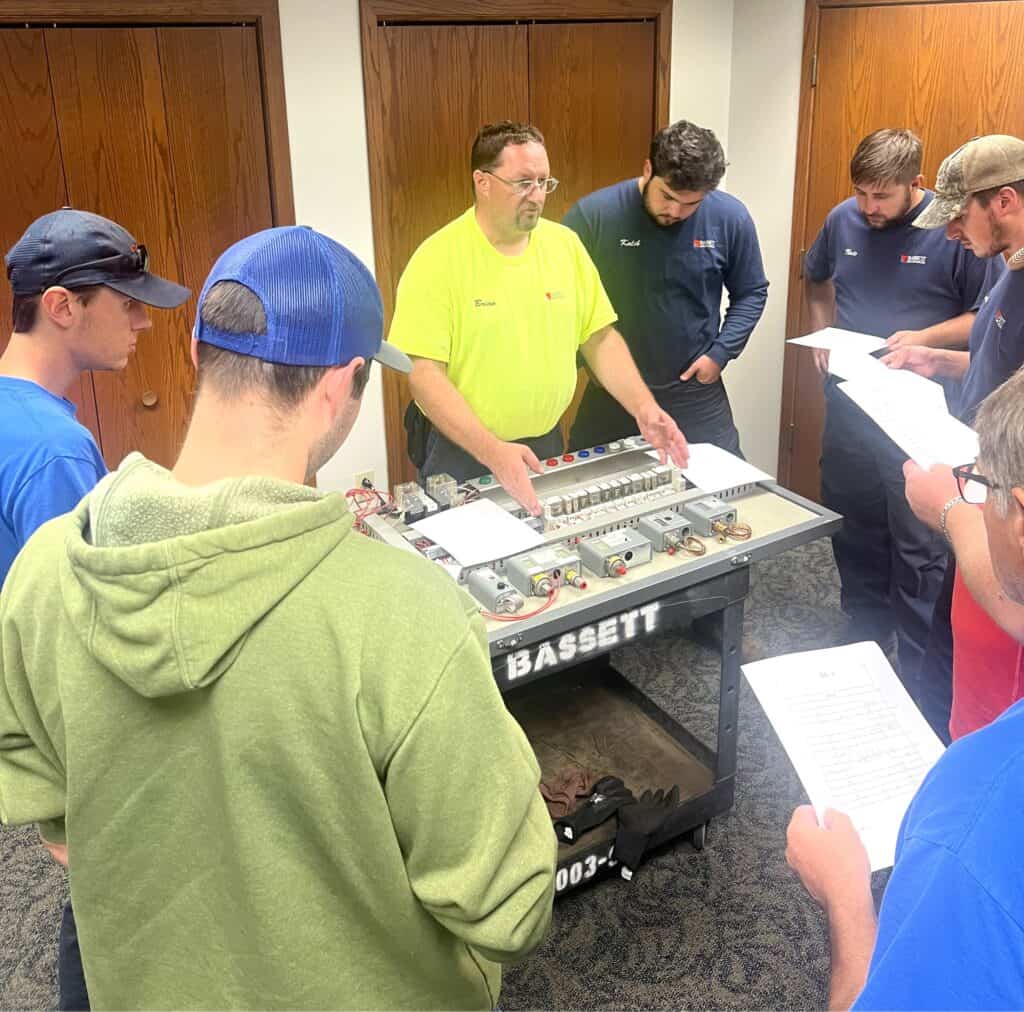
PSM, she said, is a 14-point program requiring a comprehensive safety program related to hazards, operating procedures, risk management and emergency planning.
“Teams may be working on a system retrofit to upgrade an existing system that may have older equipment and technology, or they may be designing a new system from the ground up to provide enhanced production and efficiency capabilities,” she said.
Changes in technology
With being at Bassett for more than three decades, Van Ryzin said she’s seen just about everything in terms of technology.
When she first started, she said “everything was done manually.”
“Drawings were more manual sketches, and then we got into AutoCAD,” she said. “Now that has evolved into something in the last five years called VDC (virtual design construction), with everything within like a 3D model. With VDC, you can coordinate with your other trades.”
As an example, Van Ryzin said Bassett did a large project in Minnesota two or three years ago from the ground up.
“It was for a customer who had a 60-year-old plant that wasn’t operating efficiently,” she said. “The cost to upgrade it wasn’t optimal for them, so they chose to build a new facility. That VDC allowed us to connect with all the other trades – electrical, general construction, the general contractor who builds the actual facility, the building, etc.”
It’s examples like this, Van Ryzin said, that further solidifies why the training academy is needed.
“If something is conflicting with another trade, you can figure that all out on the front end instead of on-site,” she said. “It really has been a game changer for the business to make us, as an industry, more efficient in construction.”
For more, visit bassettmechanical.com.